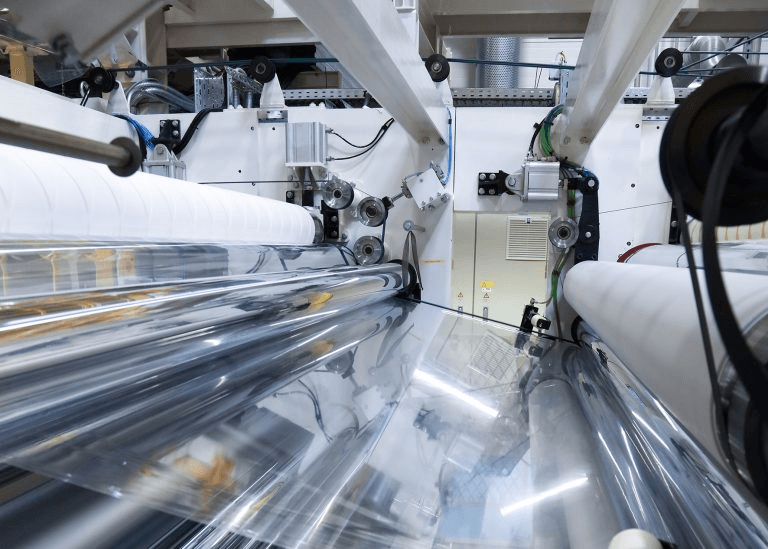
I. Introduction
Nylon has always been one of the most popular materials in the current market due to its versatility, strength, and resilience. From fabrics and carpets to car parts and industrial equipment, nylon’s ubiquity reflects its place in everyday life. But its environmental impact is challenging.
- Overview of Nylon’s Environmental Impact
Fossil Fuel Dependency:
Nylon is a synthetic polymer produced from petrochemical raw materials such as crude oil. Mining and processing these materials are both high sources of carbon emissions and resource loss.
High Energy Consumption:
Nylon manufacturing is energy-intensive: it requires high temperatures and pressures to polymerise. This energy use typically is fueled by fossil fuels, thereby increasing its carbon footprint.
Harmful Byproducts:
The most alarming byproduct of nylon production is nitrous oxide (N2O), a greenhouse gas about 300 times more powerful than carbon dioxide in terms of global warming.
- Global Demand for Nylon
Demand for nylon extends across the value chain:
Textiles and Fashion: Used in clothing, hosiery and sportswear for its elasticity and strength.
Automobile Industry: Nylon is used in lightweight components, which enhances the vehicle’s fuel economy.
For Industrial Use: Conveyor belts, ropes, and components of machines.
This widespread use underlines the need for ecologically sound production processes that can both limit environmental damage and ensure supply.
Also Read : Nylon’s Carbon Footprint: Can It Be Reduced?
- Purpose of the Article
This paper explores how technology is responding to the environmental impact of nylon production. It brings forward advances in materials, processes and recycling practices that could lead to a greener future for synthetics such as nylon.
II. Advances in Sustainable Raw Materials
Bio-Based Nylon
Perhaps the most likely path to reduce nylon’s ecological footprint is the creation of bio-based alternatives. These processes substitute fossil fuels with a renewable source such as castor oil, algae or sugarcane.
Technologies in Bio-Based Nylon
- Castor Oil as a Feedstock:
Bio-nylons like Arkema’s Pebax Rnew are made with castor oil, extracted from the seeds of the castor plant.
Castor grows on small patches of land and doesn’t require much water, which makes it an environmentally sound crop.
- Algae-Based Nylon:
For the nylon precursors, scientists are exploring algae as a feedstock. Algae-based solutions could take up CO2 as they grow, thus mitigating net carbon losses.
- Sugarcane-Derived Nylon:
Technologies exist to turn sugarcane into the chemicals for nylon. It takes advantage of sugarcane’s renewable status, and offsets carbon through photosynthesis.
- Environmental Benefits of Bio-Based Nylon
Lower Carbon Footprint: Renewable feedstocks trap CO2 as they are growing, offset in part by production emissions.
