I. Introduction
Imagine the soft touch of linen clothing, the sturdy feel of a linen tablecloth, or the soothing texture of a linen bed sheet. Chances are you have linen items in your home and probably love them. Linen is one of the oldest and most beloved fabrics known to mankind, a truly timeless textile. It’s long-lasting, highly absorbent, cool, and incredibly strong. Linen is the quintessential natural material, exuding understated elegance and sophistication in every fiber.
In addition to all that, linen is also surprisingly complex. While the final product might seem simple and pure, the process of turning flax into linen is lengthy and fascinating. To make every yard of linen, you need a miracle of human ingenuity, tons of hard manual labor, and a rich history with just the right amount of the original flax plant.
It’s the combination of all these factors that make linen the miracle textile that it is. By learning about linen, we not only get to learn more about the beloved natural fabric and what it can do for us, but we also have an opportunity to appreciate it more. We also can learn a little more about nature and our world. Linen is a fabric like no other, a symbol of craftsmanship, sustainability, and a love for slow production. As we increasingly consume clothes and textiles made from synthetic materials and fibers, it is important to remember and learn about artisanal linens of the past and present.
In this linen origin story, we will take you through every step of the linen making process. From the very beginning, with a simple stalk of flax growing in the field, to the various stages of linen production, right through to the last weaving step. We will examine the process in all its glory, from the traditional methods that have been used since ancient times to the cutting-edge techniques of modern production. By the end of this piece, you will know everything about where linen comes from, how it’s made, and the proper care linen needs.
II. The Flax Plant: Linen’s Natural Source
A. Botanical Overview
To understand how linen is made, we first need to start at the beginning. The beginning of linen, that is, because the beginning of life itself is a much more complex story. But for our purposes, the first thing you need to know is that linen comes from the flax plant. The flax plant, known botanically as Linum usitatissimum, is a humble herbaceous plant. Most flax plants don’t grow very tall, rarely reaching above 3 to 4 feet (1 meter) in height. It has slender green stems and small pale blue flowers. The flowers are stunning to look at, but they only bloom for one day. Then, in the maturity stage, the stalks dry up and turn golden yellow. With stalks like that, it’s not a surprise that they’re actually pretty strong and fibrous.
Flax has been grown and used by humans for at least 6,000 years. It’s used for a variety of purposes with both the seeds and the fibers finding widespread use throughout history. However, it’s the long cellulose fibers found within the flax stalks that will be of interest to us.
The plant typically has the following growth cycle:
an early spring sowing, a maturation period of around 100 days, and a late-summer harvest. The plant thrives in cool, temperate climates with plenty of rain. It prefers well-drained, loamy soils and can grow almost anywhere but may suffer in extreme heat or drought, which can diminish the quality of the fiber.
The long stems of the flax plant are straight, with minimal branching. This is ideal for producing high-quality linen fibers.
Some of the best flax in the world is considered to come from Western Europe.
And in particular:
Belgium. In particular, the Flanders region of Belgium is known for the premium-quality flax it produces. The country’s temperate weather and excellent soil make it ideal for linen.
France. France is one of the world’s largest producers of flax, and it has a long and well-established tradition of flax growing. Normandy and Picardy are two of the most famous French regions for linen.
The Netherlands. The country’s coastal climate, sandy soil, and emphasis on sustainable and organic farming makes The Netherlands an excellent place for growing flax.
Of course, many other countries, including Russia, Ukraine, China, Egypt, and Canada, also grow flax. However, there are differences in the fiber length and quality of flax from different countries depending on climate, cultivation, and production.
B. Sustainability of Flax Cultivation
Flax’s rise in popularity and renewed interest in recent years is for one major reason: it’s just that – sustainable. In an increasingly environmentally-conscious world, we’re becoming more aware of our consumption and the harmful effects of fast fashion and overproduction. Linen, with its low environmental and agricultural impact, is making a comeback.
Minimal Water and Pesticide Requirements
Water. Flax is a highly drought-tolerant crop, which means that it doesn’t need a lot of irrigation, if any. Most of the flax that is grown in Europe is 100% rain-fed. In that respect, linen production is not contributing much to the problem of water scarcity and is a great choice in drought-prone areas.
Pesticides and chemicals. Flax is also naturally resistant to many pests and diseases, so farmers don’t have to rely on chemical pesticides and herbicides. That makes it much better for the environment and, importantly, for the people working in flax production.
Soil-Enriching Properties
Flax is known as a soil-enhancing crop that, over time, can improve the quality of the ground it’s grown on. The flax plant’s deep roots help aerate the ground and even reduce compaction that can prevent water from being absorbed. That is why flax is often used in crop rotation systems with other plants, which all benefit from flax’s soil-boosting properties.
In addition, by-products such as seeds, shives, and tow, can be used to make animal feed, insulation, or compost.
Linen vs. Cotton
One of the most common comparisons, when it comes to fabric sustainability, is flax (and therefore linen) vs. cotton.
In that comparison, flax consistently comes out ahead:
Feature Flax (Linen) Cotton
Water use Low (Rain-fed) High (Requires irrigation)
Pesticide use Minimal High (Conventionally-grown cotton requires significant amounts of chemicals)
Yield per hectare Moderate High but with a greater environmental impact
Biodegradable Yes Yes (if untreated)
Processing chemicals Fewer Needs bleaching, dyeing, etc.
Linen wins out over cotton in water usage, carbon emissions, chemical use, and a number of other environmental factors – especially if the flax was processed using traditional, chemical-free methods.
III. Harvesting the Flax
After the flax has fully matured, it’s time to harvest the crop. The quality of the harvest will have a big impact on the linen-making process later. Harvesting too roughly or at the wrong time can shorten the fibers and affect their strength, appearance, and how well they perform in finished linen goods.
A. Timing and Method
When to Harvest
The key with flax is harvesting at just the right time. The ideal moment is when the plant starts yellowing but before the seeds are fully mature. This means the flax has grown long, strong bast fibers (needed for spinning linen yarn) but is still soft and pliable.
Flax that has been left too long in the ground will have woody stalks and brittle, stiff fibers that are hard to separate. Underripe flax that is harvested too early will not have developed strong enough fibers for quality yarn. Textile flax is a different crop from flax grown for seed oil (like linseed), and farmers prioritize fiber quality over seed value.
How to Harvest
Flax is uprooted (pulling up by the roots) rather than cut. This is a key traditional technique still used today for the best quality linen. The whole length of the stalk (fiber) is preserved by taking the plant out of the ground hole, including the long root end.
Uprooting by hand or machine pulls the flax straight from the soil and lays it out in parallel rows to dry. This is in contrast to cutting flax, which results in shorter fibers that can be weaker and less uniform. Cut stems are more likely to twist out of alignment during retting and processing, which can be a problem with linen blends or lower quality textiles.
Hand-pulling (manual harvesting) versus machine harvesting (mechanical harvesting)
Manual Harvesting:
Pulling by hand allows for careful control to avoid breaking the plant or damaging the root, where a lot of the long fiber is. While slow and labor-intensive, hand-harvested flax is still common in traditional or small-scale linen production areas (like Ireland or Lithuania).
Machine Harvesting:
Flax harvesters with multiple uprooting heads are essential for large-scale linen production. Modern harvesters carefully pull flax out of the soil and lay it uniformly for drying or retting. Machines are faster but can damage fibers if not adjusted properly.
Trends in the industry are toward more machine harvesting but often with techniques that mimic the precision of manual work. Some top producers still use hand-pulled flax or a mix of both methods to ensure higher-grade material.
B. Impact of Harvesting on Fiber Quality
Advantages of Early Harvesting
Harvesting earlier while the plant is still partly green results in softer and more supple fibers. These are naturally more flexible and have a brighter sheen, which is prized in high-end linen products. This makes the fiber easier to spin and results in a fabric that feels softer against the skin with a nice drape.
Harvesting later is better for the seed but means coarser, stiffer fibers are all that’s left to use for textiles. These are often relegated to lower-quality linen goods or used for other purposes like rope, stuffing, or insulation. Early harvested flax has a high percentage of long fiber suitable for premium fabrics.
Problems With Rough Harvesting
Linen’s reputation for strength is because of the length and durability of the long flax fibers used. Rough handling of the plant during harvesting or storage can easily break, crush, or kink fibers. This produces weak points in the yarn or visible flaws in the weave.
Damaged fibers are also more likely to knot or tangle up during retting and hackling, which prolongs the processing time and lowers the overall uniformity of the fabric produced. Avoiding fiber damage and preserving fiber length is vital to producing the longest and strongest linen threads later.
