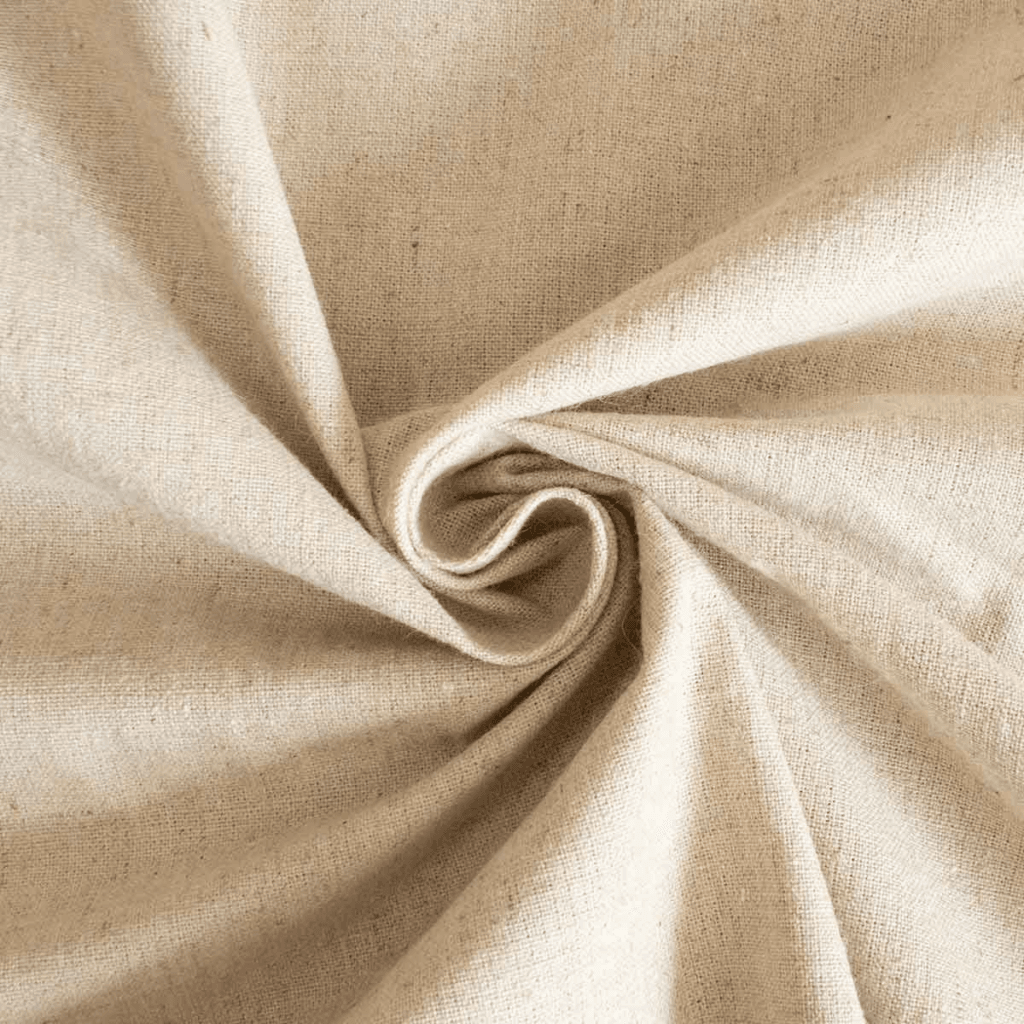
1. Introduction
Hemp fabric, which was used in textiles for centuries, is now taking centre stage in the contemporary world, especially in the sustainable fashion sector. In the face of ever more stringent demands by consumers for eco-friendly alternatives to synthetic and non-renewable materials, hemp fabrics are enjoying a renaissance. Hemp fabric has the reputation for its long life, durability and sustainability, and is not only versatile but also a promising solution to some of the toughest environmental problems faced by the textile sector.
Understanding how hemp cloth is made, from the hemp plant to the final fabric, is vital for consumers and industries wanting to move towards more sustainable solutions. The hemp fabric manufacturing process gives you a unique look at how one of the oldest, most versatile fibres can be transformed into a contemporary fabric that’s being made popular for its ecological credentials. In this article, I want to show an in-depth how-to process for the production of hemp fabric, starting from the seeds and ending up with textiles, demonstrating how sustainable and practical hemp can be in the modern apparel industry.
