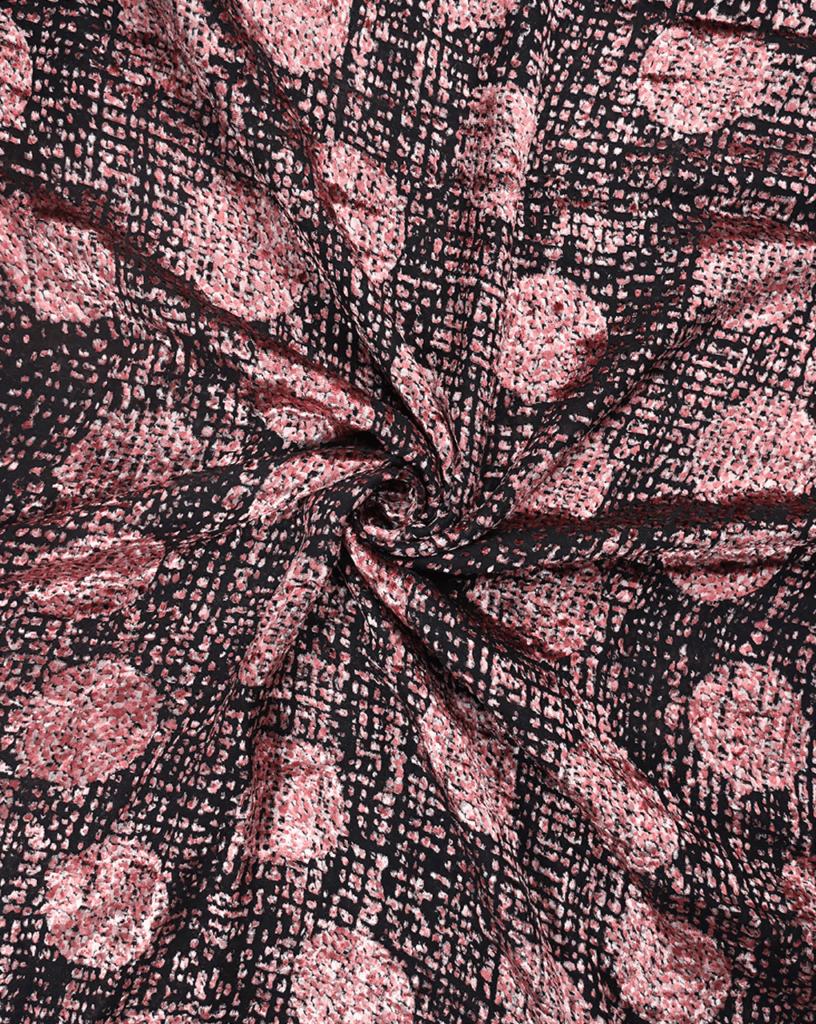
Polyester is one of the most common synthetic fibres in textile industry due to its flexibility, strength and affordability. You’ll see it in everything from clothing and furnishings to industrial processes. It is popular because it offers all of the desirable characteristics: high strength, wrinkle-resistant, cheap and easy to take care of. Polyester is used for apparel, upholstery or even industrial goods such as ropes and insulation.
Polyester is a huge industry, and millions of tons are made around the world each year. It is common in fabrics for shirts, dresses, sportswear and home textiles such as curtains, bedding and carpets. Additionally, its application in the automotive and electronic sector also shows that it has a broad utility.
Importance of Understanding the Process
Knowing how polyester fabric is made matters for a number of reasons. It provides, first, a peek into the making of a textile now part of everyday life. It also illuminates, for the second time, the environmental and sustainability issues associated with polyester production – an area of increasing interest in contemporary manufacturing. When the fashion and textile industries must be eco-friendly, knowing how polyester is made can ensure that consumers make better choices and choose sustainable alternatives.
Polyester fabric manufacturing also points towards the technological innovation and changes in textile manufacturing. All of these developments – from recycling and new dyeing technologies – help to propel the industry towards a more sustainable future.
Purpose of the Article
What this article is all about, is giving you an in-depth step by step description of the polyester fabric process, starting from the raw material to the final product. There are several stages of production, from the manufacturing of polyester resin, through fiber spinning, dyeing, weaving or knitting, and finishing the fabric. In-depth knowledge of these steps can help consumers to see the complexity of ordinary polyester goods and recognize the value of innovation and sustainability in textile production.
II. What is Polyester?
Definition of Polyester
Polyester is a synthetic polymer, or plastic, that’s used to make textiles. It’s manufactured from a chemical reaction between two raw materials, terephthalic acid (TPA) and ethylene glycol (EG), petrochemicals. These materials are polymerised to make long-chain molecules or polymers, which can be turned into fibres, films or other structures. And these polymers become threads or fibres when spun into the stuff we call polyester.
