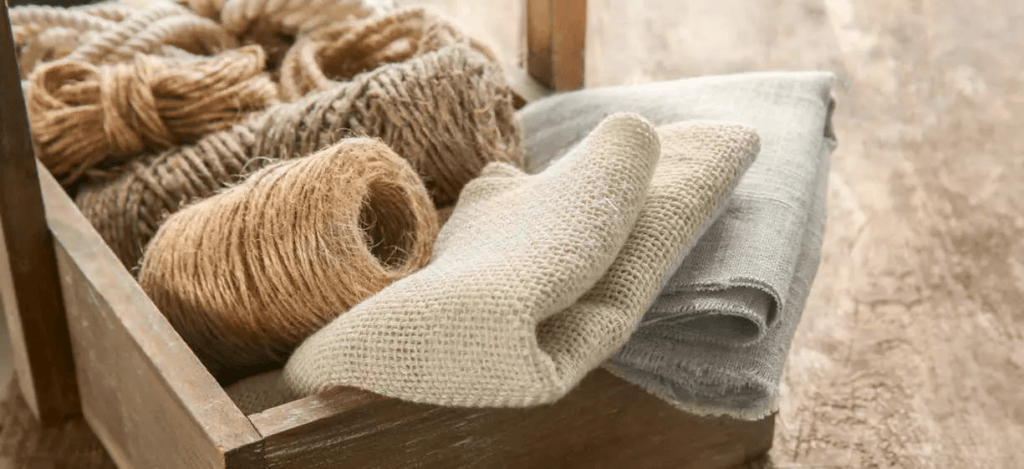
1. Introduction
Hemp fibres have been gaining popularity in recent years, particularly within the sustainable fashion and textile sectors. In an effort to protect the planet, people are turning away from traditional fabrics made of cotton, polyester and synthetics. Hemp, an environmentally friendly, renewable, and biodegradable plant fibre, has a long history of being used for everything from clothing to industry.
Yet what truly makes hemp fibres stand out from other natural fibres is its distinct chemical structure. Our hemp fibers are a material whose strength, resistance, breathable and environmental benefits stem directly from the molecular structure of the plant. Knowing more about the chemistry of hemp fibres helps you better understand their purpose as sustainable products, and why they could transform the textile industry.
In this blog, I’ll tell you more about the chemistry of hemp fibers and what makes them different from other natural fibers such as cotton, linen, and synthetic textiles. Through understanding their structural structure, it is possible to discern the nature of hemp fibers and its uses and benefits in contemporary textiles.
2. The Structure of Hemp Fibers
Biological makeup lies at the heart of what makes hemp fibres so unique. Like every plant fibre, hemp contains several molecules that make up its fibrous material. There are three primary elements that compose most hemp fibres — cellulose, hemicellulose and lignin. Each of these factors determines the mechanical and chemical properties of the fiber.
Basic Structure of Plant Fibers
Plant fibres such as hemp contain long cells made up of cellulose microfibrils. These microfibrils are structured in a manner that makes the fibres stiff and strong. Like other plant fibres, hemp fibres possess a hollow core, called the lumen, which is covered by the cell wall. It is within this cell wall that cellulose, hemicellulose and lignin occur in equal amounts. Cellulose provides the fibre’s physical structure, hemicellulose and lignin provide stretch and support.
- MULTIPLE USE – URBLUX unisex hemp washclothes are ideal for exfoliating face & body & for your daily bathing needs . Gre…
- ECO-FRIENDLY – Hemp is a natural fiber, and therefore it is completely biodegradable! Choosing hemp fabric over a synthe…
- ODOR FREE – Hemp fibers naturally maintain a fresh scent. Your washcloth will remain smelling fresh and clean after ever…
- Jute-Our burlap is made from jute stem fiber,which has good breathability, strength and durability
- Size:Folded jute fabric, fully opened to your desired size.40 inchx12 Feet burlap fabric can be easily cut or folded .Th…
- Function:Use our high-quality burlap rolls to enhance the quality of your gardening. It protects plants from cold and fr…
The physical and chemical properties of a fiber depend on how these constituents are matched up and coupled together in the fibre matrix. When it comes to hemp, its cellulose to hemicellulose and lignin ratio provides it with some of the most attractive attributes for textiles: high tensile strength, low degradation and sustainability.
Also Read : Types of Hemp Fabric and Their Applications
Hemp’s Natural Constituents: Cellulose, Hemicellulose and Lignin.
Hemp fibers are high in cellulose (from 60% to 80% of the fiber’s total weight). Cellulose is a highly complex carbohydrate composed of glucose molecules arranged in chains. It is the most abundant organic polymer on Earth, and the foundational material for plant cell walls. Cellulose, which is abundant in hemp, gives the fiber its crystalline quality that makes it durable, strong and resistant to oxidation.
Although in smaller amounts (about 15% to 20%), hemicellulose contributes to the softness and stretchiness of the fibre. Hemicellulose is a multibranched polysaccharide that wraps around the cellulose fibers. In contrast to cellulose, with its long stiff chains, hemicellulose is more flexible, so the fibre bends and does not break.
Lignin, which accounts for between 2% and 10% of the hemp’s mass, is a natural binder. It gives the fibre a hard, dense structure that provides more strength and protection against bugs, fungus, and moisture. It is lignin that makes hemp fibers unique in their hardness and resistance to degradation. This is one of the reasons why hemp fabric is extremely sturdy and long-lasting.
How Hemp Fibers Are Different From Other Fibers Such As Cotton, Linen, and Synthetic Fibers.