2. The Hemp Plant: A Universal Fiber.
Hemp, also called Cannabis sativa, is a tough and hardy herb. It’s the same species as marijuana, but dramatically different from the latter in its psychoactive effects, since hemp has extremely low levels of THC, the chemical that makes marijuana so psychoactive. Instead, hemp is grown primarily for its fibres, seeds and oils, used for millennia to produce textiles, paper, ropes and other items.
What is the Hemp Plant and What Does it Do?
Hemp is an annual that matures in about three or four months depending on where it grows. It has tall, fleshy stalks, narrow, erect leaves and a hefty bloom. Hemp is dioecious, which means it grows two plants (male and female). The male plant is usually harvested for fiber, while the females are prized for their seeds and oil.
The fibre derived from the stems of hemp is long, fibrous and robust, making it ideal for textile use. The plant’s stems are laden with both bast fibres (in the inner part of the stem) and hurd (core), a soft, woody material used in various industrial applications. The strength and durability of hemp stems from its long fibres, which can be processed into everything from textiles to biodegradable plastics.
Also Read : The History of Hemp Fabric
How Hemp is Different from Other Fiber Plants.
Hemp is regarded in much the same way as other fiber-producing crops like cotton and flax, but has very different growing, processing and environmental practices.
Hemp vs. Cotton:
Cotton is one of the most widely used natural fibres in clothing. But it takes a great deal of water and pesticides to grow, and it’s a carbon-intensive crop. Hemp, by contrast, needs far less water and pesticides, and is far more sustainable. In addition, cotton cultivation drains soil nutrients slowly, whereas hemp has the benefit of increasing soil health because its deep rooting system prevents erosion and allows for nutrient cycling.
Hemp vs. Flax:
The fibre that produces linen comes from flax, and like hemp, it yields fibres that are hard. Yet, hemp is considered more resilient and adaptable than flax. Unlike flax, which is normally a fine fabric and known for its softness, hemp fibers are initially hard, then become smooth as you use them. Hemp also has a higher acreage yield than flax and is thus less expensive to grow in bulk. Hemp’s fiber is stronger, more resilient, and less prone to tearing, making it ideal for high-density uses such as ropes, sails, and even long-lasting clothing.
Hemp’s Use for Fibres in Ancient CivilisationsHistorical Perspective: The Use of Hemp For Fibers In Ancient Civilisations
Hemp textiles were in use for millennia. Hemp is among the earliest fibre-producing plants, with ancient China showing its widespread use around 8,000 BCE. In prehistory, hemp was used to make ropes, sails, clothing and paper. Indeed, China made the first paper from hemp fibres, and old textiles would have been woven with hemp or flax fibres, given their affordability and durability.
The cultural value of hemp extended beyond this sphere: references to its use appeared in Egypt, Mesopotamia and Greece. For sailors in Europe, hemp remained a staple material: hemp ropes and sails were used to keep their ships afloat. In the medieval world, hemp remained a useful crop, and its use in clothing and tapestries was widespread.
In the Americas, early Europeans farmed hemp for textiles and paper, and hemp was a vital industrial crop in colonial societies. This long history of hemp production was the beginning of hemp’s contemporary revival as a sustainable and environmentally friendly product.
3. Cultivation of Hemp
This is one of the reasons why hemp is a sustainable and environmentally-friendly textile material. Hemp, unlike many other fibre crops, can be grown sustainably, which makes it a popular choice for those who are conscious of their carbon footprint.
Ideal Growing Conditions for Hemp
Hemp is tolerant of many climates but grows best in temperate, moist conditions. It prefers a well-drained, deep soil, ranging in pH from 6 to 7. Hemp is an intolerant to most pests and diseases, which doesn’t require pesticides or chemical fertilisers. This not only makes hemp farming greener but also less harmful to the surrounding ecosystems.
The ebb and flow of hemp’s 3-4 month growth cycle allows farmers to harvest hemp several times a year. Its short growing time also means that hemp can be planted almost anywhere, giving farmers all over the world a viable alternative.
Hemp requires little water over the course of its development, but it needs less water to grow than other water-intensive crops such as cotton. This water efficiency is a huge advantage, especially in areas where water scarcity is on the rise. Hemp also grows well in poor soils, so it is a good crop to plant on land that might not be suitable for other crops.