The polymer, which ends up as polyester polymer, or polyethylene terephthalate (PET), is an extremely versatile material. It’s chemical-resistant, long-lasting, and sanitary, so you can use it in every kind of application, from design to manufacturing.
Polyester’s Popularity
The textile use of polyester is widespread for a few reasons:
Solidness: Polyester fabrics are durable and do not swell, wrinkle or shrink. They are also stain-resistant, so even in the most frequent use, they won’t rust.
Cost-effectiveness: Polyester is low in price to manufacture, so the polyester is a very economical product for manufacturers. This low price is charged to the consumer so polyester is an affordable fabric.
Non-Poor Care: Polyester is low-porosity compared to natural fibres like cotton or wool. It doesn’t shrink when washing, it drys quickly, and it hardly ever needs ironing.
Polymorphism: Polyester can be woven or knitted into any texture and applied to any type of product. It can be woven with natural materials like cotton, wool or silk to have the best of both worlds (like the comfort of cotton with the sturdiness of polyester).
Basic Composition
Polyester consists of a polymer structure, usually made up of recurring units of terephthalic acid and ethylene glycol. Terephthalic acid is extracted from benzene, a petroleum product; ethylene glycol from ethylene, a gas extracted from petrochemical sources. It’s this polymerisation that results in polyethylene terephthalate (PET), the building block of polyester fibers. The very long molecular chains in PET ensure polyester is extremely strong, robust and environmentally resistant, the very reason that polyester is ubiquitous in textiles.
III. : The First Step: Polyester Resin Manufacturing
Petrochemical Derivatives
Polyester resin is first prepared for the polyester fabric. This is a process which starts with the crude from petroleum and two raw materials: terephthalic acid (TPA) and ethylene glycol (EG). They are both fossil-fuel based and used to make polyester polymer.
Terephthalic Acid (TPA): This is a crystalline solid, and it is the main building block of polyester. It is produced from pure terephthalic acid, and it’s oxidised.
Ethylene Glycol (EG): Ethylene glycol is a colourless, smellless petroleum-based liquid used as the second monomer in polyester production. It is used most often in antifreeze and solvent.
When these two chemicals are commingled in chemical reaction, they make a polymer that can be converted into fibres.
Polymerization Process
The polymerization reaction is the chemical reaction that bonds the molecules of terephthalic acid and ethylene glycol into a long chain polyester polymer. This usually has two phases – esterification and polycondensation.
Esterification: Terephthalic acid is heated and reacts with ethylene glycol to create a polyester intermediate called bis-hydroxyethyl terephthalate (BHET). The water leaks out of this reaction.
Polycondensation: BHET goes into further reaction (typically with more ethylene glycol) to make long polymers. It removes water molecules so that chains are attached to create a rigid dense substance called polyester resin or PET (polyethylene terephthalate). This resin is further converted into fibers, films, etc.
Formation of Polyester Chips
The polyester resin is cooled and ground into thin, solid pellets called “polyester chips” after it’s been polymerized. These chips are the feedstock for fibre production. The chips are usually transparent white and can be stored until they’re needed for further manufacturing.
IV. Step 1: Grinding the Polyester Fibers.
Extrusion Process
The polyester particles are hot-melted and run through a spinneret (a metal plate with a few holes in it). That is exactly the way spaghetti gets made — the melting polyester is pulled through these holes to produce long, continuous fibers. The diameter and number of holes in the spinneret dictate the thickness of the individual fibres.
The polyester melts and turns into a thick liquid in this extrusion process. It cools as it’s driven through the spinneret and hardens into filaments. It is the beginning of converting the raw polymer to the fiber for fabrics.
Cooling and Solidifying
The polyester fibres that are extruded then need to be cooled and hardened. It does so by cooling the fibers in a cooler, or by placing them in a swath of cold air. The cooling bonds the fibers, keeps them in place and makes them hard — from liquid to solid filaments.
Drawing and Stretching
They are pulled or stretched during manufacturing to make the fibres more dense and elastic. Drawing is simply a process of dragging the fibres on rollers, which stretch them and orient the polymer chains. This chemistry aligns the molecules in a way that gives the fibres greater strength and durability so that they can be used for textiles.
The fibres are stretched 3 to 6 times their original length, depending on the strength and elasticity of the fabric that is wanted. It’s the last step to producing polyester fibres for fabric making.