Liberation from Fossil Fuels: Going renewable reduces dependence on finite reserves of oil.
- Case Studies in Bio-Based Nylon
Arkema’s Pebax Rnew: Biobased nylon derived from castor oil, used in sportswear, electronics and industrial garments. It provides a lower carbon footprint without compromising performance.
DuPont’s Sorona: Not nylon, but a bio-based polyester that demonstrates how renewable feedstocks can transform synthetic polymer production and set a precedent for bio-nylon technologies.
Recycled Nylon
Turning nylon waste into new materials is another important way to mitigate its impact on the environment. Both mechanical and chemical recycling technologies are being streamlined to make them more efficient and scalable.
Mechanical Recycling
- Process:
Mechanical recycling involves taking post-consumer and industrial nylon waste, purifying it, and melting it down into new nylon.
- Applications:
Used in repurposing fish nets, carpet fibres and fabric.
- Challenges:
- Mechanical recycling reduces nylon’s reuse potential by reducing quality.
- Intacting waste streams with other material can make the job harder.
Chemical Recycling
- Process:
Chemical recycling reduces nylon waste to the molecular components that make it up, like caprolactam (Nylon-6). These monomers can be cleaned up and recombined into fresh nylon, effectively sealing the production chain.
- Advantages:
Restores the material to virgin quality.
Allows the recovery of mixed or polluted waste streams.
- Technological Innovations:
High-tech depolymerization methods optimize yield and reduce energy.
Disruptive Sorting and Recycling Methods
- AI-Powered Sorting:
Using AI to detect and isolate nylon from combustible waste streams, improving the quality and productivity of recycling.
- Infrared Spectroscopy:
High-speed, high-quality NIR spectroscopy to recognise nylon waste can reduce the need for lengthy efforts to recycle it.
- Environmental Impact of Recycled Nylon
- Reduced waste: Recycling helps divert huge quantities of waste from landfills and oceans.
- Reduced Carbon Emissions: There is less carbon emissions from recycled nylon production than from virgin nylon, especially in closed-loop systems.
Case Studies in Recycled Nylon
- Econyl by Aquafil:
- Made from 80% used nylon waste (from fishing nets to carpet).
- Used by brands such as Prada and Adidas, it shows versatility in fashion and sportswear.
- Patagonia’s Recycled Nylon Initiative:
The adventure brand uses recycled nylon in its products to offset their use of virgin fabrics.
III. Green Chemistry Advances in Nylon Fabrication
Nylon is a polymer that is found in everything from clothes to cars. But its environmental footprint, in particular its carbon dioxide and toxic byproducts, have led to calls for more sustainable production. Incorporating green chemistry technologies offers the most promising way to reduce nylon’s ecological footprint. All of these developments aim to reduce the impacts of nylon manufacturing on humans and the environment. Below, we see how green chemistry is transforming nylon manufacture with catalytic, energy-efficient, and biotechnological methods.
Catalytic Technologies
Traditional nylon production is among the most environmentalally destructive – emitting nitrous oxide (N2O), a greenhouse gas that accelerates global warming. It is the byproduct that is formed when nylon is sprayed into a polymer to produce Nylon 6. The new catalytic technologies have produced significant strides toward eliminating nitrous oxide and other toxic emissions.
Sensitivity To Oxygen Emissions Reduction With High Performance Catalysts
Nitrous oxide (N2O) is produced in the reaction that creates caprolactam, the raw material used to manufacture Nylon 6. In terms of its global warming capacity, N2O is around 300 times more powerful than carbon dioxide. Scientists have created new catalytic reactions to minimize, or even eliminate, nitrous oxide emissions during manufacture. Such reactions use more sophisticated catalysts to achieve better chemical reactions, reducing the amount of nitrous oxide produced without decreasing the quantity of nylon produced.
- Selective Catalytic Reduction (SCR):
A technique for curbing nitrous oxide emissions is selective catalytic reduction, in which a catalyst dissolves nitrous oxide to give off nitrogen and oxygen and release it into the atmosphere unharmed. This has been used successfully in many sectors, including nylon manufacture.