As compared to cotton, linen and synthetic fibres, hemp fibres differ in chemical composition. Cotton, for instance, is almost 100% cellulose (roughly 90%), but does not contain the other two components (hemicellulose and lignin) found in hemp. Hemp fibres therefore remain much tougher and more durable than cotton, which tends to wear out and decay at much greater speeds when subjected to pressure. Although cotton fibres are smooth, they become deformed over time, making them a poor choice for heavy-duty applications.
Linen, another natural fibre from the flax plant, is analogous to hemp in a number of ways. Linen, like hemp, is cellulose-based but has less lignin and therefore is less stiff. Hemp fibers, however, do not stretch, which makes them more durable. Because of this variation in cellulose/lignin content, hemp textiles are better suited to durable, high-performance applications, including clothing, upholstery and industrial fabrics.
Polyester and nylon, synthetic fibres from petrochemical sources, are quite different from hemp, both structurally and environmentally. Hemp fibres are biodegradable, they break down naturally, but synthetic fibres are not biodegradable, and they pollute and waste the environment. Even synthetic fibres are chemically different from plant fibres, in that synthetic polymers, rather than natural components such as cellulose and lignin, are used.
How Lignin Works in Hemp Fibers and Why It Gives Hemp Fibers Their Thickness And Weakness?
Lignin is one of the most important constituents of hemp fibres. Lignin is typically considered a “product” of fiber production, but in hemp it contributes significantly to its strength and resilience. Lignin is a polymer present in the cell walls of plant fibers that glues the cellulose fibres together. This natural binder makes hemp fibers stiff and impervious to tear.
Since hemp fibres are high in lignin, they tend to hold more tension than other natural fibers. It is this that makes hemp the perfect material for applications in which durability is paramount, including rope, canvas and outdoor apparel. Moreover, lignin ensures that hemp fibers don’t absorb moisture, mold, or mildew, which is a useful feature in a wet climate.
The inclusion of lignin offers other benefits, including UV resistance. Lignin naturally filters out UV rays, thereby warding off the sun. This means that hemp fabrics are more resistant to UV damage than other fibres such as cotton or linen. This makes hemp the perfect material for outdoor garments, sun-protective fabrics and other items requiring UV protection.
3. Cellulose: The Secret Behind Hemp’s Power and Stability.
Cellulose is the most abundant organic polymer on Earth and is responsible for the structural integrity of plant fibres. Hemp, with its high cellulose content, is among the most powerful and durable natural fibres available. Here, we’ll explore what cellulose is used in hemp fibres, what hemp fibers have for strength and durability, and why hemp is the ideal fabric for all types of textiles.
How to Describe Cellulose and Why it’s Used in Plant Biology?
Cellulose is a linear polysaccharide that consists of glucose molecules attached to one another by beta-1,4-glycosidic bonds. These long strings of glucose molecules make up microfibrils, which are tightly bound together to form a stiff shell that supports and strengthens the plant cell walls. Culturing is what keeps plants shapeable, structurally rigid, and upright.
The molecular makeup of cellulose is extremely crystalline, which means that the glucose molecules are tightly packed in a structured fashion. It is this crystalline structure that gives cellulose its incredibly high tensile strength and its resistance to stretching and deformation. This special construction makes hemp fibres incredibly resilient and resistant to breaking under strain.
Its Higher Cellulose Yield Than Other Natural Fibers.
Hemp contains the highest cellulose content of any natural fibre, and anywhere from 60-80 per cent of its volume is comprised of cellulose. This is far greater than the cellulose content of cotton (which is usually 90 per cent cellulose, and not nearly as strong or durable as hemp).
Because hemp has more cellulose, it absorbs moisture more easily, withstands wear longer, and is structurally sound for multiple uses. It is for this reason that hemp is used for products requiring strength, like ropes, canvas, and industrial fabrics.
The chemical composition of hemp’s cellulose also contributes to its sustainable nature. Since cellulose is a naturally biodegradable polymer, hemp cloth breaks down in the soil and then decays over time, unlike synthetic fabrics like polyester, which are produced from petrochemical materials and can take centuries to break down in the environment.
Why Cellulose Makes Hemp More Resistant to Wear and Tear?
The high cellulose content of hemp fibres is directly responsible for their strength and toughness. Cellulose is an extremely strong and durable polymer, and the more cellulose there is in a fiber, the stronger it will be. In hemp, cellulose molecules are tightly clustered together, so that the fibre will not stretch and unravel when subjected to pressure.
Hemp’s cellulose fiber also provides a built-in protection against environmental stresses like UV radiation, mildew and bacteria. Because hemp fibers are brittle and strong, they are durable enough to withstand wear and tear over time. That’s why hemp is also commonly used in the industry for ropes, sails, tents and canvas.
Hemp’s Cellulose Composition Compares With Cotton and Other Fibers.
In contrast to cotton, hemp has a more robust, crystallised cellulose composition. Cotton fibres, though filled with cellulose, don’t have the tight-packed, crystalline character of hemp fibres. This makes cotton more flexible and pliable, but also more susceptible to breakdown when stressed. Hemp fibres, meanwhile, remain intact for a longer time and have more tensile strength.
Linen, from flax, is high in cellulose as well, but its fibres are not as malleable as hemp’s due to the lesser proportion of hemicellulose and lignin. It means that hemp yarn is even more robust and resistant to environmental wear and tear than linen.
Due to the durability of hemp fibers, they are ideal for all kinds of uses requiring durability and endurance. Because of their high cellulose content, hemp fabrics can withstand heavy wear and conditions of moisture, UV radiation, and wear and tear, and are the best sustainable textile choice.