Texturizing
The polyester filaments are also sometimes textured to impart certain characteristics, like elasticity or texture. Texturising can be done by twisting or curling the fibres, which gives us fleece, terry cloth or stretch fabrics. The textiles that we usually find in sportswear or clothes with a little stretch or a little softness.
V. Step 2: Dyeing and Finishing.
Dyeing Polyester Fibers
After the polyester fibres are made, it is colored as per requirement. Dyeing polyester can be tricky because the fibers won’t absorb dye. But there are a few ways to dye polyester well:
High-Temperature Dyeing: Polyester yarn is heat-dyed, for example in a pressurized dye machine, to develop vibrant, lasting colors. The dye molecules can get inside the fibres in such a state.
Solution Dyeing: Solution dyeing is applied to liquid polyester resin before extrusion. This means the color gets evenly spread across the fiber and therefore colors uniformly.
Heat Setting
Polyester fibres usually go through a heat-set after being dyed. It’s when you heat up the fabric to retain the shape of the fibres and avoid them shrinking or stretching. Heat-setting holds the fabric in place so it won’t move or loosen during another washing or usage.
Finishing Techniques
Polyester fabric can be finished with different finishing procedures apart from dyeing and heat-setting to give it better performance. These treatments may include:
Comfy: Rub softeners on the cloth to make it softer and comfortable.
Moisture-Wicking: Chemical treatment to make fabric wick moisture from your body (most beneficial for activewear).
Anti-Wrinkle: Prepping the fabric with substances that resist wrinkling (especially important for garments that are less durable).
Chemicals used for Fire Prevention: Some polyester fabrics are coated with fire prevention chemicals to ensure they’re safe in industrial or public places.
Sustainability in Dyeing
There is more than just the dyeing process to make polyester a sustainable production process. Dyeing is also a water-intensive and polluting process, but new technology is coming to mitigate that. One of them is waterless dyeing, which doesn’t require large amounts of water when dyeing fabrics. The method will reduce water usage and wastewater generation in textile industry by a great deal.
Polyester Fabric Manufacturing: How It Is Manufactured.
VI. Step 3: Creating Fabric Out of Polyester – Weaving or Knitting Polyester.
Once the polyester fibres have been made and treated, they are prepared for the next stage of their life: being made into textile. Fabric production of polyester fibres includes weaving and knitting, the two common textile processing methods. Each of these treatments creates a different end fabric, which is suitable for different uses.
Weaving Process
One of the oldest and most primitive textile techniques is weaving. In it, two groups of yarns are joined at right angles to form a fabric. The warp (the vertical fibres) are gathered together on a loom and the weft (the horizontal fibres) are moved above and below the warp to create the cloth.
The main benefit of weaving is that it gives you textiles that are more robust and elastient than knit fabrics and are suitable for things such as dress shirts, trousers, upholstery, etc. Weaving is a win-win situation for polyester:
Twill and Satin Fabrics: Polyester yarns can be woven into many types of fabric including twill and satin. These wovens come in different textures:
Twill: Twill weaves with diagonally ribbed surface. This is because they are resilient, and you’ll find them in fabrics such as denim and gabardine.
Satin: Satin weave makes a smooth luster fabric reflect light. It’s most commonly used for dress fabrics, evening wear, and other designer fabrics.
Diversity of Weaves: Polyester can be stitched into other fabric materials such as plain weave, basket weave, or jacquard. These materials can be more or less resilient depending on the weaving pattern and some are better suited for heavy-duty uses (such as upholstery or outerwear) while others are used for lightweight fabrics.
Weaving is usually done on huge industrial looms, automated for efficiency. Each warp and weft yarn gets put perfectly into position on the loom, and the result is a fabric that’s even in texture and firm in form.
Knitting Process
There is a different kind of fabric-making process: knitting. Knitting doesn’t strand fibers perpendicularly, but knits together loops in a single piece of yarn to make a fabric. Knitting is done with both hands and machines, and in general it generates materials that are stretchier and more pliable than weaves.
In polyester production, knitting means placing polyester yarns in a knitting machine and knitting the yarns into loops. There are two main forms of knitting: 1) Cables.
Weft Knitting: When knitting weft, yarn is fed horizontally into the knitting machine and interlocks into loops. It creates jersey, ribbing, and fleece. Jersey, which is used for T-shirts and casual wear, is soft, elastic and breathable. We often find polyester jersey fabric in sports and activewear, because it is wicking and stretchy.
Warp Knitting: Warp knitting is done by introducing yarns into the knitting machine from above. It’s a process that builds a new structure, often for textiles such as tricot or mesh, which you typically find in underwear, athletic clothing, and sportswear. Another favourite polyester fabric, fleece, is knitted too – it makes a supple and warm fabric that is also lightweight.