- Electrocatalytic Processes:
Electrocatalysis, a technique for using electricity to initiate chemical reactions, has shown promise in reducing emissions in the production of nylon. By using electricity to convert the raw materials, we could yield caprolactam that emits less nitrous oxide and other pollutants.
- Hybrid Catalytic Processes:
Multiple catalytic reactions in a single reactor increase reaction efficiency, energy consumption, and byproducts produced. For instance, replacing an older catalyst with a greener version would cut nitrous oxide emissions without raising costs.
Such catalytic breakthroughs mark a significant development in the push towards more sustainable nylon production. By eliminating the damaging emissions from conventional nylon production, these technologies reduce the industry’s carbon footprint.
Examples of Chemical Activities that Reduce Dangerous Outcomes
Green chemistry technologies also reduce the production of other pollutants that typically come out of nylon production, including nitrous oxide. New, environmentally friendly catalysts can also eliminate the use of toxic chemicals like chlorine and hydrogen chloride, typically generated during the manufacture of nylon.
- Green Solvents:
Conventional nylon manufacturing typically uses toxic and harmful solvents that are dangerous to the environment and employees. The production of green solvents, which are environmentally benign and biodegradable chemicals that come from renewable resources, promises an alternative that is safer. These solvents are useful for the extraction and production of nylon but pose far less environmental hazards.
- Zero-Waste Catalysis:
In addition, we are creating new catalytic reactions that leave little or no waste out byproducts. With catalysts working at lower temperatures and pressures, energy is conserved and unwanted side products are minimized. These processes conform to the ideals of green chemistry by maximising efficiency and minimising the footprint.
Energy-Efficient Manufacturing
Energy consumption is one of the biggest environmental impacts of traditional nylon production. Polymerising nylon requires extremely high temperatures and pressures, typically obtained through combustion of fossil fuels. During an era when sustainability is the world’s obsession, it’s more critical than ever to use energy-efficient manufacturing processes.
Acceptance of Low-Temperature, Low-Pressure Polymerization Technologies.
Low-temperature and low-pressure polymerisation technologies remain one of the most promising breakthroughs in the quest for a better energy-efficient production of nylon. These techniques employ new catalysts and new reaction mechanisms to reduce the energy required to turn the raw material into nylon. By eliminating the requirement for high temperatures and pressures, manufacturers can significantly cut energy consumption, thereby reducing greenhouse gas emissions.
- Enzymatic Polymerization:
Enzymatic polymerization is a relatively new method of polymerizing nylon precursors by converting them into enzymes that act as catalysts. Enzymes work at room temperature, which dramatically minimizes the energy consumed by the process. Even in the experimental stage, this process offers great potential for future industrial scale use.
- Solvent-Free Polymerization:
Traditional nylon manufacturing uses solvents to dissolve and purify raw materials. Yet solvents present additional environmental hazards, both in the form of waste and toxicity. There are solvent-free polymerisation technologies under development to remove these chemicals from the process, further reducing the carbon footprint of nylon production. Such reactions employ solid-phase reactions or supercritical fluids instead of solvents to conserve energy and avoid pollution.
Closed-Loop, Solventless Waste- and Energy-Saver Systems.
In addition to solventless operations, closed-loop systems are increasingly used in nylon manufacturing. A closed-loop system is one in which the waste products and byproducts are captured and reused during production, so that less waste is produced and less raw material input is required. Such mechanisms greatly minimize the net environmental footprint of nylon manufacture by lowering the use of energy and natural resources.
- Recycling in the Production Cycle:
Some are even turning to closed loop technologies that recycle nylon waste and recycle it into new products. This not only saves the amount of waste produced but also lowers the requirement for raw materials which preserves the environment.
- Energy Recovery:
Closed-loop systems also recover energy from waste streams. For instance, any heat that is generated during manufacturing can be stored and reabsorbed into the manufacturing process, thus minimising the demand for external energy sources.
