One of the most popular and widespread synthetic fibers in use today, nylon, is in many industries. From clothing to automobile parts, nylon has many uses, and it’s a material we’re all in the business of using. In fact, nylon was the first truly synthetic fibre, a development that was revolutionary for textiles and materials science back in the 1930s. But to see how nylon works so well, we need to go inside the chemical world of nylon – its molecular shape, the chemical reactions used to produce it, and how all these aspects contribute to the nature of nylon.
In this article we dive into the chemistry of nylon fabric. If we know what nylon is made from, its chemical structure, and the process by which it is produced, we will have a better idea of why nylon is such an adaptable substance. Let’s find out how nylon works, what its major chemical constituents do, and what chemical mechanisms work to give nylon a long, strong, malleable fiber, as well as how it affects the environment. In this dive, we’ll be able to learn more about how this synthetic stuff works, how it works, and why it is ubiquitous in textiles and beyond.
2. The Chemical Origins of Nylon
The Invention of Nylon
In 1935, the US chemist Wallace Carothers at DuPont, in his capacity as a research assistant, made a discovery that would alter the textile world. In the laboratory studying synthetic polymers, Carothers and his colleagues invented the first actual synthetic fibre: nylon. It was a game-changer, because it was the first fibre made from fossil fuels, unlike cotton, wool and silk. Carothers’ innovations created the raw materials for nylon and other synthetic fibres that would later take over the textile and industrial fabric worlds.
‘Nylon’s creation began as an effort to develop a synthetic equivalent of silk, so popular at the turn of the century, but so rare. Carothers’ group invented a polymer that could be pulled into a fibre, and turned into something that had the properties of silk but at a fraction of the price and on a massive scale. The new fibre was originally called “fiber 66,” and later became “nylon” – DuPont named it that way in 1939. Nylon first became commercialised in nylon stockings that instantly went viral. But nylon had many other uses besides the runway, and was used in everything from parachutes to industrial equipment.
Basic Chemistry: Key Components
Two chemical building blocks are the heart of nylon’s chemistry: diamines and dicarboxylic acids. They are the building blocks of the polymer.
- Diamines: These are organic molecules that have two amine groups (-NH2). The exact diamine in nylon 6,6 for instance is hexamethylenediamine (C6H12N2). It is made up of nitrogen bonded to two hydrogen atoms, and it’s very reactive in chemistry, especially when creating polymer chains.
- Dicarboxylic Acids: Dicarboxylic acids are organic molecules with two carboxyl groups (-COOH). The dicarboxylic acid that is used in nylon 6,6 is adipic acid (C6H10O4). The carboxyl group is made up of a carbonyl (C=O) and hydroxyl (-OH) group, so these molecules are extremely reactive in condensation reactions.
When diamines react with dicarboxylic acids they create amide bonds (-CONH-) in condensation polymerisation. In this reaction, one water molecule is destroyed per amide bond. It’s formed as a sequence of endless repeating units that is called a polymer and can be spun into fibres to make nylon fabric.
Polymerization Process: Condensation Polymerization
By a chemical process known as condensation polymerisation, nylon is made and this reaction affects the properties of the final nylon polymer. The condensation polymerisation occurs when two monomers (the diamine and the dicarboxylic acid) cleave together to produce a polymer and a tiny molecule (usually water) escapes as an by-product.
For nylon 6,6 the diamine (hexamethylenediamine) and the dicarboxylic acid (adipic acid) in these molecules burn into long nylon chains at a high temperature. This is the response: Let’s put it like this:
H2N(CH2)6NH2
+
HOOC(CH2)4COOH
→
[-NH(CH2)6NH-CO(CH2)4CO-]
𝑛
+
𝑛
H2O
H2N(CH2)6NH2+HOOC(CH2)4COOH→[-NH(CH2)6NH-CO(CH2)4CO-]
n
+nH2O
This reaction creates a polymer chain that is alternating with amide chains (-CONH-) between the repeated units of hexamethylene diamine and adipic acid. The longer the chains are as the polymerisation continues, the stronger the material will become. The higher the monomers, the heavier the polymer becomes, and so the stronger the nylon fibres become.