4. Hemicellulose & Lignin: What Are Their Impacts on Hemp Fiber?
While most fibres in hemp are composed of cellulose, they contain other key chemical elements such as hemicellulose and lignin. These two factors contribute to the fabric and mechanical structure of hemp fibres, such as its elasticity, stiffness, degradability and overall performance in textiles and manufacturing. Understanding how hemicellulose and lignin affect the qualities of hemp fibre helps us to see why hemp is a superior material for sustainable textiles.
How Hemicellulose Shapes Fibers, and Whether or Not it Affects Stability?
Hemicellulose is a polysaccharide present in the cell walls of plants, acting as a scaffold for cellulose fibres. Instead of long, straight lines of glucose molecules, cellulose consists of short, branched, malleable chains of hemicellulose. This structural difference is what makes hemicellulose important for giving plant fibres some elasticity. In hemp, hemicellulose makes up the bulk of the fibre structure, but is smaller than cellulose.
This elasticity in hemicellulose is part of what allows hemp fibres to be both structurally sound and adaptable to multiple applications. This elasticity is ideal for fabrics where the material must bend and stretch without tearing. Hemp fibers that contain a higher amount of hemicellulose are easier to handle and can be spun into comfortable clothes. But the inherent stiffness and strength of hemp fibres (along with the high cellulose and lignin content) still ensures that the fabric remains durable and wear resistant.
Perhaps this is one reason why hemp cloth is considered a multi-purpose textile: it provides both rigidity and flexibility. The resulting strength from cellulose and elasticity from hemicellulose makes hemp fibers ideal for a wide variety of uses, from soft fabrics to strong industrial fabrics. It is this distinctive combination of cellulose and hemicellulose that makes hemp ideal for a variety of landscapes and applications.
It’s The Effect of Lignin On the Hemp Fiber’s Rigidity and Resistance to Breakage.
Lignin is a polyphenolic substance that exists in the cell walls of plants. It works as a binder, pulling together cellulose fibres and adding structural bulk. Although all fibers in plants contain lignin, hemp is more lignin rich than other natural fibres such as cotton and linen, and therefore offers many properties that are distinct from other fibres.
In hemp fibres, the primary function of lignin is to make them stiffer and more resistant to breakage. The hardness that lignin imparts to hemp fibers is part of what makes hemp cloth durable and long-lasting. As opposed to cotton or linen, which lose their structure and soften over time, hemp fibers do not become brittle and fragile when soaked in frequent use, or exposed to the effects of ultraviolet radiation and moisture.
Lignin also keeps hemp protected from insects, fungi and bacteria. As a natural antimicrobial, lignin inhibits the growth of microbes that could rot the fibre or produce bad smells. It’s why hemp fibers are ideal for use in damp or humid environments, where other natural fibers, such as cotton or linen, might become more prone to mold and mildew.
Additionally, lignin also helps to protect hemp fibers from the effects of UV radiation. Lignin scavenges the ultraviolet radiation, thus halting the degradation of the fibre’s matrix under sunlight. This makes hemp a superior material for outdoor uses that require UV resistance, such as in sun protective apparel, tents, and sporting equipment.
Why Hemp’s High Lignin Level Helps Make It More Stable and Protected from Bugs, Fungi, and Bacteria.
Hemp’s relatively high lignin content accounts for some of its extreme durability and resistance to environmental stressors. Due to the intrinsic durability of lignin, hemp fibres are not likely to degrade over time, which is why they are ideal for high-quality, long-lasting products. Hemp textiles are therefore a sustainable material, because they are less vulnerable to premature deformation and warping than other natural fibres such as cotton.
Furthermore, lignin provides hemp with natural resistance to pests and fungi. The fermentation of cellulose is the process by which many pests such as insects and fungi decompose plants. Because lignin is more resistant to microbial rot, hemp fibres are less susceptible to pests and fungi. This resistance makes hemp fibres particularly useful in settings where mould, mildew and insects are an issue, including for outdoor textiles, marine fabrics, even medical fabrics.
Another advantage of lignin is that it will also shield hemp from bacterial contamination. Lignin’s antimicrobial action prevents bacteria and other microorganisms from forming in the fabric that might make it smell or turn yellow. This makes hemp a popular choice for textiles like clothing, bed linen and other fabrics where cleanliness and quality are critical.
Hemicellulose and Lignin of Hemp for Industrial and Textile Industries
Hemp is rich in hemicellulose and lignin, providing numerous advantages that make it an attractive material for both industrial and textile use. For industrial applications, the tough, brittle qualities of hemp fibres, derived from lignin, make them ideal for ropes, sails and canvas. The herb’s anti-pest and fungicide resistance makes hemp an excellent candidate for marine uses, where moisture and climate are not uncommon.
When used for textiles, hemp’s elasticity combined with the rigidity of lignin make hemp fabrics very comfortable, strong and resilient. Hemp fabrics are naturally breathable, moisture wicking and UV resistant, making them ideal for clothes and outdoors. In addition, the antimicrobial properties of lignin improve the fabric’s resistance to smell and microbial activity, making hemp a sanitary and sustainable fabric for all kinds of clothing including activewear, shirts, pants and jackets.
Hemp fibres are also increasingly being used for sustainable materials, including biodegradable packaging, composites, and insulation. The combination of hemicellulose’s elasticity and lignin’s resilience makes hemp a fantastic alternative to synthetics for both strength and sustainability.
5. Hemp Fiber Extraction Chemical Methods The Chemical Methods of Hemp Fiber Extraction.
The process of processing hemp fibres is done through a combination of chemical and mechanical methods. The hemp fibers are contained in the stalks of the hemp plant, and extracting those fibres requires disintegrating the plant’s non-fiber material to reveal the valuable fibers. This is called retting, and has been used for centuries to obtain fibres from flax, hemp and jute.