Hemp Farming Process
Planting Seeds:
A hemp crop begins with seeds which are generally planted early in the spring after the soil is warm. Hemp is dioecious — that is, the plant has two species, one male and one female. Both the male and female plants make pollen, and the females make seeds. A farmer would grow hemp to harvest fiber from male plants, which have longer fibres and longer stems. Female plants are typically cultivated for seeds because they have oily seeds.
Growth Cycle:
Hemp plants grow rapidly, and generally take 3 to 4 months to mature. The shrub is tall and robust, with narrow leaves and thick flower heads on its stems. Hemp grows tall, with some species reaching 12 to 15 ft in height. At different stages of the growth cycle, hemp’s roots deepen the soil and reduce erosion.
Harvesting the Plant:
Hemp is harvested when the plant is at full ripeness, and the fibers are fibrous and firm. The harvest time plays an important role, ensuring that the fibers are the best quality. The stalks are slashed either manually or with harvesters, and the shoots are temporarily allowed to dry out in the field.
Benefits of Hemp Farming
We Need Very Little Pesticides And Fertilizers:
Hemp is a naturally resistant plant, and thus it needs little to no pesticides and fertilisers, making it a sustainable crop. In contrast to cotton, which has traditionally required vast amounts of chemical inputs, hemp can be grown with very few or no synthetic chemicals, without damaging surrounding ecosystems or the health of the soil.
Low Water Consumption:
Hemp is also very efficient when it comes to water use. Hemp also uses far less water than cotton, one of the most water-hungry crops on the planet. This is what makes hemp attractive to farmers in places where water supplies are scarce.
Soil Health Improvement:
The thick roots of hemp support soil health by mitigating erosion and improving nutrient cycling. Hemp can also pull and store carbon from the ground, helping to reduce global warming.
Hemp’s low environmental footprint, low chemical dependence, and short life cycle make it a perfect crop for biodynamic farming. The advantages of hemp cultivation go beyond textiles, since hemp is grown for food, oil and medicine.
4. Harvesting and Retting Process
Harvesting and retting are key elements of the manufacture of high-quality hemp textiles. These processes influence the integrity of the fibers and therefore affect the strength, surface texture and quality of the final textile. It is essential to know the best harvest times and retting techniques in hemp processing to ensure that you are making fabric that can satisfy modern buyers.
Harvesting At Right Moments For Good Fiber Quality
Hemp is usually harvested when the plant has grown fully, which generally takes between 3 and 4 months after planting. When hemp should be harvested depends on the use for which the plant will be harvested – for fiber, seed or oil. When fiber production occurs, the plant is taken off at a particular time when the bast fibres are at their best strength.
It’s crucial that the harvest is scheduled right, so the fibers are at their best. Hemp can also produce too short, weak, and brittle fibers if harvested too early. Conversely, if it is not harvested early enough, its fibres become too fragile and rigid, making them hard to digest. Hemp plants harvested for fibre are typically felled when the stalks have matured, and the outer fibers are ready to be cut from the woody core. By now, the hemp plant has gone from vegetative to flowering, and its fibers are at their heaviest.
To get the best yields, you must harvest the hemp before the flowering phase is over, because that is when the plant starts investing its energy in seed production. Further, the plant’s stem must be fibrous when picked, and the long fibres must be strong and suitable for textile purposes.
Methods of Retting
Once the hemp is picked, it goes through the retting process. The term retting is used to refer to cutting the fibre off the plant’s woody huld. It means breaking down the pectins that connect the fibers to the rest of the plant so the fibers are more easily separated.
Retting hemp comes in a number of forms, each of which is more or less the same. Water retting, dew retting, and mechanical retting are the most common.
Water Retting
One of the oldest and most traditional methods of hemp processing is water retting. In this process, harvested hemp stalks are placed under water, usually in ponds or slow-flowing streams, to disperse the pectins and separate the fibres. Water retting can take days to weeks, depending on temperature and the hemp condition. In doing so, bacteria eat away at the cellular material surrounding the fibres.
Water retting makes fine, high-quality fibers that have a silky texture, which are perfect for fabrics such as hemp fabric. Yet this approach is quite water intensive and can produce releases of contaminants into the environment when done improperly. Thus, water retting isn’t the best alternative for the environment, unless controlled.
Dew Retting
Dew retting, a more natural practice, involves leaving hemp stalks lying in the field after they have been harvested to absorb moisture, either dew or rain. During a few weeks, nature’s humidity dissolves the pectins that hold the fibers together. Dew retting is less labour intensive than water retting, and needs less water, making it more environmentally friendly.