IV. Retting: The First Step in Fiber Separation
Once the flax is harvested, it needs to go through a process called retting before the fibers can be extracted. Retting is the first step in breaking down the flax stalk and separating out the individual fibers.
A. What is Retting?
Definition and Purpose of Retting
Retting is the controlled decomposition or rotting of the outside parts of a plant in order to free up the fiber bundles for later processing. In flax processing, retting is what softens and dissolves the pectin and other cellular “glue” that binds together the bast fiber bundles, xylem (woody core), and epidermis (skin) of the flax stalk.
Flax stalks harvested from the field are a tightly packed bundle of woody core and fibers that all need to be separated. Mechanical processing can physically break down the stem, but without retting, the layers of plant material are too rigid and stuck together to extract the actual textile fibers.
Biological Breakdown
Retting is a biological process that utilizes bacteria, fungus, or enzymes to selectively break down plant tissue. The flax stalk is only partially decomposed during retting; the goal is to dissolve enough of the outer pectin to allow the individual fibers to be separated later during mechanical processing.
Retting methods can include dew, water, or enzyme retting, each of which uses different types of microbial or enzymatic breakdown to produce the same results. Retting must be done correctly in the correct time frame; over-retting the flax can weaken the fibers and damage color, while under-retting means the stalk is still too stiff to separate.
B. Types of Retting
Flax can be retted through several methods and in different environments to take advantage of natural processes.
1. Dew Retting
Dew retting is the most traditional method still used today in Europe. The flax is harvested and spread out in long rows across fields and left in place to undergo natural retting by a combination of moisture and bacteria.
Three to six weeks are needed for dew retting, depending on the climate. The action of morning dew, sunlight, wind, and rain softens the flax stem. Natural soil microbes also contribute to the retting, though more slowly. Dew retting is the most environmentally friendly method with a minimal carbon footprint and only a short production cycle.
Advantages
Environmentally friendly (natural retting only)
Uses no added chemicals or large amounts of water
Produces long and soft fibers with rich color variations
Perfect for artisanal or organic linen
Disadvantages
Slow (weather dependent)
Inconsistent results if too dry or too wet
Chance of under- or over-retting due to rain and temperature changes
Dew Retting in Practice
Modern dew retting is the same process used for centuries in regions like Belgium, Holland, Ireland, Lithuania, Latvia, and parts of the UK. Since flax is slow to rot in the presence of air, dew retting places priority on maximizing drying and aeration as part of the retting process.
A key part is spreading the flax out in long straight rows, which is why dew retting is so often used in association with mechanical harvesting. Tractors and combines lay out the flax in uniform straight rows to maximize surface area for aeration. Shaking out the flax before dewing can also prevent clumping and mold.
Dew retting is best in cool, moist climates with regular dew and rainfall. Prolonged hot, dry weather or heavy rainstorms can both disrupt the process. Manual rolling or loosening of the flax may be necessary between retting periods to keep air circulating.
2. Water Retting
Water retting is the oldest known method and has been used for thousands of years in many regions that produce flax or other bast fibers. The flax stalks are submerged in water (ponds, rivers, tanks) and bacteria work to break down the stalk in as little as four to ten days.
Advantages
Faster than dew retting
Generates bright-colored and very fine fibers
Uniform retting if conditions are consistent
Disadvantages
Pollutes waterways and produces waste that can be a disposal problem
Requires large amounts of clean, stagnant water
Labor-intensive and water-dependent; easy to over-ret
Machine harvesting can damage the fibers if not done correctly
Water Retting in Practice
Water retting was once the most common retting method in the world, but is on the decline due to environmental impacts. The technique is still used in some regions like Egypt, India, Greece, Israel, Poland, and Ukraine. For centuries, Irish flax was water-retted in local rivers and lakes.
Water retting is faster than dew retting, which is a key benefit. Only a few days are needed for the bacteria to multiply and accelerate the decomposition process. The result is a very fine, consistent fiber that is often brighter in color, which has aesthetic benefits.
Water-retted linen can be visibly different depending on the water source, leading to flax sourced from a specific lake or river having a unique market advantage. The most common problems with water retting are water pollution and disposal of the resulting waste.
Manufacturers must either find a way to remove the biological sludge and flax waste at the end of the process or work to reduce or reuse it. The use of water-retted flax in some regions has been outlawed because of these concerns. Regulators in the EU and North America have forced many mills to switch to dew retting or enzymes.
3. Enzyme Retting
Enzyme retting is a newer and more industrialized method where specialized enzymes are used to process the flax. Enzyme retting uses the same general principle of biodegrading the plant tissues but in a controlled environment with biologically-engineered catalysts (enzymes).
Advantages
Precisely controlled and consistent
Can be done in a few hours or days rather than weeks
Uses less water than traditional water retting
Low environmental impact if using biodegradable enzymes
Disadvantages
Expensive and more complex
May shorten the fibers slightly depending on enzyme selection
Used mostly in industrial-scale production
Enzyme Retting in Practice
Enzyme retting is gaining ground in industrial and large-scale linen production for the control it provides. Enzymes like pectinase or cellulase break down pectin or cellulose, which is the main “glue” that binds the flax fibers to the woody parts of the stem.
Chemical retting is closely related and was a commonly used method in the past. Chemical additives (alkalis, acids, oxidants) accelerate and control retting rather than relying on natural processes.
Comparison of Retting Methods
Method Time Needed Environmental Impact Fiber Quality Cost
Dew Retting 3–6 weeks Low (natural) High (natural variations) Low
Water Retting 4–10 days High (pollution risk) High (uniform) Moderate
Enzyme Retting 1–3 days Low–Moderate High–Very high (controlled) High
Artisanal and small-batch linen producers tend to focus on dew retting for the cleanest process. Modern flax mills often invest in enzyme retting facilities for greater speed and control.
V. Breaking and Scutching: Extracting the Fiber
After flax is harvested and retted (whether it’s field retted, water retted, or enzyme retted), it undergoes one of the most transformative stages in linen production: the extraction of bast fibers from the remaining plant material. The process, known as breaking and scutching, involves liberating the long, silky fibers within the stalks, making them ready for further processing into linen.
A. Breaking
Mechanical Braking: Breaking up the Stalk
Breaking is the initial physical process in extracting fibers. It involves a mechanical operation that fractures the woody exterior of the flax stalk, thus making it easier to separate the inner fibers. Traditionally, this was done by hand using a wooden tool known as a “flax break” which operated like a miniature guillotine. Bundles of flax stalks were fed through the device, which crushed them between wooden blades, cracking the woody core (called shives) without harming the delicate bast fibers inside.
Modern breaking machinery uses the same principles, but instead of wood, employs metal rollers or fluted drums to exert even pressure. The objective is to disintegrate the hard outer covering (the xylem and epidermis layers) while keeping the inner fibers as long and intact as possible.
Breaking does not actually separate the fibers from the plant material; it simply loosens and breaks apart the woody matrix that surrounds them. At this stage, the material appears rough and tangled, with the fibers still embedded in the broken stalk fragments.
Outer stalks vs. Inner fibers
Breaking exploits the structural differences between the fiber and the woody stem of the flax plant. Bast fibers run longitudinally along the flax stalk, while the harder components (shives and pith) encase them like bark. When subjected to the breaking process, these woody elements crack into small pieces that can be eliminated in the next step, scutching.
If the breaking is too vigorous, however, the fibers can be damaged, becoming shortened or frayed. A light, well-timed break is therefore critical to preserving the long line fibers that linen is known for.
B. Scutching
Scutching or Beating: Removing Stalks and Waste
Once breaking is complete, the next phase in fiber extraction is scutching (also called beating or scraping). This process removes the woody debris and other broken stalk fragments from the flax, leaving behind clean, flexible fiber bundles.
Wooden blade removal: traditional scutching tools
In traditional flax processing, scutching was a hand operation that used a wooden blade and a fixed board. A hank of broken flax would be hung over a vertical board (also called a “scutching board”) and struck with the scutching knife in a rhythmic motion, knocking loose the broken stalks and other impurities.
Industrial scutching machines automate this process. Instead of free-flying wooden paddles, modern scutchers have rotating paddles or beaters that strike the flax as it is held in place, knocking the shives free without damaging the fibers. Vacuum systems may also be present to capture debris or separate the usable fiber from the dust and waste products.
The goal of scutching is to produce long, clean, golden-colored fibers with as little contamination as possible. This step radically alters the appearance and texture of the plant material, making it more resemble a textile precursor than raw vegetation.