3. Molecular Structure of Nylon
Because the molecular shape of nylon is what makes it so special. The arrangement and adherence of molecules that make nylon so strong, elastic and strong is why nylon lasts so long.
Polymer Chains: Amide Linkages
Nylon is a polyamide, which simply means it’s made up of repeated units bound together by amide bonds. They’re bonds between a carbonyl atom (-CO-) of the dicarboxylic acid and a nitrogen atom (-NH-) of the diamine. These amide chains make up a recurrent element in the polymer chain, which is why nylon is so resilient.
The polymer chains of nylon are linear, so the fibre can be rolled up and twisted into fibers. Both the direction of these chains and the stiffness of the amide links are what makes nylon so strong that it can withstand high tensile forces and thus be extremely durable and resistant to degradation.
And the polarity of the amides is another factor influencing the chemical structure of nylon. All of the nitrogen and oxygen atoms in the amide links are polar, or they are slightly electrically charged. This is the polarity that lets nylon get into contact with water molecules, which absorbs moisture. That’s why nylon can trap some moisture, but it is not nearly as a water repellent as natural fibres such as cotton.
Crystallinity and Morphology
The structure of nylon fibers isn’t even. Two types of molecular shape exist in nylon: crystals and amorphous spaces.
- Crystalline Regions: These regions are highly packed polymer chains and they are very ordered – their chains are regular, repeated. The crystal layers are what make the material strong and resilient to stretching.
- Amorphous Regions: These are places where polymer chains are randomly distributed and less consolidated. The porous bits are soft and the fibre stretches and bends back.
The ratio between crystalline and amorphous parts of nylon determines its chemistry. The greater the crystallinity, the harder and stiffer the material will be; the more amorphous areas it has, the softer and more elastic the material.
The morphology of nylon means how the polymer chains are organized at the micro level. Its interface with each other – whether densely clustered crystal regions or more loosely clustered amorphous regions – makes a huge difference to the performance of the material. Fibers with more crystals, for instance, will be stiffer and less abrasive, and those with more amorphous areas will be sturdier and more comfier to wear.
Amide Linkages and Nylon’s Durability
The amide bonds in nylon are also the reason why the fiber is so strong. These bonds are dense and durable, so nylon is strong enough to withstand physical abuse, stretching and scratching. The strength of these connections makes nylon resist wear and tear over time, which is why it’s widely used in applications where the durability is important, like carpets, ropes and industrial fabrics.
This softness is another useful property of nylon that results from polymer chains. The linear chains can pass one another so that the fibre can stretch and return to its shape, not snap. This flexibility makes nylon so soft and durable, and that’s why it is widely used in flexible products like activewear, sportswear and swimwear.
4. Types of Nylon
There are different varieties of nylon which have specific applications and have special qualities. These are the two most common kinds of nylon, Nylon 6 and Nylon 6,6, but other versions like Nylon 11 and Nylon 12 come with unique properties. These different nylons and the chemistry that makes them work can tell you why some nylons make better products.
Nylon 6 vs. Nylon 6,6
Nylon 6 and Nylon 6,6 are polyamides (that is, containing long chains of amide bonds) but they are quite different in chemical composition, hence differing in properties and uses.
Nylon 6:
Nylon 6 is composed of one monomer (caprolactam) which is ring-opened to form polymers. This is by the breaking of a lactam ring in caprolactam and then a polymerisation reaction creating a long polymer chain. Nylon 6 chemical composition is:
C6H11NO
→
polymerization
[-NH-(CH2)5-NH-CO-]
𝑛
C6H11NO
polymerization
[-NH-(CH2)5-NH-CO-]
n
The polymer chain in this model is made up of repeating units of hexamethylene diamine and caprolactam. Because it consists of one monomer, the polymerization of Nylon 6 is much easier and faster than Nylon 6,6. Nylon 6 is less hot than Nylon 6,6 and it’s also generally less crystalline and therefore less stringy. But it also is more brittle and hotter than Nylon 6,6.
Properties of Nylon 6:
- Strongness: Nylon 6 is strong but not Nylon 6,6.
- Heat Resistance: Lower heat resistance than Nylon 6,6.