One of the main advantages of dew retting is its environmental sustainability. Yet dew retting is highly weather-dependent. When the environment is dry or wet, this may interfere with the retting. Quality of fibers might also depend on the period of time spent on the plant – long-term dew exposure can cause fibers to become less durable.
Mechanical Retting
Mechanical retting is a relatively recent form of retting, in which the plant material is disintegrated and the fibres are cut apart by machines. It involves shredding hemp stalks by hand, separating the fibres from the woody core using rollers, presses and mechanical combing. Water and dew retting is less time-consuming, but mechanical retting can be done in hours instead of days or weeks.
Mechanical retting is more efficient but tends to yield raggeder fibres than either water or dew retting. The mechanical action can also degrade some of the fibres, especially if the equipment isn’t specifically calibrated. Yet mechanical retting is becoming increasingly fine-tuned by technology to be a viable technology for mass-production.
What Is The Purpose Of Retting For Fiber Extraction?
Retting serves the chief purpose of separating the bast fibres from the woody root of the hemp plant. When the fibres are retted, the pectins and other components that attach to the woody core dissolve, and the fibers fall apart. After retting, the hemp stalks can be processed further to separate out the remaining non-fibrous material, while retaining the long, strong, and robust fibres used to make hemp fabric.
Retting also makes the hemp fibers softer, making them malleable for spinning into yarn. What fibers we receive in retting can affect the final quality of the fabric and its resistance.
5. Decortication: The Fiber Extraction Process
Decortication is the next critical step in hemp fabric manufacturing. It is the extraction of the hemp fibers from the woody core (the “hurd”). Decortication is the process used to harvest the long, hard fibers needed for heavy textiles and other hemp products.
Describe the Effect of Decortication and the Process by Which It Separates the Fibers from the Woody Core.
Decortication means mechanically breaking the outer hull of the hemp stalk in order to extract the valuable bast fibres from the inside of the hurd. The bast fibers, the fibres running the length of the hemp plant, are the main fibers used in weaving. The woody core is composed of shorter fibres, which aren’t typically used for textiles, but can be processed to make biodegradable plastics, bedding, and even construction products.
- HAND-WOVEN HEMP ROPE: The hemp rope color of this pampas vase matches the pampas reed, which is warm, charming, and sets…
- ROOM DECOR AESTHETIC: Suitable for Bohemian style, modern farmhouse style and country style. Suitable for home decor, li…
- CREATIVE USE: As a storage bottle, it can store sand, shells and other interesting small objects. As a holiday dress-up …

- Less-dusty alternative to other bedding types
- Sustainably sourced, grown without pesticides
- Superior odor, ammonia, and moisture control

Decortication is a mechanical process by which the fibres are isolated from the rest of the plant. They begin by slicing the hemp stalk in to pieces and then stripping the fibres out with mechanical equipment. This apparatus includes decorticators – the machines used to remove the fibres from the stalk.
Instruments and Machines for Decortication.
Traditional decortication involved chopping and sifting the fibres by hand with hammers or wooden mallets. This laborious activity eventually gave way to machines capable of consuming large volumes of hemp more quickly.
Modern decorticators work the stalks down using rollers, combs and mechanical presses to pull out the bast fibres from the hurd. Some decorticators resort to what’s known as “ball milling,” where the hemp stalks are fed through rotating barrels or drums that push the fibres out from the woody core.
Newer, better machines enable the fibers to be removed more thoroughly and effectively, so that the fibres are of a higher quality and free from contaminants. Modern decorticators also ensure that the fibres are cut to the correct length and quality to create durable hemp fabrics.
What’s The Difference Between Old and New Decortication Methods?
The major difference between ancient and contemporary decortication was the scale, velocity and accuracy of its execution. Old-fashioned methods were slow and labour-intensive, and it took a lot of human energy to harvest the fibres. The fibres they produced were usually not quite as symmetrical in character and texture.
By contrast, modern decortication processes are very mechanised and automated, which means that enormous amounts of hemp can be processed faster. These are also more efficient systems – yielding better fibres with less waste. Furthermore, modern decorticators reduce the amount of damage to the fibres when they are processed so as to retain their durability and quality.