These breakthroughs in energy-efficient production can dramatically lessen the environmental footprint of nylon production and render it more sustainable in the long run.
Biotechnological Approaches
Biotechnology is emerging as a viable alternative to the increasing worries about the ecological footprint of traditional nylon manufacturing. Drawing on the energy of engineered microbes, researchers are trying to find new ways to generate nylon precursors from sources that are renewable and not oil.
Engineered Microorganisms Producing Nylon Precursors
Nanoparticles containing precursors of nylon are a recently emerging, rapidly advancing field of science. Engineered microbes, like bacteria or yeast, could be programmed to generate the chemical building blocks of nylon from renewable feedstocks. Such microbes are capable of digesting plant sugars or waste materials, and converting them into the chemicals required to produce nylon, greatly decreasing dependence on petroleum.
- Bio-Fermentation to Replace Petroleum-Based Synthesis:
Bio-fermentation, which exploits microorganisms to transform organics into useful chemicals, has enormous promise as a means of displacing the petroleum-based synthesis of nylon precursors. Scientists are developing biotechnological pathways to create caprolactam (the main raw material for Nylon 6) through fermentation, thereby bypassing fossil fuels.
- Examples of Biotechnological Developments:
DSM and Genomatica: DSM, the world’s largest supplier of sustainable materials, has teamed up with the biotech firm Genomatica to create a bio-based version of caprolactam. This technology aims to offset the carbon emission of nylon production by replacing petroleum feedstocks with renewable sources.
LanzaTech’s Carbon Recycling: LanzaTech leverages microbial fermentation to transform industrial carbon dioxide from combustion into valuable chemicals such as those used to produce nylon. This technology can collect and recycle waste carbon, thereby reducing emissions and creating a circular carbon solution.
Such biotechnological techniques could transform the nylon industry, bringing cleaner, biobased alternatives to traditional petroleum-based nylon production.
IV. Technology-enabled Circular Economy Methods
Apart from green chemistry, technology is one of the key factors driving circular economy in the nylon industry. If we are thinking about product design for recycling, closed loop production, and smart waste, the industry will be able to move towards a more sustainable future.
Product Design for Recycling
One of the most important pillars of a circular economy is the recycling of products at the end of life. Design advances ensure that nylon products are easier to recycle, making them less wasteful and resource-saving.
- Monomaterial Designs:
When we create products that are made from only one material – monomaterial designs – recycling becomes easier. By producing pure nylon or blending it with easily separated materials, manufacturers can avoid contamination in recycling systems, making nylon easier to recycle.
- Digital Product Lifecycle Management Tools:
Softwares such as lifecycle analysis programs and product design programs are being implemented to ensure the sustainability of nylon products right from the outset. They enable manufacturers to estimate the environmental footprint of a product throughout its lifecycle and design it to become recyclable.
Closed-Loop Manufacturing Systems
Closed-loop manufacturing technologies have become the new standard for sustainable nylon manufacture. Such mechanisms provide the capability to reuse material throughout its lifecycle — drastically reducing waste and CO2 emissions.
- Aquafil’s Econyl Process:
Aquafil invented the Econyl process, whereby used materials like discarded fishing nets and repurposed carpets get recycled into durable nylon. This closed loop model makes sure these resources are reused time and again, preventing them from ending up in landfills and creating demand for new raw materials.
- Textile Recycling Innovations:
Textile recycling has made it possible to extract nylon fibres from textiles and garments. Not only does this keep nylon products in production, it reduces the need for virgins.
- Smart Waste Management Solutions
The AI and machine learning technologies are transforming the waste systems to help sort and process nylon waste more effectively. These advances maximize recycling rates and contribute to the reduction of the percentage of nylon that ends up in a recovered and reused state.
- AI-Powered Sorting:
Ai can distinguish between nylon waste, making it easy to sort and recycle. Machine learning algorithms can improve sorting over time, creating more efficient and clean recycling processes.
- Blockchain for Transparent Recycling:
You can trace the supply chain of recycled nylon materials using blockchain technology for transparency and accountability. This allows consumers and manufacturers to see how much nylon is recycled, thereby strengthening sustainability statements.