Description of How Hemp Fibers Are Extracted from the Plant (Retting, Decortication)
The processing of hemp fibers starts with retting, which uses moisture, bacteria or enzymes to breakdown the pectin and lignin that holds the fibres together. There are three forms of retting: water retting, dew retting and chemical retting. The most common hemp fiber extraction technique is water retting, which places hemp stalks in water for several days so natural bacteria can breakdown the non-fiber parts.
When retting is complete, the hemp stalks are dried and mechanically processed by decortication. Decortication is a method of cutting away the fiber from the hard core of the hemp stalk. This is often accomplished with mechanical machines that decapitate the stalks and chip away the outside bark and non-fiber components. The result is a clump of long, tough hemp fibres that can then be converted into yarn, fabric or other materials.
How Retting Uses Natural Enzymes, and How This Distills Plant’s Non-Fiber Components.
The pectin that holds the cellulose fibres together is destroyed by microbes, such as bacteria and fungi, during natural retting. The enzymes of these microbes break down the plant’s non-fiber components, including lignin and hemicellulose, which do not form the fiber. It eventually softens the fibres from the stalk, enabling it to be snipped apart and used for textiles.
Newer retting technologies, instead, used natural enzymes to speed up and optimise the process. Enzyme retting is more eco-friendly than chemical retting, which can be environmentally damaging using toxic chemicals. Enzymes not only speed up the retting process but also maintain the quality of the hemp fibers, making them strong and robust.
How Pure Hemp Fiber Is Chemically Extracted From the Stalk, and How Technological Advancements Have Sped Up the Process.
Pure hemp fibre is difficult to harvest because of the chemical chemistry of cellulose, hemicellulose and lignin. The fibres are bound tightly together by these elements, and dismemberment must be carefully controlled so that the fibers are not destroyed. Modern techniques, including enzymatic digestion and mechanical decortication, had improved extraction efficiency and made it more sustainable.
The main problem with extracting fiber is that the plant’s woody core is so densely laden with lignin that it can be difficult to separate out the cellulose fibres. But better processing has made it possible to selectively remove lignin, creating high-quality hemp fibres with very little waste. With these advances in fiber extraction technology, new uses for hemp have emerged, from clothing to biocomposites.
6. Absorption and Wetness-Repelling Characteristics of Hemp Fiber.
The chemical structure of hemp (especially its high cellulose content) contributes to its water-wicking properties. In this section, we’ll see how the moisture control of hemp fibres makes it both comfortable and useful in a variety of applications, especially textiles and clothing.
How Hemp’s Chemical Composition Impacts Its Water Absorption Properties.
Hemp fibers have a high surface area, which helps it retain moisture more effectively than most other natural fibers. Hemp molecules are hydrophilic (water-seeking), which means they can take up water from the air. This moisture-holding capacity makes hemp fibers an excellent choice for textiles, because they retain water from the skin during moist conditions.
In addition, the cellulose structure of hemp fibres helps it control moisture. Long strings of glucose molecules in cellulose create a network by which water molecules can be picked up and pushed across the fibre. This makes hemp fabrics particularly effective in absorbing sweat and moisture, especially in workout apparel and garments worn in hot, moist environments.
Wetness Retention of Hemp Fibers Compared with Cotton and Other Fabrics
As well as being moisture-absorbing, hemp fibres are moisture-wicking, which means that they draw moisture away from the skin and evaporate it. It’s a crucial element in activewear and other clothes that demand comfort. Hemp is far more moisture-wicking than cotton because cotton fibers are bulky and soaked in water, making them uncomfortably warm to wear in humid weather. Hemp, on the other hand, remains a lightweight and breathable garment even when it soaks up water, keeping the wearer dry and comfortable.
- Cellulose: How Hemp Controls Moisture and What It Does To Make Clothes Comfortable.
Cellulose is a key component of hemp’s ability to draw moisture away from the body. Because of its chemical composition, hemp fibres do not swell or stiffen as they soak up water. This prevents the fabric from becoming too damp or achy, which causes it to be uncomfortable and uncomfortable. The moisture wicking qualities of hemp fibers also make it breathable so clothes can better flow and regulate the temperature.
In general, hemp fibres’ chemical composition — particularly their cellulose content — is perfect for regulating moisture and facilitating comfort in fabrics. Dresses, bedding or backpacking clothes: hemp’s moisture-wicking properties regulate body temperature and keep the wearer dry, making it increasingly popular for sustainable fashion.
7. Hemp’s UV Resistance: A Chemical Perspective Hemp’s UV Resistance: A Chemical Perspective
Hemp fibres are incredibly durable and tough, but one of their most unique natural properties is their resistance to ultraviolet (UV) radiation. Hemp naturally possesses UV-blocking abilities, making it an ideal material for outdoor clothing and equipment that allows both ease of use and shade from the sun’s harmful rays. It is crucial to understand the chemical processes that underlie this UV resistance if we are to truly understand hemp as a sustainable material.
The Natural UV-Shielding Effects of Hemp
Keeping fabrics UV-resistant is a key attribute for clothes used in the outdoors, athletic apparel and other clothing that is required in sun-lit settings. The sun’s UV rays are damaging to our skin – it can cause sunburn, premature aging, and skin cancer. Hemp fibers naturally resist the effects of UV rays, a crucial factor in shielding the skin from these ill effects. In contrast to synthetic fabrics that often are treated with chemical UV-blockers, hemp is an eco-friendly alternative because of its natural UV resistance.
Hemp fibres withstand UV radiation precisely because of their chemical composition. One of the reasons why hemp is UV resistant comes from the abundance of lignin in its fibres. Lignin is a dense polymer, which plants naturally secrete from their cell walls. It serves as a shield against UV radiation to stop the sun’s light from entering the fibre and into your skin. This inherent UV-blocking quality of hemp is due to lignin’s capability to bind and reflect UV radiation away from the body without harming it.