Producing clean line fibers
A well-executed scutching phase results in what’s called line flax fibers. These are the premium, long, lustrous strands used to make high-quality linen fabrics. Depending on the fineness and cleanliness, these fibers may be suitable for light apparel, fine linens, or even lacework.
The shorter fibers and other debris left behind are known as tow. Two fibers are coarser and less valuable than line, but they are not wasted and are used in a variety of applications (discussed in the next section).
C. Environment and Labor
Traditional hand-scutching vs. industrial scutching
Flax processing was once a major cottage industry, particularly in the British Isles, Eastern Europe, and the Low Countries (Belgium, Netherlands). In these regions, hand-scutching was often done by skilled artisans, and the methods have been passed down through generations.
Hand-scutching requires not only brute force but also timing and a light touch, as a strike that’s too hard or too soft can damage the fibers or fail to clean them properly. It produces exceptionally fine, artisan-grade linen, but it’s slow and expensive.
Industrial scutching, on the other hand, is designed for mass production. These facilities can process several hundred kilograms of flax per hour, greatly reducing costs and improving consistency. However, mechanization can sacrifice some fiber length or uniformity if not carefully monitored.
Labor conditions and regional practices
The transition from hand to machine processing has had significant consequences for labor. Mechanization can reduce physical strain and improve efficiency, but it also makes traditional knowledge and skills obsolete and alters rural economies that once depended on artisanal flax work.
In some developing countries, manual scutching and breaking still take place, often under suboptimal working conditions. Dust from broken flax can be a respiratory hazard, and repetitive motions over long hours may lead to injuries. As with most textile production, linen is most ethically produced when fair labor practices and safety protocols are in place.
France and Belgium in particular have come to be associated with high standards for both mechanical quality and labor treatment, which is why “European Flax” is now a mark of both ethical and premium linen.
VI. Hackling (Combing)
Breaking and scutching leave the flax fibers mostly free from their woody casing, but they remain rough, tangled, and full of residual particles. The final stage in flax preparation before spinning is hackling, also known as combing. This delicate process transforms the coarse material into soft, aligned strands ready for spinning into yarn.
What Hackling is and does: Aligning and Softening Fibers
Hackling involves pulling the flux through a series of combs or hackles with increasingly finer metal teeth. The movement detangles and straightens the fibers, aligning them parallel to one another and removing the last of the unwanted material—such as straw, dust, and broken fibers.
Hackling is to linen what brushing long hair is to hair care, after it’s been washed and air-dried. It smooths and refines the fibers, and organizes them into a uniform bundle.
The final product is a set of silky, light-colored fiber strands known as line flax, which is the finest form of linen fiber.
Removing Remaining Straw, Short Fibers (Tow), and Impurities
Hackling is also critical to cleaning the bulk of the fiber mass. Even after scutching, small straw fragments and clumps of tangled fiber remain. As the flax is combed through the hackles, these bits are caught in the teeth and removed, ensuring that only the cleanest and longest fibers are left in the final bundle.
This step not only improves the fiber’s overall usability but also determines the yarn’s final smoothness, luster, and spinnability.
Hackling separates the fiber mass into two grades:
Line flax:
The longest, most uniform fibers, used for high-end linen textiles.
Tow flax:
The shorter, coarser fibers that get caught in the combs and teeth, often used in rope, coarse cloth, or blends.
Producing Long, Lustrous Line Fibers
The key to luxury linen lies in the line flax produced by effective hackling. These fibers can reach up to 90 cm long, which gives them a natural sheen, a soft drape, and superior strength when spun into yarn.
Line flax can be spun into very fine yarns, making it suitable for garments (summer shirts, handkerchiefs, tablecloths) or lace. Its natural luster is one of linen’s most coveted features, and much of it emerges during hackling.
Line flax may be hand-hackled for artisanal production, or it may be processed through automatic hackling machines in large industrial settings.
In either case, the objective is the same:
refine and perfect the fiber before spinning.
Use of Tow Fibers in Coarser Linen or Blended Fabrics
While tow fibers are shorter and more irregular, they are by no means wasted.
Tow is often:
Carded into yarn for strong, durable fabrics (canvas, upholstery).
Blended with cotton or synthetics to reduce cost.
Used in nonwoven textiles such as insulation, padding, or paper.
Because tow is coarser, it’s less commonly used for next-to-skin applications but it plays a vital role in the full utilization of the flax plant and ensures minimal waste in the linen production chain.
VII. Spinning the Linen Yarn
At long last, our carefully processed flax fibers have made it through the arduous steps of breaking, scutching, and hackling. They are now finally in a condition suitable for spinning into linen yarn. Spinning is the critical point in linen processing where the transformed fiber begins to feel and look like the fabric most of us know – dozens, hundreds, or even thousands of small fibers pulled out from their bundles and twisted into long, continuous threads of strength.
The way these linen threads are spun largely determines the texture, strength, and appearance of the fabric they eventually become. Spinning can be done by hand or machine, but in either case requires care and precision to create high-quality yarn.
A. Traditional Spinning Techniques
A Brief History of Hand-Spinning
Of course, traditional flax spinning predates any written history by thousands of years. In Egypt and Mesopotamia, as early as 8,000 years ago, the first human civilizations were processing flax into linen yarns and fabrics. The art of hand-spinning flax, using only simple tools, is one of the earliest textile crafts known to humanity.
Spinning flax by hand is incredibly slow and labor-intensive work, even with decades of experience. But it was a time-honored trade and one passed down through generations, traditionally performed by women in the home.
Spinners would work the line flax (the long, glossy fibers teased out during hackling), carefully drawing and twisting the fibers into thread. The quality and consistency of the resulting yarn was often a point of pride for a spinner, especially in societies where linen was an important ceremonial, domestic, or trade product.
Flax is naturally very stiff and slick, so it’s more challenging to work with than wool or cotton, and also needs moistening to allow the fibers to stay clumped together. In the past, spinners had to lick their fingers or use a wet rag to keep the flax from breaking apart as they drafted.
Drop Spindle and Spinning Wheel Methods
Early hand-spinners used one of two basic tools: the drop spindle or spinning wheel.
The drop spindle is one of the earliest spinning tools ever used throughout human history. It consists of a stick (shaft) and a weighted disc (whorl) at one end. The spinner attaches a tuft of flax to the spindle and then spins the shaft, allowing the fiber to twist into yarn as it is drawn out and rotated.
Drop spinning is relatively simple and portable, but the process is quite slow.
By the Middle Ages, a much faster mechanism was developed: the spinning wheel. The type most commonly used for linen was the Saxon wheel, with adaptations made specifically for spinning long staple fibers.
The wheel consists of a large wheel with a spinning cord attached to a mechanism that twists the fibers, called the flyer. The spinner sits with the wheel at their feet and a distaff (vertical post holding a bundle of flax) on their left side. As the wheel spins and twists the fibers, they are drawn out and wound onto a bobbin, making the process much more efficient.
Hand Spinning for Centuries
Hand spinning was of course the dominant method of yarn production for many centuries and is still used by some artisans today for high-end, heirloom-quality linen yarns.
B. Modern Spinning Methods
Wet vs. Dry Spinning (Wet for Finer Yarns)
Industrial spinning of linen is almost entirely mechanized and tightly controlled. However, the most important distinction between different modern flax spinning processes is the difference between wet spinning and dry spinning.
Wet Spinning:
In wet spinning, the flax fibers are passed through a hot water bath immediately prior to being drafted (drawn out). The hot water further breaks down the remaining pectins and lubricates the flax, allowing for a much tighter, smoother twist.
Wet spinning produces finer, glossier yarns better suited to lightweight or delicate linen products such as garments or fine tablecloths.
Dry Spinning:
Dry spinning does not include the hot water bath. The fibers are spun and twisted in their dry state. This produces a thicker, rougher yarn better for upholstery, canvas, towels, or rustic textiles.
Dry-spun yarns have a stiffer hand and may have more intentional or unintentional slubs and irregularities.
Wet spinning is more resource-intensive but typically produces a much better quality yarn, while dry spinning is faster and more energy-efficient.
Spinning Yarns of Different Weights and Textures
Modern spinning can produce flax yarn in a great range of:
Weights:
from ultra-fine thread to thick yarn for rugs or outerwear
Twists:
tighter twists for strength/slipperiness, looser twists for softness
Textures:
intentionally slubby (uneven) for rustic effect, or smooth for luxury fabric
The final weight, texture, and twist of the yarn depends not only on the spinning method but on the quality of the flax, the end use, and whether it will be a warp or weft yarn for weaving.