Polyester knits are preferred for their durability, ease of wear and flexibility, which is great for activewear, underwear and other clothes that need to be comfortable and mobile.
Blending with Other Fibers
Polyester can also be combined with natural fibers such as cotton, wool or silk to produce fabrics that are equal parts cotton and wool. This is called blending, and it is often done in order to increase the fabric’s breathability, comfort or strength.
Polyester/Cotton Mixes: Polyester is sometimes mixed with cotton in order to add the natural breathability and softness of cotton to the strength and wrinkle resistance of polyester. This combination is very common in T-shirts, shirts, and wear casual.
Polyester-Wool Blends: Wool is another fibre mixed with polyester. Wool is comfortable and warm, but polyester improves durability, wrinkle resistance and washing efficiency — so you can use it in outerwear, sweaters and suits.
Polyester-Silk Blends: Polyester mixed with silk will cut the cost of virgin silk without losing the soft luxurious feel. It’s the combination you see commonly used in designer clothing and dress clothes.
Combine polyester with other fibers and you’ll get fabric with a more nuanced equilibrium of comfort, toughness, moisture-wicking, or shrinkage resistance.
VII. Step 4: Stitching the Polyester Fabric.
After polyester yarn has been spun or woven, it gets a set of finishing treatments for better feel, performance and look. It is the finishing step that imparts the final attributes to give the fabric the right qualities to be used in its end-use – be it clothing, furniture or construction.
Additional Treatments
Softener: Polyester textiles are sometimes softened to make them feel more comfortable. The fabric can be brushed with softeners (in a process called bio-polishing) to take out extra fibre and give it a more natural feel. This treatment is particularly good for polyester blends because the fabric remains soft on the skin.
Polyester Fabric With Water-Repellent Coatings: To increase the performance of the fabric — specially for outdoor/active wear use — polyester fabric can be coated with water-repellent coatings. Such treatments make water bubble and roll off the fabric’s surface so that it cannot soak up water. This is particularly useful for jackets, sportswear and outdoor wear.
Treatments for Flame Retardants: Polyester fabric is flame retardant, but it can be treated to make it less flammable. Such treatments appear in polyester fabric used in industrial textiles like workwear or protective clothing where flame resistance is a major factor.
Final Quality Control
Before polyester fabric can be declared ready for distribution, it is vetted. This includes checking the fabric for any flaws or imperfections that might affect the way it looks or operates. Key areas of inspection include:
Qualitiy of Dye: Double check uniformity of dye distribution and color fade.
Texture and Weave: Examine for blemishes in texture or weave or knit that could impair fabric durability or look.
Durability & Strength: Testing the fabric for strength and durability for the industrial applications where durability is critical.
When these checks are completed, the fabric is considered good to go: into packaging and distribution.
VIII. Step 5: Packaging and Distribution
After the polyester fabric has received all the treatment and quality assurances, it is distributed. This is the part of the manufacturing process where the fabric gets cut, rolled, packed and sent off to the manufacturers, wholesalers, and retailers worldwide.
Cutting and Rolling
Cutting and rolling: the enormous rolls of finished fabric are slit to smaller lengths as per the buyer’s need. It’s then folded onto massive bolts or spools that can be easily rolled and carried. These rolls are usually wrapped in a material to ensure they are not damaged during shipping.
Packaging for Shipment
We need to pack it well so that the polyester fabric arrives on its way in good shape. The fabric is packed well and shipped labeled; fabric type, color, specification printed on the labels. Packing can be based on end use and destination, some fabrics may need special handling or protection.
Global Distribution
Polyester fabric is globally available and its supply chain is huge. From fabric factories to garment factories, wholesalers and retailers, polyester cloth moves in a complex global supply chain. The cloth often travels continent-by-continent from Asian factories to North American, European and other retailers. The world supply chain is efficient and this has made polyester one of the most commonly used textiles on Earth.
IX. Innovations in Polyester Fabric Production
Polyester fabric is constantly being made with advances designed to reduce the environmental impact of manufacturing and increase the sustainability of the fabric.
Sustainability Efforts
Polyester manufacturing has always been condemned for using fossil fuels and producing huge amounts of carbon. But there are many new developments in polyester sustainability:
Recycled Polyester (rPET): Recycling post-consumer plastic bottles into a high-quality polyester material is done using recycled polyester (rPET). This reduces virgin polyester requirement, and keeps plastic waste out of the trashcan. rPET is becoming used in fashion and housewares for sustainability purposes.