V. Renewable Energy Adoption In Nylon Manufacturing
With nylon production becoming increasingly sustainable, manufacturing will need to incorporate renewable energy sources to reduce carbon emissions. Neylon plants are now using solar, wind and other green energies to reduce the need for fossil fuels.
- Solar and Wind Power Adoption
Nylon-producing factories increasingly use clean energy sources, such as solar and wind. These fuels lower the carbon footprint of conventional nylon production and help manufacturers achieve their sustainability targets.
Renewable Energy Use in Nylon Manufacturing Case Studies:
Many nylon manufacturers are turning to renewable energy. Aquafil, for instance, uses renewable energy to generate Econyl, reducing its carbon emissions significantly. In the same vein, Nylstar, the world’s largest nylon producer, has added solar panels to its production facilities, reducing its dependence on fossil fuels.
- Energy Storage and Efficiency Technologies
Innovative storage and efficiency technologies help factories to tap renewable energy more reliably, even when the sun is not out and the wind is not blowing. We’re building battery storage systems to hold the surplus power from solar and wind power so that plants don’t need to run on non-renewable energy sources.
VI. Emerging Applications of Eco-Friendly Nylon
In a world increasingly concerned about sustainability, the nylon industry is responding to environmental demands. The introduction of sustainable nylon has inspired numerous new applications to mitigate the ecological footprint and optimize the function and performance of nylon products. From sustainable smart textiles to green engineering using nylon composites, environmentally friendly nylon’s new uses are reshaping fashion, sportswear, automobiles and construction.
- Sustainable Smart Textiles
Smart fabrics have seen major advancements in the textile industry in recent years. These textiles combine technical functions including temperature regulation, moisture management and even biomedical monitoring features, but they are made from renewable resources. Sustainable smart textiles set the pace in integrating textile performance with sustainability. Non-toxic nylon is an important component of these innovative fabrics.
combining of functionalities with Environmentally Sustainable Production.
Smart textiles are designed to improve the feel and performance of fabrics by offering moisture-wicking, thermal management, and even self-cleaning. For a long time, such textiles have been produced using synthetic fibres such as nylon, which although flexible and hard-wearing have also been condemned as being damaging to the environment. But thanks to sustainable nylon manufacturing techniques, producers are now able to produce smart fabrics that offer performance without compromising on sustainability.
- Temperature Regulation and Moisture-Wicking Fabrics
Sustainable smart fabrics such as those found in sportswear and activewear are built around moisture-wicking fabrics that retain comfort by wicking sweat away from the body. By using sustainably manufactured nylon that is bio-based or recycled, these fabrics provide moisture management without the environmental degradation associated with traditional nylon manufacturing.
Sustainable nylon, for instance, can be incorporated into clothing that regulates body temperature to keep you warm. New smart textiles coated with phase change materials (PCMs) are being made out of sustainable nylon fibers. These fabrics hold, conserve and release heat as the temperature changes, with significant benefits for both performance and sustainability.
- Health and Performance Monitoring
With the advancement of wearables, sustainable smart textiles are paired with sensors that record heart rate, body temperature and movement. They’re commonly integrated into wearables, health apps, and athletic wear. Through the usage of sustainable nylon in these garments, designers can reduce the clothing’s carbon footprint and improve its function.
- Integration with Circular Economy Practices
The greatest potential of sustainable smart textiles lies in the ability to support circular economy practices. By using nylon made from recycled materials or bio-based feedstocks, manufacturers make products that have a more sustainable life cycle. Such fabrics can be recycled or repurposed in the post-consumption process, reducing waste and preserving resources.
Brands Who Use Smart Nylon Fabrics Sustainable Sustainability Smart Nylon Fabrics: Examples of Brands With Smart Nylon Fabrics Sustainability
Some brands are taking the first step toward using recycled nylon for smart clothing and sportswear. Not only are these brands using environmentally responsible manufacturing practices, they are also producing textiles that lead to more functional and performance-enhancing designs.