Industrial Spinning Machinery
Today’s spinning mills use a series of specialized machines that draw out the fibers into rovings (soft ropes of fibers), then twist these rovings into yarn and wind the yarn on cones or bobbins.
Modern spinning equipment is precision engineered, computer controlled, and capable of processing thousands of meters of yarn a day. Some wet spinning systems use closed-loop water recycling to reduce environmental impact.
Linen producers in France, Belgium, Lithuania, and other leading nations continue to innovate and perfect flax spinning methods to balance quality, efficiency, and sustainability.
VIII. Weaving Linen Fabric
Spinning may have been the culmination of the painstaking linen fiber processing, but weaving is the transformative point where linen production really comes to life. The weaving process is where literally thousands of handspun threads are intersected and interwoven to form real, structured, tangible linen fabric. Weaving gives linen its strength, drape, texture, and final look. Weaving linen can be traditional hand-production artistry, or high-speed industrial manufacturing.
A. Weaving Basics
Warp and Weft Threads Explained
Before diving into the actual weaving process, let’s clarify the two basic thread directions on a loom:
Warp threads are the threads running vertically in the loom. These are the threads that are set under tension during weaving and must be strong and stable.
Weft threads are also called fill or woof and run horizontally. They are passed back and forth through the warp threads to build up the fabric row by row.
In linen, warp yarns are usually dry-spun or blended for added strength while weft yarns can be wet-spun and more decorative since they are under less tension.
The intersection of warp and weft threads at various points creates a wide variety of possible weave structures with different properties.
Common Weave Structures:
Plain, Twill, Damask, Herringbone
There are a number of common weave structures found in linen products:
Plain Weave
The most basic and durable weave pattern. It alternates over one warp thread, under one warp thread.
Produces a flat, crisp fabric with high stability and strength.
Used for dish towels, sheets, shirting, base fabric.
Twill Weave
Creates a diagonal ribbed pattern (e.g. over two, under one).
Softens drape and adds more texture compared to plain weave.
Used for trousers, heavier apparel, upholstery, canvas.
Damask Weave
Jacquard-woven patterns that mix satin and plain weave structures for raised designs.
Generally monochromatic but highly reflective and elegant.
Table linens, high-end home décor, upholstery.
Herringbone and Chevron
Variants of twill weave that create zigzag or arrow-like patterns.
Popular for tailored garments, scarves, classic menswear.
Offers both structure and subtle visual interest.
B. Types of Looms
Traditional Handlooms vs Power Looms
Historically, all linen was woven on handlooms like pit looms, treadle looms, and frame looms. On a handloom, the weaver must manually lift the warp threads (pedals or levers) and pass the weft back and forth using a shuttle.
Handlooms offer:
Full control over the tension, spacing, and design
Ideal for artisan or bespoke weaves
Rich texture variation and intentional irregularities
Artisan linen woven by hand (especially in countries like Lithuania, India, parts of France) is still highly sought after for its quality and character.
But for most commercial-scale linen production, manufacturers use power looms:
mechanized looms that:
Are able to operate at high speeds
Can create uniform fabric widths
Are able to incorporate complex designs with jacquard or dobby attachments
Power looms can be driven by electricity, compressed air, or even water in some eco-conscious factories.
Some high-end linen brands use a hybrid approach: slow-speed weaving with modern controls to retain the feel of handwoven fabric while maintaining high efficiency.
Influence of Weaving Technique on Fabric Feel and Durability
The weaving technique and type of loom used has a significant impact on the final linen fabric quality.
Weaving Factor Impact on Linen
Loom speed Faster looms can produce tighter weaves but cause more breakage of brittle flax fibers. Slow looms are gentler and retain more fiber softness.
Tension control Precise warp tension prevents yarn slippage and helps maintain even texture. In handweaving, tension is adjusted manually.
Beating force The force with which the weft is packed down. Heavy beating = denser, more durable fabric; light beating = softer drape.
Fiber lubrication Wet weaving (using mist or steam) increases sheen and reduces friction between fibers, improving softness.
Weaving can produce linen fabric that is sheer and lightweight like voile or cambric or very dense and heavy like canvas or upholstery linen. The weaving process is also where design and pattern options truly explode from subtle, tonal elegance to bold, graphic geometrics.
IX. Finishing the Fabric
The journey from fiber to fabric doesn’t end once flax yarn has been woven into cloth. To transform rough material into refined linen suitable for the marketplace, it must go through various finishing stages. These include washing, bleaching, dyeing, softening, and more. Finishing processes impact everything from performance and aesthetics to price and application.
While previous phases were more about fiber extraction and structure creation, finishing is about perfecting and enhancing the final cloth. As it comes off the loom, linen woven from “grey” yarn may be stiff, uneven in shade, or have a slightly scratchy texture. The finishing stage corrects that. Final treatments produce the softness, color, and beauty that make linen so desirable.
A. Washing and Bleaching
Natural vs Chemical Bleaching Methods
Newly woven linen is often a dull, off-white to light brown shade. However, to create brighter linen—required for products like white tablecloths or pastel garments—it needs bleaching.
Two methods are typically used:
1. Natural Bleaching (Sun Bleaching)
A low-impact, traditional technique using repeated washing and exposure to sunlight to gradually fade the color over time.
Relies on UV rays and oxidation to naturally bleach the fabric.
Is more gentle on the linen fibers and preserves strength.
Favored by organic or artisan producers.
2. Chemical Bleaching
The most common practice in industrial production where speed and consistency are a priority.
Involves adding bleach agents like hydrogen peroxide or sodium hypochlorite to strip color.
Hydrogen peroxide is less damaging and more environmentally friendly.
Must be followed by neutralization and thorough rinsing to avoid fiber damage.
Both methods aim to prep the fabric for dyeing or final use. Aggressive or careless bleaching with chlorine can weaken the linen and reduce longevity.
Pre-shrinking and Cleaning the Fabric
Linens must also be scoured to remove oils, sizing agents, and processing impurities from spinning/weaving before sale or use.
This cleaning with hot water and mild alkaline solutions (soda ash) does the following:
Removes waxes and pectins.
Eliminates processing lubricants and residues.
Helps improve absorbency and dye receptivity.
Allows for pre-shrinking, or sanforizing.
Linen also tends to shrink in its first few washes, so the pre-shrink step stabilizes dimensions and prevents surprises during production/garment wear.
For apparel-grade linen, this step is essential to ensure exact cut sizes.
B. Dyeing and Printing
Natural Dyes vs Synthetic Dyes
The cellulose fibers in linen can be dyed with both natural and synthetic colorants. Linen does have a lower dye uptake compared to cotton, though. It’s a more rigid, less porous fiber.
1. Natural Dyes
Obtained from plant (indigo, madder) sources, minerals, and insects like cochineal.
Common in artisan or eco-linens.
Need mordants like alum or iron salts to attach dye to the fabric.
Give more muted, earthy colors that may fade over time.
2. Synthetic Dyes
These include reactive dyes, vat dyes, and direct dyes.
Synthetic colorants provide:
Greater color options.
Higher fastness properties.
Better cost efficiency.
Reactive dyes create strong chemical bonds with the fiber and are especially effective on linen.
Vat dyes (like indigo) are insoluble in water but can be reduced to a soluble form for dyeing in alkaline solutions.
Synthetic dyes are more consistent in color matching and resistant to sunlight/fading from washing.
Luxury or fashion linens may combine natural and synthetic dyes to create unique color effects.
Common Patterns and Colorfastness Considerations
Linen can be colored via several different techniques:
Piece Dyeing:
The whole fabric is dyed after weaving. Solid color linens.
Yarn Dyeing:
Individual fibers are dyed before weaving. Patterns like plaids, stripes, checks.
Printing:
Applying designs with screen or digital printing techniques. Florals, graphics, custom artwork.
Colorfastness—resistance to fading from washing, rubbing, and light—is an important consideration. Linen fabrics are often used in home textiles like curtains and bedding where they may be exposed to strong sunlight. Therefore, good color fastness properties are a priority.
Quality dyes and finishing treatments can significantly improve performance. Linen is typically tested for:
Wash Fastness (resistance to fading during laundering)
Lightfastness (resistance to fading from sunlight exposure)
Rubbing fastness (resistance to abrasion)
C. Softening and Texturizing
Use of Enzymes or Mechanical Treatments to Soften Linen
Raw linen fabric will feel crisp, or even stiff, when first produced. Some people enjoy this tactile sensation. Others want something softer, smoother, and more fluid to the touch. Softening techniques can modify linen’s hand (texture) and drape to suit different applications.