6. Turning Hemp Fiber into Yarn.
After the hemp fibers are decorticated, it’s time to spin them into yarn. Spinning involves weaving the individual fibers together to produce a long, continuous piece of yarn or thread. The yarn quality and stiffness are important in determining the final properties of the hemp fabric — its toughness, feel, and appearance.
Carding and Spinning Hemp Fibers.
Carding is the initial step of spinning. It involves spinning the hemp fibers through combs and rollers to unpick, cut and displace them into a homogeneous lump. This will allow you to get the fibers ready for spinning, making sure they are evenly distributed and free of clumps or knots.
Once carded, the fibers are spun into yarn. In the spinning stage, fibers are twisted into a ball by a wheel or a mechanical spinner. The twist used in spinning determines the final texture of the yarn. A higher twist produces a thinner and denser yarn; a lower twist creates a looser and lighter yarn.
How Spinning Creates Yarn from Short, Separated Fibers?
The spinning process takes short, individual fibres and twists them into long fibers. Twisted together, the fibres get stronger and tangle together, creating a yarn that goes on and on. This twisting also produces the yarn’s textured surface, which can range from soft and fine to rough and heavy, depending on what the fabric will be used for.
The fibrousness of hemp makes spinning hemp yarn a bit more difficult than spinning cotton or artificial fibres. Hemp fibers are longer and coarser than silk, and therefore more difficult to spin into a fine yarn. But with the modern spinning machinery, fine hemp yarns are made that are soft, durable and suitable for a range of textile uses.
Modern Versus Traditional Spinning Methods
Some spinners, mainly small-scale producers, continue to use traditional spinning, such as spinning by hand with a wheel. But the majority of contemporary hemp fabric manufacturing is done using industrial spinning machines capable of spinning out masses of fibre quickly and efficiently. These machines, based on modern technology, control the speed, tension and twist of the yarn to ensure consistency and quality.
Using contemporary spinning techniques, it is also possible to spin thinner, softer yarns. Others blend hemp fibers with other fibres, like organic cotton or recycled polyester, to create a silky feel and improve the yarn’s capability in textile making.
Yarn Density and Structure Involved in Fabric.
The bulk and feel of the yarn affects the quality of the end hemp cloth. Better yarns produce more resilient fabrics and are resistant to wear and tear. Hemp fibers are extremely durable, and hemp yarn becomes softer as you use it, so that they are comfortable to wear.
This texture also impacts how the yarn looks and feels. Hemp textiles range from rough and rustic to soft and smooth, depending on how the yarn is spun. The yarn weave will determine how the cloth drapes, perspires and touches the skin.
7. Sewing and Fabricating the Hemp Yarn Into Fabric.
So once hemp yarn is spun, it needs to be weaved or knitted in order to make it useful material. This production process is where the stiffness, elasticity, and final appearance of the fabric come into being. The two most common methods of weaving and knitting yarn into cloth are weaving and knitting, both of which have significant influence on the flexibility, durability and sturdiness of the fabric.
What’s the Difference Between Weaving and Knitting Hemp Yarn?
Knitting and weaving are two different processes that make fabric in a different way. In both processes, the yarn is stitched together to form a continuous piece of fabric, but the way that the yarns are stitched varies enormously.
Weaving consists of weaving two pairs of yarns opposite to each other, one horizontally (the weft) and the other vertically (the warp). This treatment results in an extremely rigid construction, and is most commonly employed for fabrics that require a tight, durable finish. Weaving is the preferred technique for producing hemp fabrics because it maintains the natural strength and resilience of hemp yarn.
Knitting, by contrast, is knitting the loops of yarn together with needles to create a stretchy material. Knitted fabrics tend to be softer and more flexible than woven fabrics, and can be used for clothing with greater elasticity, like t-shirts or athletic clothing. Knitting results in a fabric that moves either one way or the other depending on the knit you use.
In the case of hemp yarn, you can weave or knit it, based on fabric qualities you want. Hemp yarn is generally coarser than cotton yarn, so weaving results in a tougher, more durable cloth, while knitting leads to a soft, more elastic cloth.
Simple Hemp Fabric Weaving Instructions.
Hemp fabric is primarily weaved, and there are several common techniques of woven fabric that impart different types of textile qualities. Plain weave, twill and satin are the most widely used weaving techniques, and each gives a distinctive feel and wear.