- Mobilitiy: Flexible and suitable for the use cases requiring extensibility.
- Typical Uses: Textile, carpet, packaging material, and industrial applications where moderate heat resistance is needed.
Nylon 6,6:
Nylon 6,6 however, is made by condensation polymerisation from two monomers, hexamethylenediamine and adipic acid. These two monomers then recombine to make an amide amide bond, yielding a very stable polymer. The composition of Nylon 6,6 is:
C6H12N2
+
C6H10O4
→
polymerization
[-NH-(CH2)6-NH-CO-(CH2)4-CO-]
𝑛
C6H12N2+C6H10O4
polymerization
[-NH-(CH2)6-NH-CO-(CH2)4-CO-]
n
“6,6”…because the diamine and the dicarboxylic acid contain six carbon atoms making it larger and more complex than Nylon 6. Nylon 6,6 polymerizes to a more crystal-like state, and therefore is tensile, abrasion and heat resistant.
Properties of Nylon 6,6:
- Thickness: Nylon 6,6 is stronger and tougher than Nylon 6, a great choice for heavy duty.
- Heat resistance: Increased heat resistance because it is more crystallized so it is good for higher temperature applications.
- Robustness: Resistant to wear, abrasion, and chemicals.
- Uses: In wide use in industrial process and auto parts, performance textiles, sportswear, parachutes, military uniforms.
There Are Two Major Differences Between Nylon 6 and Nylon 6,6:
- Polymerization Process: Nylon 6 is made from a monomer (caprolactam), Nylon 6,6 is made from two monomers (hexamethylenediamine and adipic acid).
- Chemical Composition: Nylon 6 is less crystal, it is more malleable; Nylon 6,6 is more crystal, it is strong and heat resistant.
- Performance: Nylon 6 is better for the softer applications, while Nylon 6,6 is better for heavy-duty, high-performance applications because it is strong, strong, and heat resistant.
Other Variants of Nylon
Nylon 6 and Nylon 6,6 are the most popular varieties of nylon but, for certain uses, there are others. These include:
Nylon 11 and Nylon 12:
Nylon 11: Derived from undecanoic acid, Nylon 11 is superior to cellulose fibers and is used for high chemical, oil and solvent resistance. It is often used in industrial projects like pipes, automobile parts and electrical wires.
Nylon 12: Nylon 12 also known as Dodecanoic acid. It’s more malleable than Nylon 11 and more resistant to water. It is commonly used in automotive and aerospace industries where we want something with flexibility, permeability and dimension stability.
Other Specialty Nylons:
Nylon 4,6: A nylon that is super-efficient in terms of thermal stability and durability. It’s found in engineering plastics, particularly parts that need to be extremely stiff and heat resistant.
Nylon 6,10: This nylon is a higher-performance nylon that is resistant to moisture absorption and is found in auto components and performance textiles.
5. What Are The Functions Of Additives In The Fabrication Of Nylon?
The fundamental chemical structure of nylon can be added additives to make it more effective. These additives increase the properties of nylon fabric in particular applications – for example, increasing its UV resistance, dyeability or water or flame-retardance. Additives are the key to tinkering nylon’s properties to fit different industries.
Dyes and Pigments
It’s the problem with synthetics such as nylon that they hold and soak up dyes. Whereas natural fibres like cotton or wool, for example, possess natural bonds that make dyes adhere better, nylon demands specialised chemical interventions to create vivid and durable hues.
When you dye nylon fabric, acid dyes are chemically drawn to the amide groups of polymers. Acid dyes are water-soluble and attach to the polar amide chains in the nylon fibres to give intense colours. But dying is more time-consuming and resource-hungry than dying natural fibers.
Challenges in dyeing nylon:
- Color Resistance: Dyeing has to make sure that colors will not yellow or peel in washing and wearing.
- Energy use: Dyeing nylon can use lots of energy and high temperatures to dye, which can harm the environment.
- Chemicals Employed: Dyeing and other chemicals used in dyeing process could cause pollution if not handled well.
In response to these limitations, scientists are creating less toxic dyes (low water or eco-friendly dyes) in order to minimise the ecological footprint of nylon fabric production.