1. Enzyme Finishing
Cellulase enzymes are used to selectively break down the outer layer of the linen fibers on a microscopic level.
This process softens the fabric without weakening its overall structure.
Regarded as more environmentally friendly than chemical softeners.
Produces a “lived in,” washed look common in premium clothing and bedding.
2. Mechanical Softening
The fabric is passed through rollers, tumblers, or sand washers to abrade the surface.
Like stone-washing denim, this process physically breaks in the fibers.
Adds surface texture, slubs, and variation in visual appearance.
Gives linen that rustic, casual aesthetic.
3. Chemical Softeners
May be used in large-scale production to achieve fast softening at a low cost.
Include silicone-based or emulsion agents.
Build-up from overuse can cause breathability problems, environmental impacts.
How Finishing Affects Final Fabric Feel, Drape, and Use
Finishing gives linen its final hand, look, and feel. Depending on treatments applied, it can be any of the following:
Crisp and formal (tablecloths, tailored blazers)
Light and gauzy (summer dresses, curtains)
Soft and “worn in” (bedding, scarves, casual apparel)
Finishing can also be used to adjust performance characteristics such as:
Wrinkle resistance (many linens receive some treatment to reduce creasing)
Shrinkage control
Stain repellency (particularly for home textiles)
The goal is to ensure linen feels and performs the way consumers expect and matches its intended use.
X. Quality Grading and Inspection
Not all linen fabrics are created equal. As finished material comes off the loom, it must be graded and inspected to determine its quality level and classification. This helps manufacturers and retailers communicate the level of linen they are using and ensures it will meet performance or luxury expectations.
A. How Linen Is Graded
Many criteria determine the quality of linen fabric. Most are related to the original flax fiber used and the processing skill applied:
1. Fiber Length
Closer to full-length (line flax)
= smoother, stronger yarns
Coarser, shorter fibers (tow)
= more irregular, often used for blends or lower grade
2. Color and Uniformity
Fine grade linen will have consistent color, whether natural ivory or dyed, with no patchiness or streaking.
Blotches may indicate over-retting, poor scutching, or dyeing issues.
3. Purity and Cleanliness
Lint, husk, and shive particles should be absent in high-grade linen.
Visible foreign matter or slubs (unless intentional) lower grade.
4. Texture and Hand
Fine linen has a consistently soft yet firm hand, pleasant to touch.
Coarse, scratchy texture
= low quality, under-refined linen.
B. Standards for Fine Linen Fabrics
For a fabric to be considered premium or fine linen, it usually has the following:
Made from line flax, not tow
Made with wet spinning and careful weaving
Dyed and finished using high-standard processes
Has appropriate thread count and density for intended use
Passes quality inspection (typically under UV and white light for flaws)
Irish linen or Belgian linen status are so sought after that they serve as de facto quality categories.
C. Certifications and Origin Labels
Certifications and origin labels provide helpful guidance to both consumers and professionals. A world filled with misleading textile claims has made this information all the more important.
1. Masters of Linen®
Certification program by the European Confederation of Flax and Hemp (CELC).
Certifies 100% European origin for linen from flax farming to final fabric production.
Focuses on traceability, sustainability, transparency.
Considered a mark of excellence and ethical production.
2. OEKO-TEX® Standard 100
Certification ensures that linen fabric has no harmful chemicals and is safe for human contact.
Common for organic or eco-conscious brands, children’s clothing/textiles.
3. GOTS (Global Organic Textile Standard)
Certification for organic linen products.
Includes social and labor standards for production, in addition to no synthetic pesticides/dyes.
4. Belgian Linen™
Label reserved for linen woven in Belgium and made with European flax.
Iconic for centuries of craftsmanship and quality.
Certifications help consumers sort through the linen market, identify authentic and responsible fabrics, and support traditional producers with modern ethics.
XI. From Factory to Fabric Store
The long journey of linen from plant to product doesn’t end after weaving and finishing. Linen fabric must then be packed, shipped, marketed, and presented for sale in fabric stores, to home décor companies, fashion designers, and ultimately—consumers.
In this stage of the production chain, some of the most interesting things we can ask are:
how does fabric get from a factory to a fabric store?
Or how do we know what’s inside that bolt?
Or where does this bolt come from? Knowing where linen comes from, and how it reaches fabric stores and boutiques, can help consumers make more educated choices and decisions, and see the bigger picture.
A. Packing and Shipping
Linen is shipped to retailers, distributors, and other customers in either bales or on rolls.
The packing method is determined by:
The type and weight of the fabric
The end-use (wholesale vs retail)
Destination (local or export)
1. Rolls
Fabric rolls are the most common method for packaging apparel and retail-grade fabric.
Fabric is tightly wound around a cardboard or plastic tube.
Rolls range from 10 to 100 meters depending on weight and fabric thickness.
Rolled-up linen is much easier to measure, handle, and cut for sale.
2. Bales
Fabric bales are used mostly for bulk or tow-grade linen.
Fabric is folded, pressed, and wrapped in plastic or burlap for shipping.
Bales can weigh several hundred kg and are designed for wholesalers or manufacturing customers purchasing large quantities.
Fabric bales and rolls are then labeled with information about:
Weight per meter
Color and dye-lot number
Fabric type (100% linen or blend, etc.)
Country of origin and textile certifications (Masters of Linen)
Packaging is also designed to keep the linen from wrinkling, getting contaminated, or absorbing moisture on its way to fabric stores.
Transport from Mill to Distributor and Retailers
Linen fabric is produced in only a few regions (Europe, China, India) but distributed worldwide for sale. There are a few key methods and steps that help keep the system streamlined.
1. Inland Transport
Trucks and trains carry fabric bales and rolls from production mills to warehouses, shipping ports, or local distribution centers.
Handling and stacking must be done carefully to avoid wrinkling and tearing.
2. International Shipping
Cargo ships, air freight, and freight trains move linen across oceans and continents.
Shipping requires export papers for the fabric’s country of origin, commercial invoice, customs clearance form, and material safety declaration.
3. Distribution Centers
Fabric wholesalers, distributors, or large retail customers receive shipments.
Bulk material is often cut or reprocessed by these middlemen into units ready for sale at retail outlets.
Rolls are re-rolled, cut to size, and tagged or packaged for sale to the customer.
4. Retail and eCommerce
Fabric stores source rolls of linen for individual customers, DIY and craft projects, fashion designers, and small businesses.
Online fabric stores also offer cut-to-order linen fabric with images, swatches, and detailed descriptions.
Logistics and ethical, efficient transport systems can help ensure that linen fabric travels fast, arrives in good condition, and remains traceable in a closed-loop, minimal-waste environmental system.
B. How Do Consumers Encounter Linen?
Consumers have two primary ways of encountering or buying linen products:
Fabric by the meter or yard
Finished garments and linen products
Each presents a very different type of experience:
1. Fabric Form (DIY, Custom Use)
Fabric by the meter/yard or bolt is sold in fabric or craft stores and online.
Popular with sewists, fashion students, interior designers, crafters, and other custom projects.
Offers the flexibility to customize, design, and personalize projects.
Labels will have information on:
Fabric width
Weight (gsm)
Shrinkage range and allowance
Cleaning, washing instructions
Country of origin, etc.
Many high-end linen fabric stores also sell swatches, for customers to feel and examine fabric samples before they buy.
2. Finished Garments and Products
Finished linen items include shirts, dresses, suits, coats, scarves, curtains, napkins, tablecloths, towels, bed linens, and more.
Tags will be on the inside of the product:
“100% Linen” or “Linen-Cotton Blend”
“Made in France” or “Crafted in Lithuania”
Care instructions and symbols (machine wash, dry clean, iron)
Textile certifications (Masters of Linen, OEKO-TEX®)
Finished garments and products highlight the aesthetic appeal of linen, and how it responds to cutting, stitching, pressing, and tailored design.
The Fabric Label:
Key Information and Quality Markers
A quick glance at the label can help a consumer understand the quality, country of origin, and certifications of linen.
Label Term Meaning
100% Linen Pure linen, 100% flax fiber. Highly breathable and textured.
Linen Blend Linen often mixed with cotton, viscose, or polyester to add softness or lower cost.
Belgian Linen Linen woven in Belgium from European-grown flax. Sign of higher quality.
Masters of Linen® Material produced in the EU from field to fabric.
OEKO-TEX® Certified A certification that tests textiles for harmful chemicals or residues.
GOTS Certified Linen Linen produced from organically-grown flax and under ethical labor standards.