Patagonia
Patagonia is one of the most prominent fashion and outdoor brands that embrace sustainability. They’ve incorporated recycled nylon into their apparel and equipment, including performance and utility gear. Patagonia also extracts nylon from post-consumer waste – including fishing nets – and integrates it into outdoor gear. Many of their designs have moisture-wicking and temperature-regulating qualities, smart textile details and eco-friendly nylon fabrication.
Athleta
Activewear brand Athleta also adopted smart textiles by using recycled nylon fabrics for workout wear. The brand makes moisture-wicking, breathable, and temperature-regulating sports apparel from environmentally sound nylon fibers. These fabrics can be used to make high-performance garments, for both athletes and consumers, that don’t require virgin nylon and offer enhanced comfort and function.
Uniqlo
Uniqlo has been making significant efforts to include sustainable products in its product portfolio. Their “BlockTech” jackets, for instance, are crafted from environmentally friendly nylon that is both water resistant and windproof, enabling it to function in all conditions. Uniqlo’s use of bio-based or recycled nylon reduces the environmental footprint of their outerwear without sacrificing performance.
- Green Engineering with Nylon Composites
Nylon is also paving the way in the automobile and construction industries where light, durable and recyclable materials are in high demand. In these industries, nylon composites – composed of nylon bonded with glass or carbon fibres – are increasingly used for their superior mechanical performance. By minimizing material usage and improving recycling rates, eco-friendly nylon composites are making the engineering in these industries more sustainable.
Automotive and Construction Industry Applications :
- Automotive Industry
Automobile manufacturers have used nylon composites to build lightweight parts including interior doors, underbody assemblies, and paint. These parts provide exceptional strength and durability with minimal vehicle weight resulting in improved fuel efficiency and emissions. As the industry evolves toward sustainability, nylon composites that are made from recycled or bio-based materials are in high demand.
Examples: Recycled Nylon for Auto Accessories.
Some car makers are even inserting recycled nylon into the parts of their cars. For example, automakers such as BMW are now fabricating parts for their vehicles out of recycled nylon produced from post-consumer material, like bottles and discarded fabrics. This not only reduces the waste generated in landfills but also decreases the production’s carbon footprint.
- Construction Industry
In the building sector, nylon composites are used for reinforcement, pipes and insulation. By making materials out of recycled nylon, developers are minimising the carbon footprint of construction projects. Nylon composites are lightweight and durable, which makes them ideal for sustainable construction, saving material and helping create efficient buildings.
Example: Ecological Construction Using Nylon Composites.
Honeywell and others are generating sustainable nylon composites for the construction industry. These composites can be integrated into insulation materials that are not only energy efficient, but also have a lower carbon footprint than standard insulation materials. As nylon composites can be recycled at the end of their useful lifecycle, it is attractive for use in sustainable building projects.
Material Performance Improvements At Low Environmental Costs
In an ever-evolving nylon composite, much has been achieved with respect to both material performance and the environmental footprint. Advances in nylon composite recycling and removing toxins from the mix has opened the way to more sustainable options.
- Enhanced Durability
New polyamide composites are being developed to improve efficiency and strength. Combining nylon with another fibre, like carbon or glass, yields materials that are more robust and resistant to wear. This strength eliminates frequent replacement and decreases the overall amount of material needed.
- Recycling of Nylon Composites
The recycling of nylon composites is a major research issue. Through chemical recycling techniques, nylon is recovering from composites at the end of their life cycle so that manufacturers can recycle it for a new purpose. Nylon composites can also be recycled more effectively, and used in closed-loop processes, further reducing their impact on the environment.
VII. Challenges and Limitations
While the new applications of natural nylon sound promising, a number of barriers are still in place to commercialize such innovations and deal with the greater environmental footprint of the nylon industry. The shift to sustainable technologies comes with challenges – from the cost of manufacturing to consumer education.
Transition Costs to Renewable Technologies?
The biggest impediment to the mass adoption of sustainable nylon is the price that comes with switching to sustainable technology. It isn’t always cheap to invest in R&D and retrofit existing manufacturing plants. Such transformations can be a challenge for companies who’ve operated around old-fashioned nylon manufacturing.