Stabilizers and Antioxidants
Nylon prone to deterioration in the environment with the ultraviolet (UV) light, heat and moisture. UV exposure over time will weaken, brittle and yellow nylon fibers. Stabilisers and antioxidants are placed into nylon fibres to fend off this.
- UV Stabilizers: These substances reflect or absorb UV light so it won’t disintegrate the chains of nylon polymer. UV stabilizers are found mainly in outdoor clothing, automotive parts and textiles subject to direct sunlight.
- Antioxidants: Antioxidants are present in nylon so that it doesn’t oxidize and thus lose its qualities. These ingredients extend the life of nylon items especially in hot conditions.
Finishings and Coatings
The coatings and finishes are chemically applied to nylon fabrics for enhancement of certain performance features like water-repellency, flame retardancy or anti-static. Such treatments are common where nylon has a demanding performance requirement.
Repellence to Water: You can spray silicone or fluorochemical finishes on nylon to give it a water-repellent surface. This works best for outdoor fabrics such as tents, jackets, and backpacks that should be waterproof when it rains.
Fire Resistance: There are certain chemicals to encapsulate nylon to keep it from burning or to stop the spread of fire. Such coatings are used in protective clothing, military uniforms and upholstery.
Anti-Static: Anti-static solutions can be used for nylon to minimize static electricity accumulated in the fabric, which might be undesirable in certain environments (electronics production or fabrics used in clothing designed for specific uses).
6. Synthesis and Manufacturing Process
Whether it is a polymer that gets made and then a fabric is produced, nylon cloth has many phases. Every step contributes to the final outcome of the nylon fabric.
Polymerization of Nylon
As mentioned before, the first stage in making nylon is polymerizing monomers into the nylon polymer. Polymerisation usually happens in two steps:
Step 1: Formation of Monomers: The raw materials (caprolactam in Nylon 6 or hexamethylenediamine and adipic acid in Nylon 6,6) are mixed in a reactor. Then these compounds react chemically to create the monomers, the structural units of the polymer.
Step 2: Polymerization: Now the monomers get heated and pressured to start polymerization. Here the monomers join through condensation polymerization to make long polymer chains. They freeze the polymer chains and get a nylon polymer to make fibers from.
Spinning and Extrusion
Then the polymer can be produced and then the polymer can be converted into fibers. We do this through something called extrusion. In extrusion, the nylon polymer melts and is squidged down a spinneret — a piece of machinery with tiny holes to form the molten polymer into long, thin filaments. The fibres are cooled and solidified at the end of the spinneret.
After extrusion, the nylon fibres can be spun into yarns or threads and woven or knitted into cloth. Fabric qualities — strength, elasticity, and appearance — can be modified by changing the spin-extrusion and extrusion conditions — speed and temperature of processing the fibers.
Heat Setting
The last phase of the production of nylon fabric is heat setting. Heat setting is when the nylon fabric is heated to lock in polymer chains and stabilise the fabric shape. Heat setting is the process of releasing residual tension in the fibers, so that the fabric will still have the properties it needs (ie, strength, flexibility, shrinkage resistance).
This heat treatment also improves the fabric’s dimensional stability — it is more resilient to bending or shrinking during usage. The heat setting process is critical for making sure that the final nylon fabric will perform and last.
7. Chemical Formula that Can Help You Fabrics With Nylon.
One of the most common synthetic fibers is nylon, famous for its exceptional blend of strength, stretch, resistance to moisture and heat resistance. This molecularly derived chemical nature of nylon is the key that makes it the perfect material for so many textile purposes. Molecular ties and polymerity make nylon fibres the only kind of fibers that can change the world of industries from fashion to cars. This is where we will go into the specific chemical formula of nylon for textile use.
Hardness: Tensile Strength and Waterproof from Tear and Wear.
The main characteristic of nylon is its elasticity and thus very strong and durable as well as wear-resistant. This is why nylon is so strong: it has amide linkages that hold the monomers of the nylon polymer chain together.
Molecular Structure and Tensile Strength
The polyamide of nylon means the polymer chains are repeated unitary units of amide bonds. These amide chains are produced by condensation polymerisation: monomers such as hexamethylenediamine and adipic acid (Nylon 6,6) join to create longer molecular chains. These long, repeating amide units are very durable and strengthen the material.