High-quality labels and material often means:
Longer fibers from line flax.
Consistent weave structure.
Less slubs and flaws.
Ethically sourced and environmentally friendly.
Customers who ask more questions, and pay attention to textile labels, have the power to make more conscious decisions and support quality production and sustainability.
XII. Linen Production and the Environment
Linen has often been held up as the poster child for sustainable textile production. Natural, biodegradable, low-energy, and far more eco-friendly than other common fabrics, linen can help consumers live more responsibly and comfortably. Yet when production is scaled to an industrial level, certain challenges arise and processes change. To be more environmentally responsible, modern linen producers are finding new solutions.
A. Natural Advantages
Biodegradable and Recyclable
The most obvious advantage of linen, when we talk about environmental impact, is biodegradability.
Composed entirely of plant-based cellulose fibers, linen will decompose naturally given enough time:
100% linen garments, sheets, curtains, etc. can biodegrade in as little as several weeks to a few months.
Linen will not pollute waterways with microplastics, as synthetics like polyester or nylon will.
Old or unused linen can be recycled and used as paper, home insulation, or industrial materials.
Buyers who embrace circular fashion and want to avoid textile waste have few better options than linen.
Minimal Chemical Use
Linen generally involves far fewer chemical inputs than cotton, through its whole production chain.
Farmers grow it without pesticides.
Retting uses dew or enzymes instead of chemical solvents.
Dyes can be more gentle, and the material retains its color even when dyed with natural pigments.
Organic linen is also common in natural and holistic clothing lines.
Low Water Footprint
Flax is extremely drought-resistant, and linen is one of the least water-intensive textiles on the planet.
Crop Water Use (per kg fiber)
Flax (Linen) ~650 liters
Cotton ~10,000 liters
Since high-quality linen is mostly rain-fed, linen is especially good for regions where water is scarce or agricultural resources are limited.
B. Challenges in Industrial Production
In spite of the natural advantages of flax and linen, the modern industry presents a few environmental challenges.
Energy and Water Use in Retting and Finishing
Certain parts of the linen production process use more water or energy, particularly if not optimized for a sustainable system.
1. Water Retting
Process of soaking flax stalks in water tanks or ponds.
Creates risk of water source pollution if flax waste and liquid are not properly filtered and disposed of.
Must be carefully handled by the end-user.
2. Wet Spinning and Dyeing
Consumes water and energy for scouring, spinning, and wet-finishing.
Chemical and mechanical efficiency can still result in carbon emissions.
Synthetic dyes and softeners, if misused, will produce more toxic wastewater.
3. Drying and Calendering
Uses steam heat and mechanical compression, consuming energy.
Solar energy, waste-heat reuse, and more can lower the carbon footprint.
Inefficient or unregulated production can quickly undo the natural sustainability of flax cultivation.
Need for Cleaner, Circular-Loop Methods
To address these production challenges, many linen producers have found ways to adopt cleaner systems and green standards:
1. Closed-Loop Processing
Includes closed systems for water recycling, chemical reuse, and zero waste.
Used in enzyme retting, dye baths, and finishing work.
Drastically reduces the environmental impact of linen production.
2. Renewable Energy Use
Solar and wind energy now powers many flax farms and spinning mills, especially in Europe.
Carbon footprint can be cut by up to 90%.
3. Localized Supply Chains
Short supply chains that keep cultivation, spinning, weaving, and finishing in the same country or region.
Consumers have fewer transportation-related emissions.
The Masters of Linen certification program also supports this.
4. Natural Dyes and Plant-Based Finishes
Interest in plant dyes like onion skins, turmeric, pomegranate rind, and other natural pigments is on the rise.
Provide low toxicity wastewater, in line with zero-waste production goals.
By using time-tested agricultural techniques and modern innovation, the linen industry is leading the way to a more ethical textile economy that values our shared ecological future.
XIII. Traditional vs Modern Linen Making
The story of linen is not just about the process of going from flax to textile, but also where, when, how, and by whom. Linen production is by no means static—technologies, methodologies, and even ideologies have all changed throughout history, though the basic material has remained the same. Linen is now made both traditionally and by industrial scale, by hand and by machine, by artisans and by corporations.
In this section we’ll look at the differences between craft linen and fast textiles, the increasing slow textiles movement, and the recent artisanal linen revival.
A. Craft-Based Artisanal Production
Linen, by its very nature as a domestic and versatile fiber, was often made entirely by hand for thousands of years. The linen was grown in local fields, retted, processed, spun, and woven by artisans who had been making linen for generations.
1. History of Linen Culture in Ireland and Lithuania
Ireland
Ireland was famous for linen production in the 18th and 19th centuries.
Ulster region (centered around Belfast) was the epicenter of global linen production.
Irish linen was prized for its very fine weave and whiteness, elegant drape and smooth hand.
Production remains very active in Northern Ireland, including traditional hand weaving, field bleaching, and finishing on small looms.
Lithuania
Lithuania is one of the oldest European countries with a linen history stretching over 4,000 years.
Linen is also a very important part of national cultural identity.
Lithuanian linen has a natural color and texture, and is usually undyed or plant-dyed.
Local artisans value minimal linen processing (natural dew retting) and manual finishing.
Scarves, bed linens, towels, and clothes are very popular.
Traditional methods of production are still honored in these countries and others including Latvia, Poland, and northern France/Italy, prioritizing a hand touch over the use of machines.
2. Techniques & Tools Used in Hand-Linen Production
Hand flax harvesting with sickles or pulling up by roots
Dew retting on the field
Hand scutching with a wooden blade
Hackling with an iron comb
Drop spindle or foot treadle spinning
Traditional wooden loom weaving
3. Qualities of Artisanal Linen
Texture is more varied and unique
Hand is usually softer
Quantity limited (sometimes one-of-a-kind)
Rooted in place and identity
Ethical and sustainable practices
Artisanal linen is usually more expensive, but more luxurious, durable, earthy, and thoughtful than mass-produced textiles
B. Mass Production for Fast Fashion
Fast Fashion Brands. With increased global demand, and an expansion in where linen was being used (fashion & home decor especially), linen making had to become mass production to be fast and affordable.
1. Automated Linen Mills
In countries where labor is very cheap and farm land is plentiful like China, India, and Pakistan, linen is often:
Mechanically harvested with large farming equipment
Retted with water or enzymes in tanks
Dry spun or wet spun on machines
Produced with air-jet or rapier looms
Mechanically finished with softeners or bleach
Millions of meters are often produced per year and sold to global brands or retailers.
2. Linen for Fast Fashion
Big-name apparel companies have been incorporating linen into their spring/summer lines as:
Lightweight
Breathable
Natural
Eco-friendly
However, the value and veracity of these claims are often:
Mixed/blended with synthetics
Chemically finished to compromise softness/breathability
Made in less environmentally responsible ways that counteract linen’s benefits (energy from fossil fuels, harmful dyes/preservatives)
As with all fast-fashion textiles, the price usually reflects low processing standards, cheap labor, and lack of environmental concern.
3. Tradeoffs with Industrial Scale
Aspect Traditional Linen Industrial Linen
Labor Hand labor by artisans Machines and sometimes unregulated labor
Quality High & inspected Variable by demand and production rate
Sustainability Low/zero impact methods Mixed and more opportunity to pollute
Price Premium quality Lower price
Availability Rare/limited Abundant
C. Revival of Interest in Slow Textiles & Artisanal Linen
Slow Textiles. In the past few years there has been a slow textiles movement that takes inspiration from the slow food movement.
1. Definition of Slow Linen
Linen is produced in small quantities using mostly natural and traditional methods.
Values soil health, water conservation, and fair labor.
Sold directly by the producer or through a small brand with a transparent supply chain.
2. Drivers of the Revival
Consumer knowledge about greenwashing and textile waste
Interest in handmade and high-quality heritage products
Resurgence of tactility, texture, natural materials in design
Interest in own less, own better philosophy
3. Examples of Modern Artisanal Linen Brands
Rough Linen (USA)
– Makes linen from European flax grown sustainably in Lithuania. Sewn by hand or machine in the US, no chemical treatment.
Fog Linen Work (Japan)
– Inspired by Japan and Scandinavian traditions, these table linens are modern but traditional in spirit.
Not Perfect Linen (Lithuania)
– Custom made, hand sewn linen clothing and clothing blanks, using only soft, Nordic linen.
XIV. Final Thoughts
Let’s take a moment to review what we have learned and experienced as a result of this deep dive into the history of linen, as we follow the incredible journey from field to fabric.