- R&D and Infrastructure Costs
Bionylon, chemical recycling and environmentally sound manufacturing techniques all involve significant R&D investments. Moreover, modernising manufacturing sites to use these new technologies requires huge capital investments. Small companies and manufacturers in developing countries might not be able to make such investments, and this could hold up the global march towards sustainable nylon production.
- Balancing Affordability with Sustainability
For consumer goods, it’s hard to strike the balance between affordability and sustainability. Even if eco-friendly nylon is more expensive to manufacture, it tends to sell for a high price, making it less available to the budget-minded consumer. For this, manufacturers will need to develop ways to increase capacity and decrease prices so that sustainable products can stand up against the classic cheaper alternatives.
- Scalability of New Technologies
: The second huge obstacle is the scale-up of bio and chemical recycling technologies. Though promising research and pilot trials have been launched, the technologies remain restricted in mass production.
- Infrastructure Limitations
The recycling infrastructure for nylon in large quantities remains undeveloped. Current recycling facilities are unable to produce the volume of nylon waste that mass production would demand. It will require construction of new recycling plants and investments in waste technology to combat this.
- Technical Difficulties in Chemical Recycling
Chemical recycling, the reduction of nylon waste into monomers for reuse, is still in its infancy. The work is complicated and it takes a lot of energy, which can negate the environmental benefits if not carefully monitored. It will take more technological progress to make chemical recycling more efficient and scalable.
- Consumer Awareness and Demand
It’s vital to teach consumers why it makes sense to use recycled nylon to encourage demand for sustainable goods. Most consumers have no understanding of the ecological implications of nylon and other synthetic materials, and there are also misperceptions about their sustainability that could impede progress.
- Overcoming Misconceptions About Synthetic Materials
Some consumers might view synthetics such as nylon as intrinsically unsustainable because they’re derived from fossil fuels. It’s essential that we can overcome these misunderstandings in order to develop a market for sustainable nylon. Brands and manufacturers will need to communicate in clear ways and share a simple understanding of how environmentally friendly nylon alternatives benefit the environment.
- Raising Awareness
Campaigns that inform customers of the ecological advantages of eco-friendly nylon, such as its recyclability and production using renewable materials, can influence consumer attitudes. By sharing success stories and explaining the benefits over time from purchasing sustainable goods, consumers will have the courage to shop responsibly.
VIII. Case Studies and Success Stories
Some firms and organizations have already taken the lead on sustainable nylon production and use. All of these cases illustrate how sustainable nylon can be produced and how it could lead to a better world.
- Aquafil and Econyl
Aquafil is the world’s leading provider of sustainable nylon. By developing the closed-loop recycling of nylon waste into quality fibre, Aquafil’s Econyl project has pioneered a closed loop recycling system for nylon waste. Econyl fibers are produced using recycled textiles, industrial plastics, and fishing nets.
Econyl has made significant contributions towards reducing waste and emissions from traditional nylon manufacturing. Reusing nylon saves millions of tons of material from landfills and the oceans, and creates a healthier supply chain for textile and fashion manufacturers.
- Toray Industries
Toray Industries, a global leader in synthetic fibers production, has been actively moving toward using renewable energy and bio-nylon in their manufacturing processes. Toray’s commitment to their carbon footprint extends to using plant-based materials to make nylon and making their factories more energy efficient.
Toray’s commitment to sustainability has made them the market leader for environmentally friendly nylon, and their bio-based nylon innovations are revolutionizing the industry.
- Brands Leading the Way
Some of the biggest fashion and outdoor brands are adopting environmentally friendly nylon as part of their sustainability practices. Companies like Patagonia, Prada, and The North Face are incorporating recycled and bio-based nylons into their collections, eliminating waste and contributing to the circular economy.