These polymer chains are very tightly arranged and highly structured in nylon – especially Nylon 6,6 which is a bit crystalline in contrast to other types of nylon. This crystallinity gives nylon its improved tensile strength, so that it can take a lot of mechanical abuse without tearing. The result is a textile suitable for high-wear fabric, for example in outdoor clothing, industrial fabrics and automobiles.
Resistance to Abrasion
Nylon is abrasion-resistant as well as tensile-resistive, which is important for fabrics that will be subject to high wear. The tightly packed and strong polymer chains prevent friction and rubbing forces that would otherwise breakdown fibres. That’s what makes nylon fabrics resistant to washing and using them repeatedly, in the outdoors, or against rough objects.
High tensile strength and abrasion resistance make nylon an excellent material for clothing and materials that must be kept looking and working good for long periods of time.
Elasticity and Tension: The Function of Polymer Structuring
This is the other fundamental quality of nylon — its elasticity and softness. Nylon is not only hard and resistant to damage, it is also elastic and will hold its shape after it has been stretched. Such properties are necessary for fabrics for activewear, swimming wear, socks and other items that need to move.
Polymeric Chain Structure and Flexibility
Nylon is elastic because of the polymer chain structure. Polymer chains are long, elastic polymers which are neither glued nor twisted. These chains stretch and bend without breaking because their amorphous parts deform the polymer. In the case of nylon, if it is under pressure, its polymer chains may pass each other for a moment, causing the fibre to stretch. When they take the stress off, the polymer chains move back where they came from and the fabric regains its shape.
Besides, nylon’s stretch makes the fabric more comfortable to wear. It can stretch without sagging or tearing, which is perfect for applications such as sports wear where elasticity is critical. Nylon-blend fabrics, for instance, are common in leggings, athletic tops and swimmingwear because they stretch and come back into shape.
Resilience and Memory
It is not only polyesters that have resilience, but also nylon fabrics because they recover their form when stretched or compressed. The nylon fibers are elastic when they re-entrain, a quality that’s useful for clothing that needs to keep its shape and avoid wrinkles.
Resilience to Water: Water-Resistant Nature and Application In Many Environments
Nylon is hydrophobic, i.e. This abrasion resistance plays an important role in fabric’s functionality, especially in fabrics employed in moist areas, such as clothing for outdoor wear, athletic wear, upholstery.
Chemical Structure and Water Resistance
This is because nylon is a molecular material. Nylon’s amide bonds are polar but polymer chains are protected by non-polar hydrocarbon groups, so water molecules can’t just seep into the fabric. This makes nylon anti-absorption and quick-drying.
Because nylon doesn’t absorb water, it doesn’t become bulky or heavy and it is used for everything from swimwear to camping rigs and backpacks. Additionally, nylon’s water repellent properties also keep mold or mildew at bay in areas where humidity is high – which is especially relevant when you’re doing outdoor stuff.
Performance in Wet Conditions
Not only is nylon water repellent, nylon is able to withstand the wet better because of its low moisture resorption. Although most fibres (eg, cotton) will hold water and begin to shrink or deform when they get wet, nylon stays sturdier under wet conditions. That means it is highly durable in all kinds of places where water gets exposed regularly – for example, on boats, on hikes, and even in industry where dampness is a frequent occurrence.
Heat Resistant: Nylon Resistance to Heat.
Nylon is very thermally resistant too which makes it suitable for high temperature use. Its heat resistance is crucial in textiles for industrial applications or applications where heat is a frequent factor (e.g., automobile, aerospace, protective garments).
Melting Point and Heat Resistance
The melting point of nylon will vary with nylon type. The melting point of Nylon 6 is for instance about 220°C whereas the melting point of Nylon 6,6 is about 260°C. It is because of a difference in the crystallinity of the two forms of nylon that there is a difference in melting points. The more crystallized nylon 6,6 can be heated up further without cracking.
These porous zones in nylon give it some modulus under extreme heat. These places help the material stay round and elongated even under very high temperatures. If textiles are to be used in high-temperature environments, like protective clothes, hot-wire cables or automobile bodywork, then heat resistance of nylon is a must-have quality.