Plain Weave
Plain weave is the basic and most widely used weaving process for hemp fabric. Using this technique, the weft yarn is stitched over and under the warp yarn in a regular, alternating pattern. This produces a flat, narrow, and robust fabric with a well-balanced look. Plain weaves are relatively stiff, unlike other weaves, and are ideal for applications requiring a high volume of wear such as bags, upholstery, and industrial textiles.
Plain weave hemp fabric is a little rough, but becomes smoother as it gets washed and used again and again. Plain weave also means that hemp is inherently strong and durable and will not become brittle.
Twill Weave
Another popular hemp fabric weaving technique is the twill weave. In this technique, the weft yarn slips over and under two or more warp yarns on regular intervals, leaving a diagonal line on the fabric. This produces a fabric that is less stiff and brittle than standard weave hemp cloth, but still strong.
Twill weaves are commonly used to produce textiles that have a shiny surface. It is widely used in jeans, jackets, and skirts, because the twill’s diagonal texture allows for a smooth drape while keeping the fabric firm.
Satin Weave
Satin weave, an advanced method of weaving, produces a high-gloss finish fabric. In this technique, the weft thread stretches across several warp yarns and then down under one, leaving a satiny surface. Satin-weave hemp fabric is shiny and velvety, which makes it ideal for more upscale products, like couture clothes or interior decor.
Satin weave hemp fabric may be soft and shiny, unlike plain or twill weave fabrics, but it’s usually softer and susceptible to wear. The soft surface is more vulnerable to scratching or pulling, and so it is generally found in gentler landscapes than other hemp fabrics.
The Use of Looms and Knitting Machines for Textile Processing.
Weaving and knitting techniques employ both looms and knitting machines. These machines regulate the direction and amount of tension in the yarns so that the fabric has the same weight, surface texture and durability.
Looms are giant mechanical machines that spin yarn into cloth. They are made of different kinds, such as handlooms and power looms. The handloom is primarily employed for small-scale, manual weaving; the powerloom is employed in large-scale manufacturing to weave large-scale batches of fabric.
The power looms come with sophisticated technology that speeds up and produces more efficient weaving. These machines can weave a wide variety of fabrics, from thin cotton to thick hemp, in weaves such as plain weave, twill and satin. The loom manipulates the motion of the warp yarns while the weft thread is passed through the shed (the gap between the warp yarns) to produce the cloth.
By contrast, knitting machines knit yarns into garments by joining loops of yarn. Such machines insert needles in the yarn to pull it through previous loops, giving knitted fabrics their characteristic pattern. Modern knitting machines can weave flat or tubular knitted fabrics, depending on what is being woven.
Knitting machines are employed to create fabric that requires stretch and elasticity, like activewear, t-shirts and sweaters. Although hemp is commonly spun into cloth, knitted hemp blends are now appearing in some apparel lines.
Fabric Types Created (Formatted Hemp Fabric, Hemp Mixes)
It all depends on how the hemp yarn is woven or knitted, as well as on whether or not it has been treated or mixed with other fibres. The most used types of hemp fabric are regular hemp fabric, hemp blends, and performance fabrics.
Plain Hemp Fabric
Pure Hemp Fabric (Plain weave)- It is the strongest and most useful type of hemp fabric. It’s perfect for applications requiring strength and durability, including upholstery, bags, and workwear. The cloth is relatively rigid and coarse when first woven, but it stretches and washes softly.
Hemp fabric is also often combined with other natural fibres like organic cotton or linen, to create fabrics that combine the advantages of each. Hemp-cotton blends, for instance, are gaining favour in the fashion industry because they can marry hemp’s durability with the feel of cotton.
Hemp Blends
Hemp blends mix hemp fibers with other materials like cotton, silk or polyester to deliver certain performance attributes. For instance, a hemp-cotton blend could yield a fabric that had the wicking properties of cotton but the added strength and sustainability of hemp. In the same way, hemp-silk blends meld the softness of silk with the durability and sustainability of hemp.
Hemp blends are very common in fashion and upholstery textiles because they provide the properties of hemp fabric without overcoming the texture or softness drawbacks of natural hemp fabrics. They are blended with synthetic fibers like polyester or nylon to enhance the elasticity and flexibility of hemp textiles.
- Lark Books-Hemp Macrame
- Kick off summer fashionably with these twenty beachy hemp creations! Using nature’s loveliest bounty, like shiny sea gla…
- Fashion a knotted sea glass bracelet, shell cluster necklace, tassel and bead earrings and more
- Design Originals-Friendship Bracelets All Grown Up

8. Post-Production Treatments
Hemp fabrics are usually subsequently treated at various stages after they have been woven or knitted to enhance its texture, colour and convenience. Such treatments provide a vital function in improving the final look and feel of the fabric and also ensure that the fabric conforms to certain performance criteria.