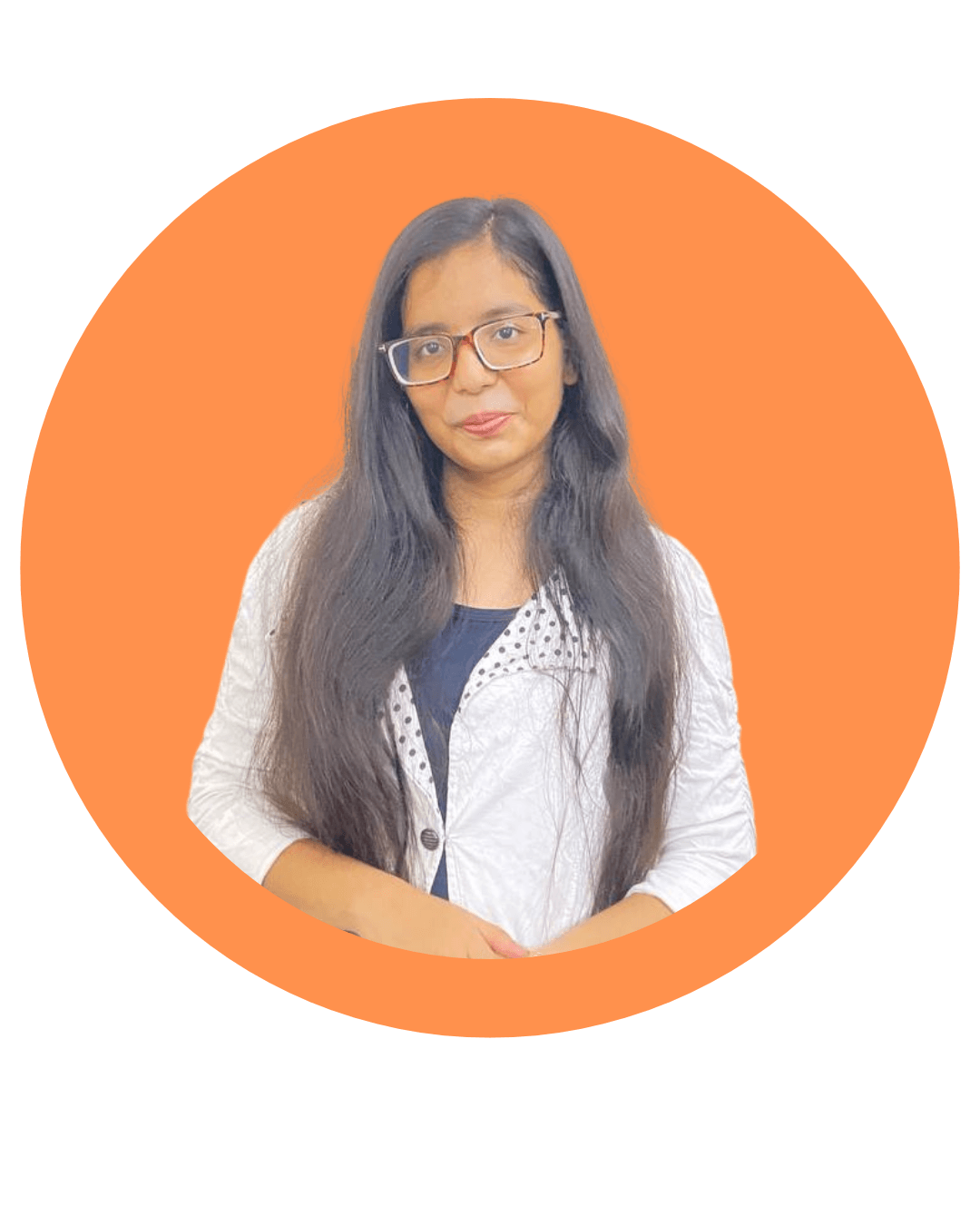
Yashvi Jain, a writer by day and reader by night, is an accomplished content writer and published author of ‘Mind Under Construction. Yashvi possesses extensive knowledge of fabrics, sustainability, and literature. On occasions, you would catch her scripting for her YouTube channel, engrossed in fiction, or ardently dedicating her time to research and storytelling.