Thermal Stability in Textile Applications
In the textiles industries – fashion, interiors – nylon’s thermal stability is part of the reason why it looks and performs so well in extreme temperatures. This is what makes it perfect for fabrics that need to keep their shape under heat — upholstery, carpeting, high temperature industrial textiles.
8. Chemistry Problems in Nylon Fabric: Defibrillation.
Nylon’s chemical properties make it flexible and durable, but it isn’t without challenges in its manufacture and usage. These issues mostly have to do with nylon’s environmental footprint, sustainability issues and its environmental relationship.
Impact On Environment: Incompatible With Biodegradability & Microplastic Degradation
Among the worst issues with nylon is its inbiodegradability. The fibers of nylon do not break down in nature, so any nylon waste builds up into the long-term. Because nylon is a synthetic fibre that’s produced from petroleum chemicals, it’s environmentally unsustainable, especially in the textile sector, which is the biggest contributor to the global waste dump.
Microplastic Pollution
There’s also the threat of microplastic contamination. When nylon garments are washed or soiled, little fibres will separate and fall out into the world – sometimes into rivers, oceans and rivers. These microplastics are a big environmental problem, they’re hard to remove from the water and they could get eaten by marine animals, thus entering the food supply.
Waste Accumulation and Landfills
As nylon is not biodegradable, it also feeds into the burgeoning issue of textile waste that finds its way to landfill. The same materials take centuries to break down – such as nylon. With the fashion industry growing and more and more consumers looking for products made from nylon, the problem of waste is now at the centre of sustainable living.
Eco-Activities: Recycled Nylon and Alternative Bio-Drawn Components
There are many sustainability projects undertaken to lessen nylon’s ecological footprint by developing greener alternatives and reducing nylon’s overall environmental footprint.
Recycled Nylon
But the latest development looks promising: recycled nylon. Recycled nylon is produced by transforming nylon wastes, like old clothing, used fishing nets and industrial wastes, into new fibres. This eliminates virgin nylon production which consumes more resources and is environmentally damaging.
Companies like Parley for the Oceans and Nylon 6,6 Recycling are pioneering the recycling of recycled nylon into new textiles. As recycled nylons can also be reused, these projects reduce petroleum-based nylon consumption and lower carbon emissions.
Bio-Based Nylon
An even better solution to make nylon more sustainable is to make nylon with bio-technology. Bio-based nylon is not manufactured using petroleum but renewables (eg, plant feedstocks). Nylon 11, for instance, which is a synthetic of castor oil, is less derived from fossil fuels and a cleaner alternative to standard nylon manufacturing.
9. The Future of Nylon Chemistry
As the market for sustainable and performance textiles continues to increase, the future of nylon chemistry is transforming for the benefit of the textile industry and the environment. The future of nylon manufacturing is sustainable, effective and practical.
Smart Textiles: Blending of Cutting Edge Technologies
Perhaps the biggest thorn in the side of nylon’s bow is the future of smart textiles embedded within nylon fabrics. Smart fabrics build sensors, conductors, even self-healing materials into the nylon fibre structure. These fabrics could revolutionise everything from medicine to fashion to sport.
Wearable tech can, for instance, be programmed into nylon materials to monitor wearer health, measure movement, or even transform the fabric’s properties in the presence of changes in the environment. They are also creating self-healing nylon, whose material can heal itself when damaged, so no more replacement is required and less waste is produced.
Biodegradable Nylon: Future Directions
With nylon’s harmful effects on the environment at play, scientists are trying to develop biodegradable nylon. Polymer chemistry is leading to nylon derivatives that can degrade naturally in the environment. That might lessen the environmental burden of unbiodegradable nylon and the landfill of textile waste.
Eco-Friendly Manufacturing Techniques
Besides innovation in the fabric, there is also a race to find more sustainable manufacturing methods for nylon. They’re experimenting with waterless dyeing, energy savings during polymerisation, and closed-loop recycling of waste to make nylon manufacturing more environmentally friendly.