Beyond lignin, hemp fibers are rich in phenolic acids and flavonoids, which also have UV protection. These are antioxidants and UV-blockers that further guard the substance from damage due to the sun. These natural ingredients all add up to a fabric that is resilient and invulnerable to the damaging effects of the sun.
How the Lignin and Other Chemicals in Hemp Fibers Provide Natural UV Protection?
Lignin is a polymer composed of phenolic groups which allow it to absorb UV light. When UV light hits hemp fibres, the lignin filters the light away and keeps it from entering the fibre. This keeps the fabric intact and doesn’t rot when exposed to the sunlight. In this way, hemp fabrics resist sun-induced fade, degradation and weakness, which makes them suitable for outdoor applications such as sun-protection clothing, tents and outdoor gear.
Besides lignin, there are other naturally occurring elements in hemp fibres that enhance their UV stability. Secondary metabolites of many plants are flavonoids, which act as antioxidants and absorb ultraviolet light. These elements are able to resist UV oxidation, prolonging the durability and durability of hemp fibers. Another group of compounds in hemp, phenolic acids, also absorb UV rays, thus further strengthening the fabric’s sun protection.
The hemp fibre’s combination of lignin, flavonoids and phenolic acids makes it naturally UV-resistant, without the use of chemical treatments or additives. That makes hemp a healthier alternative to synthetic fabrics, which typically require chemical UV-blockers that are potentially harmful to the environment or to humans.
How Hemp’s UV Stability Can Affect Outdoor and Sportswear.
Because hemp naturally blocks UV rays, it’s a great fabric for outdoor wear and protection clothing. Hemp also protects more effectively from harmful UV rays for items that will be exposed to the sun, including hats, shirts and jackets. Even clothes that are fabricated from hemp fabric may offer better UV protection than clothing constructed from cotton or other natural fibres that don’t have the same UV protection.
The biggest advantage of hemp’s UV stability is that it doesn’t deteriorate. Where most synthetics are not UV-resistant after repeated washing or exposure to the sun, hemp will keep it that way for as long as the garment is worn. This makes hemp a sustainable, high-performance fabric for outdoor clothing, as it provides long-term UV protection without the need for additional chemical or paint applications.
Furthermore, hemp’s UV protection not only benefits apparel, but also outdoor apparel and accessories. Hemp is being used in the making of tents, backpacks, umbrellas and other outdoor gear because it contains UV protection. The more consumers become conscious about sun protection and environmentally friendly materials, the greater the demand for hemp-derived outdoor goods.
Not only does hemp naturally resist UV rays, it’s also durable and strong, making it a durable choice for outdoor usage. Hemp fibers are highly resistant to wear, tear and weathering, and hence, suitable for outdoor applications. This tensile strength coupled with UV resistance make hemp an excellent material for practical and environmentally responsible hiking clothes and accessories.
8. The Biodegradability of Hemp Fibers
One of the major environmental benefits of hemp fibres is that they are biodegradable. In contrast to synthetic fibres, which can decay over centuries, hemp fibres are naturally biodegradable and can decompose in a matter of days under normal conditions. This property plays a vital role in decreasing the ecological footprint of textiles and tackling the emerging issue of textile waste.
Description Of The Chemical Bond That Makes Hemp Fibers Decompose Naturally Explanation of How Hemp Fibers Break Down In Nature.
Biodegradability of hemp fibres is closely related to their chemical composition (particularly cellulose, hemicellulose, and lignin). Cellulose is a natural polysaccharide, readily digested by soil microbes. Because hemp is a vegetal fibre, it’s very cellulose-rich, making it easily damaged by microbes. After a cloth containing hemp fibres is moist, heated and infected with bacteria and fungi, the cellulose dissolves into simple sugars that bacteria and fungi consume, eventually decomposing the fibre naturally.
Due to its high cellulose content, hemp is biodegradable and environmentally friendly as it simply decomposes with minimal toxic contamination. This is much faster than the decomposition of synthetic fibres such as polyester, which can survive in the environment for hundreds of years. The natural decomposition of hemp fibres is part of the circular economy, since the material can be returned to the soil without damaging the ecosystem.
But hemp fibres do contain lignin, which is more inert than cellulose. Though lignin helps to maintain hemp’s toughness and resilience, it also has a limiting effect on its biodegradability. However, hemp fibres remain well-biodegradable compared to synthetics, which do not decay in nature and may cause lasting harm in landfills.
Comparing Hemp’s Biodegradability with Synthetic Textiles and Other Natural Fibers.
Hemp fibres are far more biodegradable than synthetic fabrics such as polyester, nylon or acrylic. Synthetic fabrics are chemically constructed using petrochemicals and are made from non-biodegradable ingredients. It can take hundreds of years for these fabrics to decompose in landfills, and as they do so, they release microplastics into the atmosphere that pollute and disrupt ecosystems. Hemp fibres, however, are plant-based and cellulose-based, and they fall apart much more rapidly, making them more environmentally friendly.
Hemp is more biodegradable than other natural fibres such as cotton and linen (though cotton can decompose more rapidly than hemp due to the absence of lignin). Yet hemp still surpasses cotton in sustainability as hemp needs less pesticides and less water to grow. Besides, hemp is more resistant to pests and diseases, which reduces chemical application in the field, further enhancing the overall environmental advantages of hemp.
Hemp’s biodegradability makes it an ideal candidate for sustainable clothes and green fabrics. In an era when the fashion industry is striving to be greener, hemp presents a viable alternative to artificial materials for consumers who want a biodegradable, environmentally sound product that can be recycled.