Waterless Dyeing: Dyeing in the traditional manner takes a lot of water and it pollutes the environment. But waterless dyeing technologies have made a dent. Such processes dye polyester fabrics without water by using air or supercritical carbon dioxide, saving a lot of water and waste.
Bio-Based Polyester: A few companies are experimenting with bio-based polyester fibers made from renewable sources such as plant-based sugars. The technology may be quite powerful and will drastically lessen the use of petrochemicals in polyester making it a more eco-friendly fabric.
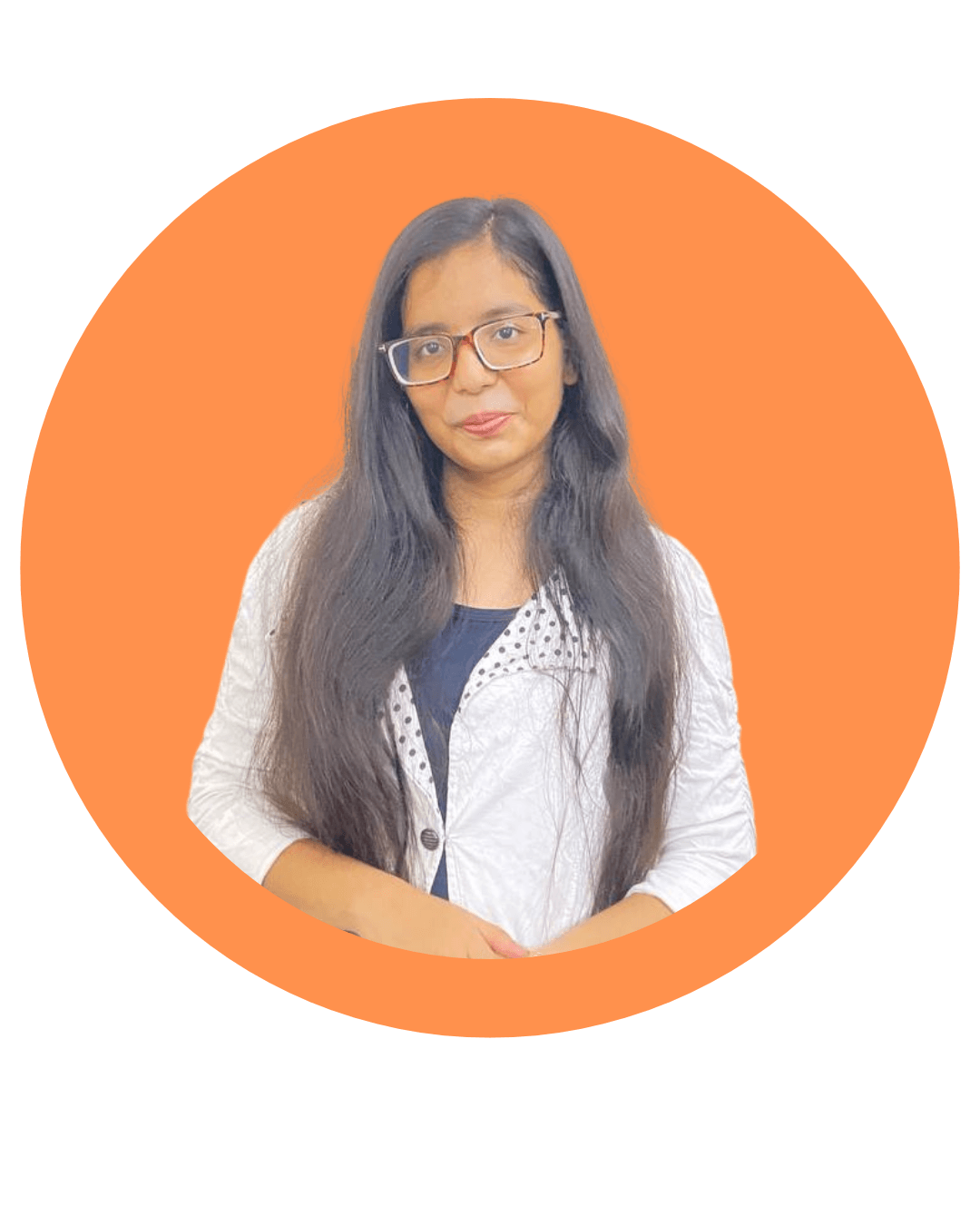
Yashvi Jain, a writer by day and reader by night, is an accomplished content writer and published author of ‘Mind Under Construction. Yashvi possesses extensive knowledge of fabrics, sustainability, and literature. On occasions, you would catch her scripting for her YouTube channel, engrossed in fiction, or ardently dedicating her time to research and storytelling.