A. Reflection on the Process from Flax to Linen
Linen Cultivation
– In temperate climates, flax can grow with relatively low water and chemical inputs.
Flax Harvesting
– Retting is a necessary step to make linen fibers supple and strong.
Retting
– Loosens fibers from woody stem
Breaking & Scutching
– Breaks the woody stalk to remove fibers and yield line flax.
Hackling
– Brushes and aligns fibers, removing tow and any unwanted material
Spinning
– Twists linen fibers into yarn (wet or dry).
Weaving
– Combine yarns to form fabric (handloom or power loom).
Finishing
– Chemical treatment & washing to achieve desired texture, color, and finish
Grading & Certification
– Linen is often graded by fiber fineness, weave tightness, and water use.
Packing & Retail
– Exported as bolts or pre-made products with markers for transparency, origin.
Review on Ecology of Linen
– Natural qualities of linen, where we can improve on more industrial approaches.
The final part of the flax to linen transformation is the weaving process, during which two or more sets of yarn are interlaced at right angles to form a linen fabric. In industrial processes, this can be performed almost entirely by machines, and the techniques for weaving linen differ very little from weaving cotton or wool. However, weaving was the last stage of production to be mechanized, and still today many people choose to weave their linen by hand, especially in smaller artisanal businesses.
Hand weaving is a highly skilled task, and in some cultures and family lines, this knowledge has been passed down through the generations. Different loom structures (horizontal or vertical, treadle- or hand-powered) and different types of yarn (even the thickness of the yarn can vary by spinning method) can produce significantly different textures and patterns, even if the raw linen is the same. Weaving linen by hand is a craft that has continued for thousands of years, and even today most small-scale artisans will use traditional hand-powered looms at some point in their production.
Finishing refers to the steps taken to improve the final characteristics and quality of linen. Finishing can include washing the linen to remove any remaining starches and pilling, bleaching to achieve a white or uniform color, as well as a variety of chemical treatments to improve characteristics like softness, smoothness, wrinkle resistance, and so on. Most commercial linen used today will have at least been washed and bleached after production.
Finishing techniques and substances have developed over time, but also now must be mindful of both environmental and human safety impacts of certain chemicals. Linen often receives final softening and brightening treatments as it is an important part of creating the desired hand and appearance of the fabric for home furnishing or clothing. Some chemical treatments can be harsh and polluting, and one of the goals of more ethical and environmentally focused brands and mills is to find substitutes that have lower impact and toxicity. It’s also important to note that while we have identified the industrial finishes that are commonly used, individual linen makers may also create their own final treatments to get the feel and look they want.
Once linen has been finished, it will often be “graded” by the producer or an independent agency. Grading refers to the overall quality of the textile, and can involve factors like fiber fineness, weave tightness, amount of water use in the process, even how the textile might perform in specific applications like water resistance or snag resistance. This grading can then be used to help create a certification program (like GOTS) or be used in marketing and labeling to help consumers understand the relative quality of the product.
The final stage of the flax to linen production journey is packing the linen textile into bundles, rolls, or finished items and sending them to retail. This usually involves weighing and tagging the products, wrapping, and shipping. It is an important stage as it usually marks the last chance for quality and supply chain control before the finished textiles reach the consumer.
For retailers or consumers, it’s possible to see the tags on bolts of linen or garments to see where it came from, what grades it received, and other useful information like fiber content, thread count, and so on. In recent years there has been a move to use the tags on fabrics and clothes as marketing and a way to ensure supply chain transparency, which is an important development given how long supply chains have been and continue to be for linen.
At this stage, it is worthwhile to reflect on the time, effort, care, and skill that has gone into transforming flax into linen. It’s easy to take for granted how a plant fiber makes its way from fields to clothes or curtains, but by tracing the linen making process, we hope you have developed an increased appreciation and even wonder at the world of textiles.
B. Gratitude for Craftsmanship and Sustainability
Linen, which can be spun by hand in a cottage in Lithuania or woven by machines in a state-of-the-art European factory, is an example of both the highest textile craftsmanship as well as the most sustainable. At its best, linen represents both artisanship and modern technology.
As such, it is a textile that has deep respect for both the earth and the people who work on that earth to bring it from fields to your wardrobe or home.
For these reasons, linen is so meaningful in both the history of textiles and its future.
C. Inspiration to Appreciate Linen for History and Future
Textile production, and especially linen production, is full of knowledge and resources that could be better applied to sustainability and ethical production, and ultimately the human health of the people who make our clothing and household textiles.
As a consumer or creator, what can you do?
Buy and support linen made with ethical, transparent supply chains
Support small linen artisans to keep heritage skills alive
Care for your linen textiles so they last longer
Educate yourself about the fibers that are in your clothes and home
Live a simpler life with fewer but better things in your home and wardrobe
We hope that this guide has inspired you to wear linen with a sense of the history, the ecology, and the human touch and talent that have gone into making it possible for this remarkable fiber to be in your hands and on your skin.
XV. Optional Add-Ons
Online readers crave more than text. They want graphics, video, and takeaways. Sprinkling a longform article with complementary value-adds will keep your reader’s attention and increase comprehension, retention, and satisfaction.
Here are some optional features to add to your linen post:
A. Infographics Showing Process Stages
Infographics are a great option for turning complex concepts into visual explanations that reach visual learners and give detailed sequences, comparisons, or processes “at-a-glance” communication.
Here are some infographic topics you can use:
1. “ Flax to Fabric: Step-by-Step” Journey
Format:
Vertical timeline
Sections to include:
Flax Cultivation
(drawing of a flax plant with side root and top flower)
Harvesting
(pulling with tool/hand vs machine uprooting)
Retting
(photo of stalks in morning dew vs soaking tub)
Breaking and Scutching
(wooden blades vs industrial pressing)
Hackling
(comb-like smoothing tool)
Spinning
(hand wheel vs industrial yarn cone)
Weaving
(handloom beside a power loom)
Finishing
(washing machine, dye pots, softener vs simple water bath)
Grading
(photo of poor, medium, excellent fiber bales)
Packing and Distribution
(fabric rolls and transport trucks)
Visual elements:
Icons for tools
Arrows to show flow or sequence
Color coding
(e.g., blue for traditional, grey for industrial)
2. “Linen vs Other Natural Fibers” Comparison Chart
Format:
Side-by-side matrix
Fibers compared:
Linen, cotton, hemp, bamboo
Factors to compare:
Water usage
Pesticide needed
Biodegradability
Texture
Durability
Common uses
Purpose:
To demonstrate why linen outperforms other natural fabrics in sustainability, strength, and value.
3. “Artisanal vs Industrial Linen” Visual Breakdown
Format:
Split-screen, before-and-after illustration
Left side:
Flax field
Dew retting
Hand-spinning wheel
Wooden loom
Natural dye pot
Artisan signature or regional seal
Right side:
Combine harvester
Retting tank
Industrial spinner
Power loom
Synthetic dye barrel
Barcode label
Purpose:
To visually tell the story of the different process philosophy, aesthetics, and impact.
Embed these infographics as they appear in your article, or as a downloadable PDF or Pinterest-style pin to entice sharing.
B. Video Links to Flax Harvesting and Linen Weaving
Curated links to educational or documentary videos are another great way to bring your story to life. You can link to YouTube videos and embed them or just hyperlink to them within the appropriate section.
Here are some video categories and links for examples:
1. Flax Harvesting
Video Type:
Documentary or field footage
Suggested YouTube Search Terms:
“Flax harvesting by hand in Belgium”
“Modern flax farming machinery”
“Flax retting process demonstration”
Educational Highlight:
Demonstrates how flax is pulled from the ground, the timing, and the differences between traditional vs mechanical techniques.
Bonus Idea:
Add timestamps to important parts of long videos (e.g., “Harvest begins at 1:32”)
2. Linen Spinning and Weaving
Video Type:
Mill tour or artisan spotlight
Suggested YouTube Channels:
Linen Tales Lithuania
Masters of Linen
Irish Linen Guild
V&A Museum Textiles
Possible Titles to Embed:
“ From Flax to Fabric – How Linen is Made ”
“ Artisanal Weaving Process: Traditional Irish Loom ”
“ How Linen Yarn is Spun – Factory Tour ”
Educational Highlight:
Allows the viewer to visualize the whole process of flax being turned into thread and then woven into fabric, with focus on looms and finishing techniques.
3. Eco-Friendly Linen Production
Video Type:
Sustainability reports or brand features
Examples:
“How Linen Is a Sustainable Fabric”
“Linen:
The Eco-Fabric with Ancient Roots”
Interviews with European flax farmers
Purpose:
To add an extra dimension to your article’s environmental sections.