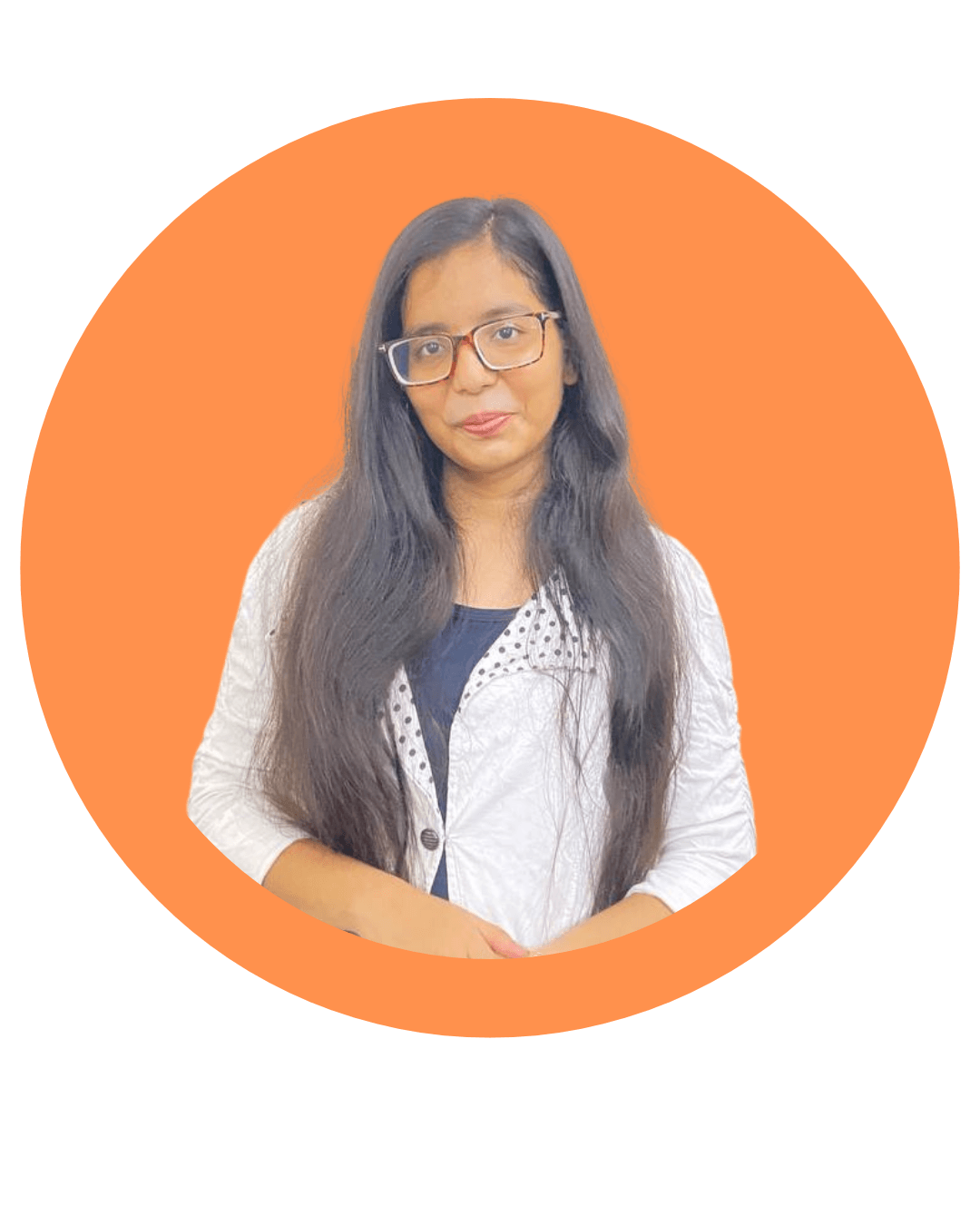
Yashvi Jain, a writer by day and reader by night, is an accomplished content writer and published author of ‘Mind Under Construction. Yashvi possesses extensive knowledge of fabrics, sustainability, and literature. On occasions, you would catch her scripting for her YouTube channel, engrossed in fiction, or ardently dedicating her time to research and storytelling.