The Environmental Advantages of Hemp Fibers in Textiles and Fashion Industry Waste Reduction
The environmental benefits of hemp fibres extend far beyond their biodegradability. Hemp is also a very water-efficient, low-use crop, and requires less pesticides and fertilisers to grow than cotton, which consumes a great deal of water and requires more chemicals to produce. By transitioning to hemp fabrics, the fashion industry will be able to shift from water-intensive agriculture and reduce its toxicity through harmful pesticides and fertilisers.
Hemp fibres are also processed without the need for any chemicals, thus further reducing their environmental footprint. Compared with synthetic fibres, which are highly energy-intensive and chemically based, hemp fibres are carbon-neutral and pollutant-free. That makes hemp an integral part of the movement towards sustainable fashion and textile recycling.
His biodegradability also addresses the burgeoning problem of textile waste. Since fast fashion wastes huge quantities of clothing every year, the natural breakdown of hemp fibres provides an alternative to the overflowing landfill. As consumers demand more environmentally friendly options, hemp textiles can be used as a way to reduce the environmental impact of the fashion industry and shift towards a circular, sustainable economy.
9. Hemp Fiber Processing: Combining with Other Fibers
Although hemp fibres are by nature durable, strong and biodegradable, they can be manipulated to make them softer and more comfortable. Mixing hemp with other fibres means that manufacturers can make fabrics that combine the best of both. Through blending, the chemical and physical properties of the fabric can be modified, creating multiple textiles for various uses.
What Chemical Alterations We Can Add to Hemp Fibers To Make Them Softer and Comfier?
Hemp fibres are notorious for their roughness, especially when they are raw. Chemicals and mechanical manipulations can be applied to hemp fabrics to improve the softness and warmth of the fabric. These can include enzymes, scouring and bleaching, which break down the lignin and hemicellulose in the fibres and soften the material. Enzyme treatments in particular are gaining in popularity because they’re environmentally friendly and enhance the sheen of hemp fibers without the use of harsh chemicals.
Hemp fibres can also be mechanically carded, combed and spun to further straighten and polish the fibers. These techniques straighten the fibres and reduce their roughness, resulting in a silkier, more breathable fabric. With these changes, hemp can be converted into fabrics that are akin to cotton or linen yet retain their inherent strength and resilience.
How to Mix Hemp With Other Fabrics, Such As Cotton, Silk, and Synthetic Fiber.
Combining hemp with other natural or artificial fibres is another way to alter its properties. By weaving hemp and cotton, silk or synthetics like polyester, textile manufacturers can achieve fabrics that are as soft, durable and versatile as possible. They blend hemp fibers and selected fibers together, spinning them together to produce a single fabric with desired characteristics.
Mixing hemp with cotton, for instance, results in a fabric that combines hemp’s durability and UV protection with cotton’s softness and breathable properties. This blend is great for casual wear because it gives you the best of both worlds. Hemp and silk blends, however, produce luxurious fabrics that are silky-smooth without compromising hemp’s strength. Such combinations appear prominently in fine clothing and jewellery.
Other synthetic fibres, like polyester, can also be added to hemp to make textiles that are lightweight, wicking, and resistant. Such blends are also used in activewear and outdoor wear, where comfort and performance are required. The chemical composition of the synthetic fibers complements the natural qualities of hemp, which means they make both wearable and sustainable fabrics.
How Such Blends Influence the Chemical and Physical Properties of the Resultant Fabric As A Whole.
Combining hemp with other fibres changes the chemical and physical characteristics of the fabric as a whole. For instance, mixing hemp with cotton can soften and soften the fabric while still retaining hemp’s moisture-wicking and UV-resistant properties. This layer of cotton softens the coarse feel of hemp to create a material that is comfortable and resilient.
Likewise, mixing hemp with silk produces a more comfortable and soft fabric that is not at all devoid of hemp’s strength and durability. Silk is added, making it smoother and softer to make it suitable for fashionable and high-end uses.
When synthetic fibres are concerned, mixing with hemp may enhance the fabric’s performance characteristics, including moisture resistance, elasticity and wrinkle resistance. Synthetic fibers such as polyester help lower the production cost and enhance the adaptability of hemp fabrics to a wide variety of uses.
Such changes enable hemp to compete with a wider variety of fibres and provide more versatility for textile manufacturing. Combining hemp with other fibers enables manufacturers to produce fabrics that can satisfy the demands of many industries while keeping hemp’s environmental qualities intact.
10. Challenges in Hemp Fiber Chemistry
Hemp fibers have attracted much attention in recent years because of their sustainability and distinctive nature, but processing these fibres has several difficulties. Although hemp fibres offer numerous benefits, including biodegradability, durability and UV stability, there are inherent properties that make them difficult to process and incorporate into the textile industry. In order to understand these issues, we need to explore more closely the chemical and physical characteristics of hemp fibres and their impact on usability.
The Challenges of Using Hemp Fibers: Texture and Hardness
One of the most recognizable issues with hemp fibers is their rough, stiff texture. Hemp fibres are coarse and stiff, in contrast to cotton, which is a soft, smooth fibre that easily tangles and spins. They do so because they are heavily coloured with lignin and cellulose, which lend strength and resistance to the fiber while making it rough. Lignin, specifically, is the “glue” that bonds the cellulose fibers in plant cell walls, giving hemp its toughness and abrasion resistance.
Hemp’s roughness can be problematic for its processing, especially in the first phases of textile manufacturing. When hemp is harvested, it must be removed from the plant’s wooden stalks. The process of decortication is often slow, requiring heavy machinery to cut the fibre apart from the rest of the plant matter. Further, hemp fibers are shorter and more fibrous than cotton fibres, so they are not well-suited to conventional spinning.