When embedding, be sure to add a short description and “takeaway” for the viewer like this:
🎥 Watch:
See how flax is dew retted in Lithuania in this 2-minute video
📝 Takeaway:
Dew retting takes longer but produces cleaner, stronger fibers
C. Q&A or FAQ Section
A FAQ can answer the last-minute questions many readers walk away with after reading a blog post, and can drive a lot of Google searches to your website.
This is because Google now automatically scrapes content to build its “People Also Ask” boxes (below is an example for “Linseed oil vs flaxseed oil”):
To format your FAQ:
Include common questions in your topic
Write out a solid answer to each, with links to your main content
Structure in a Q & A list, with bold questions as shown above
SEO Note:
FAQ and Q&A are interchangeable for SEO.
Example FAQ Section:
Extended Answers
1. What’s the Difference Between Flax and Linen?
Answer:
Flax refers to the plant (Linum usitatissimum) that’s cultivated for the oil in its seeds and the fibers from its stalks. Linen is the resulting fabric that’s woven from the fibers. This is like how cotton is the plant name, and cotton fabric is the textile name. Flax is also used for oil and food products, while the dried stalks are retted and spun into linen fabric.
2. Is Linen Always Organic?
Answer:
No, linen is not always organic, although it is naturally more eco-friendly than many other fabrics. Organic linen is specifically grown and processed without any synthetic pesticides, herbicides, GMOs, or synthetics, and under an inspected/regulated standard (like GOTS or EU equivalents). Regular linen can still be fairly sustainable, although looking for a certification is your best way to be sure of organic practices.
Some certifications to look for include:
GOTS (Global Organic Textile Standard)
OEKO-TEX®
European Flax®
3. Why is Linen So Expensive Compared to Cotton or Polyester?
Answer:
Linen costs more because:
The fibers are more labor-intensive to process
Flax takes longer to grow and must be harvested carefully
Much of the high-quality linen comes from Europe and farms with specific ethical standards
The yield per flax plant is also less than cotton plants
Values are added at each point in the production process (dew retting, hand weaving, etc.)
However, linen is also much longer-lasting, more breathable, and overall outperforms many cheaper textiles.
4. Can Linen Be Washed at Home?
Answer:
Yes—linen can typically be machine washed using cold or lukewarm water and gentle detergent.
Key care tips:
Avoid bleach and fabric softener
Use a gentle spin cycle
Hang dry or tumble dry on low
Iron while still damp if needed
Pre-washed linen or garment-washed linen is softer and less prone to shrinking, but always check the label.
5. What Are Tow Fibers in Linen?
Answer:
Tow refers to the shorter fibers that come from the flax plant as a byproduct of hackling and combing.
Tow is rougher and less lustrous than the long line flax, but can be useful for:
Blended fabrics that mix linen and other fibers
Coarser textiles like upholstery or sackcloth
Paper manufacturing and insulation
Tow-based linen is usually cheaper and more textured/rugged. Ideal for rustic or natural design.
6. How Can I Tell If My Linen is Good Quality?
Answer:
Look for:
A smooth, even weave with minimal holes
Fewer or intentional slubs in the yarn (unless it’s a design feature)
Transparency on the label (country of origin, certification, etc.)
Line flax instead of tow
Weight consistency (lightweight for clothing, heavier for upholstery)
Luxury linen often carries marks like Masters of Linen or Belgian Linen, or OEKO-TEX®.
7. What Makes Linen Sustainable?
Short answer:
Flax has a low water, pesticide, and fertilizer footprint
Grows in suboptimal climates/marginal soil types
Linen is biodegradable and recyclable
Longer-lasting than most other textiles (less textile waste)
Industrial processing can also counter these advantages, so look for low-impact, handwoven, artisan, or certified linen for a greener buy.
Extra Interactive Ideas
If you want to further round out the post and increase reader participation, here are some additional enrichment ideas:
1. Interactive Quiz Widget
“Is Linen Right for Your Lifestyle?”
Asking about their climate, wardrobe needs, and washing habits then provides a score and suggests different types of linen (e.g., casual wear, home linen, formalwear).
2. Downloadable Care Guide PDF
Create a printable 1-page care reference:
Washing temp
Ironing temp
Shrinkage precautions
Seasonal storage tips
3. Printable “Linen Lifecycle” Chart
Seed to finished garment—a great educational resource for schools or textile fans.
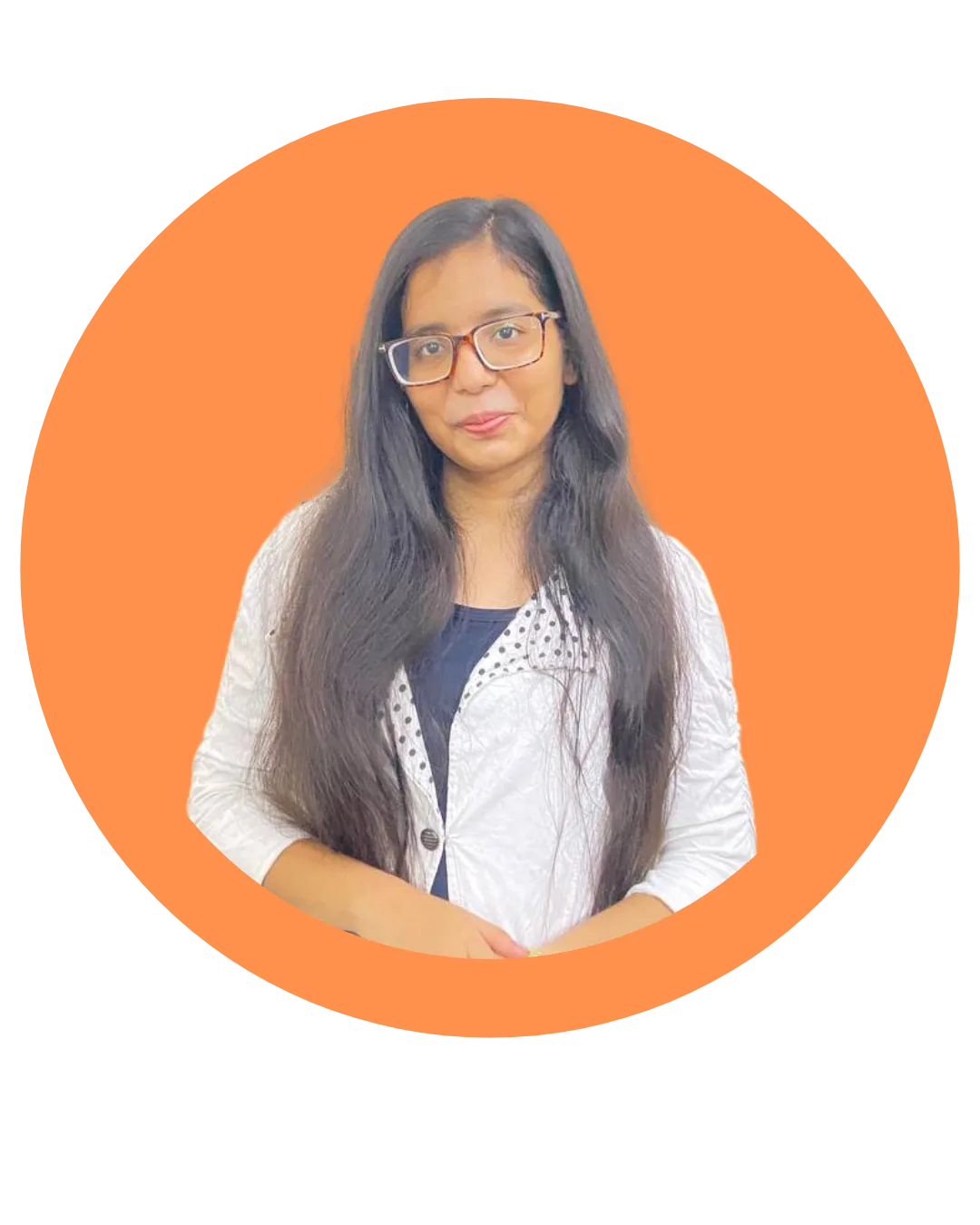
Yashvi Jain, a writer by day and reader by night, is an accomplished content writer and published author of ‘Mind Under Construction. Yashvi possesses extensive knowledge of fabrics, sustainability, and literature. On occasions, you would catch her scripting for her YouTube channel, engrossed in fiction, or ardently dedicating her time to research and storytelling.