It is also difficult for hemp fibres, due to their hardness, to be used comfortably and easily in textiles. Raw hemp textiles tend to be rough and stiff on the skin, so they are not ideal for use in apparel and bedding. The material, although hemp is durable and tough, is not naturally soft, making it less widely adopted for everyday wear compared to soft fibres such as cotton or wool.
How the Chemical Structure of Hemp Fibers Influences its Processing and Use in Textiles?
Hemp fibers are highly influenced by the chemical structure that determines their processing and application in textiles. Hemp consists primarily of cellulose, hemicellulose and lignin; cellulose provides the highest strength and durability. While cellulose gives the fibre its elasticity, its richness in lignin means it is resistant to decay through natural decomposition. This lignin content provides for increased durability, but it also makes the fibre more brittle and difficult to soften and work with.
Hemp is rich in cellulose, giving it many of its desirable properties – strength and moisture wicking properties. But it is also cellulose that renders hemp fibres difficult to digest. The crystallisation of cellulose prevents it from breaking down and being spun into yarn. Unlike cotton, which has more pliable cellulose, hemp demands more energy-intensive treatments to get ready for textile use. The addition of hemicellulose (a group of polysaccharides) complicates further processing of fibers. Because hemicellulose is a binder, it makes it difficult to disentangle the cellulose fibers from each other when it’s being processed.
Restructuring hemp fibers into usable fabric means breaking up these elements and making the fibers soft. Traditionally, this was done through extreme chemical treatments, often damaging to the environment. Such treatments also harm the fibres and reduce their durability and strength. As hemp fibers are high in lignin, they also need extensive retting which takes time and can leave fibers exposed if not done correctly.
Additionally, hemp fibres are of a different length and diameter than cotton or wool, which makes weaving and spinning difficult. Hemp fibres should lie together symmetrically so that the result is a durable fabric. When the fibres aren’t placed in the right alignment, the fabric will be frayed.
Progress and Innovation on Hemp Fiber Treatment and Processing.
As a response to these difficulties, research and innovation in the hemp fiber processing sector seek to identify more effective and sustainable ways to soften and prepare hemp fibers for textile applications. Technological improvements in enzymatic processing, mechanical processes and chemical modification are transforming hemp fibres into more usable materials without jeopardising their sustainability.
One of the most promising advances in hemp fibre processing is the enzyme process to decompose the lignin and hemicellulose present in the fibers. Enzyme treatments are more environmentally friendly than conventional chemical methods and have been shown to increase the softness of hemp fibers without reducing their strength and resistance. These enzyme treatments remove the complex carbohydrates and lignin that stiffen the fiber to produce smoother, more malleable hemp fabrics.
Apart from enzymatic treatments, new mechanical techniques are being developed to smooth out hemp fibres and reduce their roughness. Modern spinning techniques, including air-jet and ring spinning, result in finer hemp yarns better suited to textile applications. These techniques soften the fibers, making them easier to work into clothing.
Scientists are also studying how hemp could be blended with other fibres like cotton, silk, and artificial fibers to give hemp textiles a more supple and functional texture. Combining hemp with other fibers, textile designers can make fabrics that are as strong and sustainable as hemp and as soft and supple as other fabrics. This blend-in could open up more opportunities for hemp to make its way into fashion and textile production, and become an increasingly desirable choice for casual wear.
11. The Future of Hemp Fiber Chemistry?
Hemp fibres hold promise, particularly as consumer interest in sustainable and environmentally friendly textiles continues to rise. Chemical processing, fibre manipulation and blending are increasingly making hemp a practical and adaptable fabric for use in everything from apparel and upholstery to machinery. When the fashion industry searches for alternatives to artificial fibres, hemp might be able to take over most of those current sources due to its sustainability, durability and increasing ease of manufacture.
New Chemical Processing Methods for Hemp Fibers to Make Them More Soft, Flexible, and Usable.
As demand for hemp products across the globe continues to rise, the need for faster and better methods of processing hemp fibres becomes increasingly urgent. They’re constantly coming up with new ways to improve hemp fibers — their feel, stretch, and versatility.
One of the main areas of innovation in the hemp fiber processing industry is the introduction of more effective softening processes for the fibers. ‘Most old-school hemp fabrics feel tough and coarse, but new chemical treatments and enzymes are breaking down the lignin and hemicellulose that comprise hemp fibers, making them soft and comfortable. Using natural enzymes or less toxic chemicals, manufacturers can enhance the feel of hemp fabric without compromising their environmental benefits.
A second new area of innovation is the creation of hemp fiber blends. Combining hemp with other natural fibres such as cotton, silk or wool will increase the softness and versatility of the fabric, making it fit for a broader array of uses. For instance, hemp-cotton blends are becoming increasingly popular in fashion because they bring together the durability and strength of hemp with the softness and breathable qualities of cotton. In a similar vein, hemp-silk blends are now being used to manufacture luxury fabrics that provide both comfort and durability without resorting synthetics.
The mechanical treatment, through spinning and weaving, is also improving the usability of hemp fibres. New spinning techniques produce smaller, more even hemp fibres that can be woven into comfortable fabrics. Development of sustainable dyeing and finishing techniques is also promoting hemp-based fabrics’ popularity by making them more adaptable to different end applications.
How Hemp Fibers Can Supersede Synthetic Fabrics and Save the Environment?
Perhaps the most important use for hemp fibres is as a substitute for synthetic textiles that are a menace to the environment and pollute the atmosphere. Because hemp is a natural, biodegradable product that can be grown with little environmental impact, it is a perfect alternative to synthetic fibres produced from petroleum products.
The textile industry is one of the leading polluters and waste collectors, particularly in the manufacture and disposal of synthetic fabrics such as polyester, nylon and acrylic. These materials aren’t biodegradable and can take hundreds of years to decompose in landfills, leaving noxious microplastics in the air. Hemp, however, decomposes organically, keeping textile waste out of landfills and encouraging a more circular economy.
Not only is hemp biodegradable, it uses less energy to produce than crops such as cotton. Hemp also naturally repels pests, meaning there is no need for chemical pesticides or fertilisers. It also takes less water to germinate, which makes it more sustainable in a water-poor environment. As people become more mindful of the impact of their clothing purchases, hemp can supplant synthetic fabrics in every product category from apparel to manufacturing.
Trends in Hemp-Based Textiles and Their Chemical Advancements in Fashion and Industry.
In the wake of a growing need for more sustainable and eco-friendly materials, hemp has gained acceptance in fashion and industry. Hemp is increasingly being worn in fashion because consumers want alternatives to fast fashion and synthetics. Designers are mixing hemp into their clothes to create not only fashionable, but sustainable clothing. From everyday wear to high-end accessories, hemp is becoming a fashion fabric, and hemp-cotton and hemp-silk are increasingly being used.
In industry, hemp fibers are employed to make ropes, composites, and bio-based car materials. Demand for natural products has also inspired a new era of hemp-derived industrial products, as manufacturers continue to look for ways to optimize the performance and utility of hemp fibers in the field. New processing technologies are unlocking the potential of hemp as a more economically viable and adaptable material for diverse applications.
The future of hemp fibers looks bright, and more research and innovation promises to bring hemp into textiles and beyond. With the right technology, hemp will become a ubiquitous material, providing environmental and industrial benefits in many industries. Despite its chemical identity and increasing versatility, hemp could revolutionise the textiles sector and make our world a greener place.
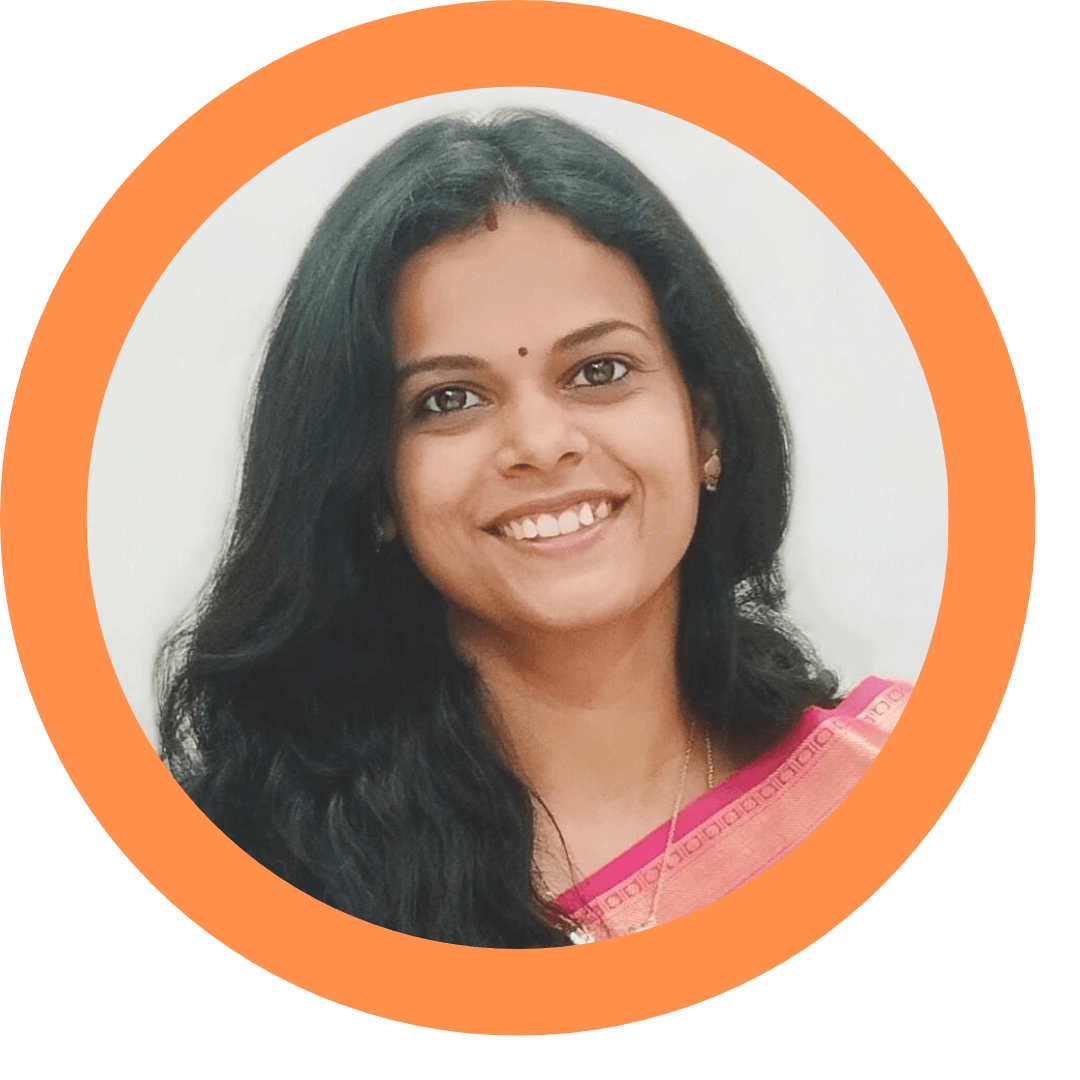
Dhanya Nair is a fabric Lover and a mom. She offers a unique perspective on the intricacies and history of fabric and specializes in bringing the unique narratives of textiles to life.