Chemicals to Smooth and Finish the Fabric.
Hemp fabric is renowned for its durability, but when first made, hemp can be coarse and stiff. It is softened by a number of processes in order to make the fabric more comfortable and functional.
Enzyme Washing
The most popular method to soften hemp fabric is enzyme washing. This involves spraying the fabric with enzymes to break down the lignin and cellulose that forms fibers, which softens and reduces stiffness. Enzyme washing also smooths and polishes hemp fabric by washing off any residual impurities or roughness.
Enzyme washing is environmentally friendly as it does not use as many chemicals or water as conventional treatments such as stone washing or bleaching. It also retains the fabric’s natural properties and prevents wasteful aging.
Bleaching and Dyeing Methods
Colouring and dyeing are the two main processes that change the look and appearance of hemp fabrics. Hemp fibers, though naturally beige or light brown, can be bleached to white or off-white fabric, or dyed to various shades of grey.
Hemp can also be dyed using a variety of natural and artificial dyes. The porous surface of the fabric absorbs dyes in a uniform manner, producing vivid, long-lasting hues. Hemp holds dye very well, making it the ideal fabric for producing textiles with dark shades.
Softening for Comfort and Usability
Apart from enzyme washing, hemp textiles may also be softened using silicone softening or mechanical softening. The silicone softening process involves spraying a silicone solution on the fabric and making the fabric feel soft without loosing the durability of the fabric. Brushing or sanding mechanically softens the fabric physically, which smooths it out to increase its softness.
These softening chemicals make hemp textiles more suitable for wear in everyday situations, giving them more comfort and wearability without diminishing the elasticity or sustainability of the material.
How Finishing Enhances the Quality of the Final Fabric.
What happens to hemp fabric after it is treated for the production process, makes the fabric meet its own quality, comfort, and useability requirements. These finishing processes soften, colour, and enhance the performance of the fabric to create a piece that is not only useful but also attractive and wearable.
Finishing can also increase the fabric’s resilience to wear, tear, and fade. This makes hemp cloth a lasting and environmentally friendly alternative to conventional textiles.
9. How Hemp Fabric Production Affects the Environment?
Hemp fabric production is typically considered to be less harmful to the environment than other fabrics such as cotton and polyester. Hemp is a renewable fibre that uses less to produce and process than most fibers, making it an appealing choice for eco-conscious consumers.
Environment Impact of Hemp Production Over Other Fabrics.
Hemp has a much smaller ecological footprint than cotton. Hemp requires far less water and pesticides than cotton, and it germinates quicker, making it a more sustainable crop. In contrast, cotton cultivation is well-known for its water intensive practices and reliance on chemical pesticides that can be detrimental to natural and regional ecosystems.
Hemp has an innate biodegradability advantage over synthetic fibers such as polyester. Polyester and other synthetic fibres are made from petrochemical components that release microplastic pollutants during washing. In contrast, hemp is utterly biodegradable, disintegrating naturally over time without adding any pollutants to the environment.
Production of Hemp Fabric: Energy and Water Consumption.
Hemp cultivation uses comparatively less water than cotton, one of the world’s most water-consuming crops. The early retting and processing phases of hemp production can still be water intensive, but in the long run, hemp production uses much less water.
Hemp fabric manufacturing also uses less energy than manufacture of synthetic fabrics such as polyester, which require a significant energy input to produce polymers. Hemp production, especially in an environmentally friendly way, uses far less energy and has a much lower carbon footprint.
The Biodegradable Properties of Hemp and Its Use in Green Fashion.
Hemp fabric has the advantage of being biodegradable. In contrast to artificial fabrics, which can take hundreds of years to decompose, hemp fabric breaks down organically with no toxic imprint left behind. This makes hemp a perfect candidate for sustainable fashion, because hemp keeps waste out of landfills and has a lower environmental footprint when it comes to the manufacture of clothes.
In a world where consumers are shifting to sustainable alternatives, hemp fabric is increasingly being used in sustainable fashion. The fabric’s low environmental footprint and its strength, comfort and versatility make hemp a promising future substitute for both natural and artificial textiles.
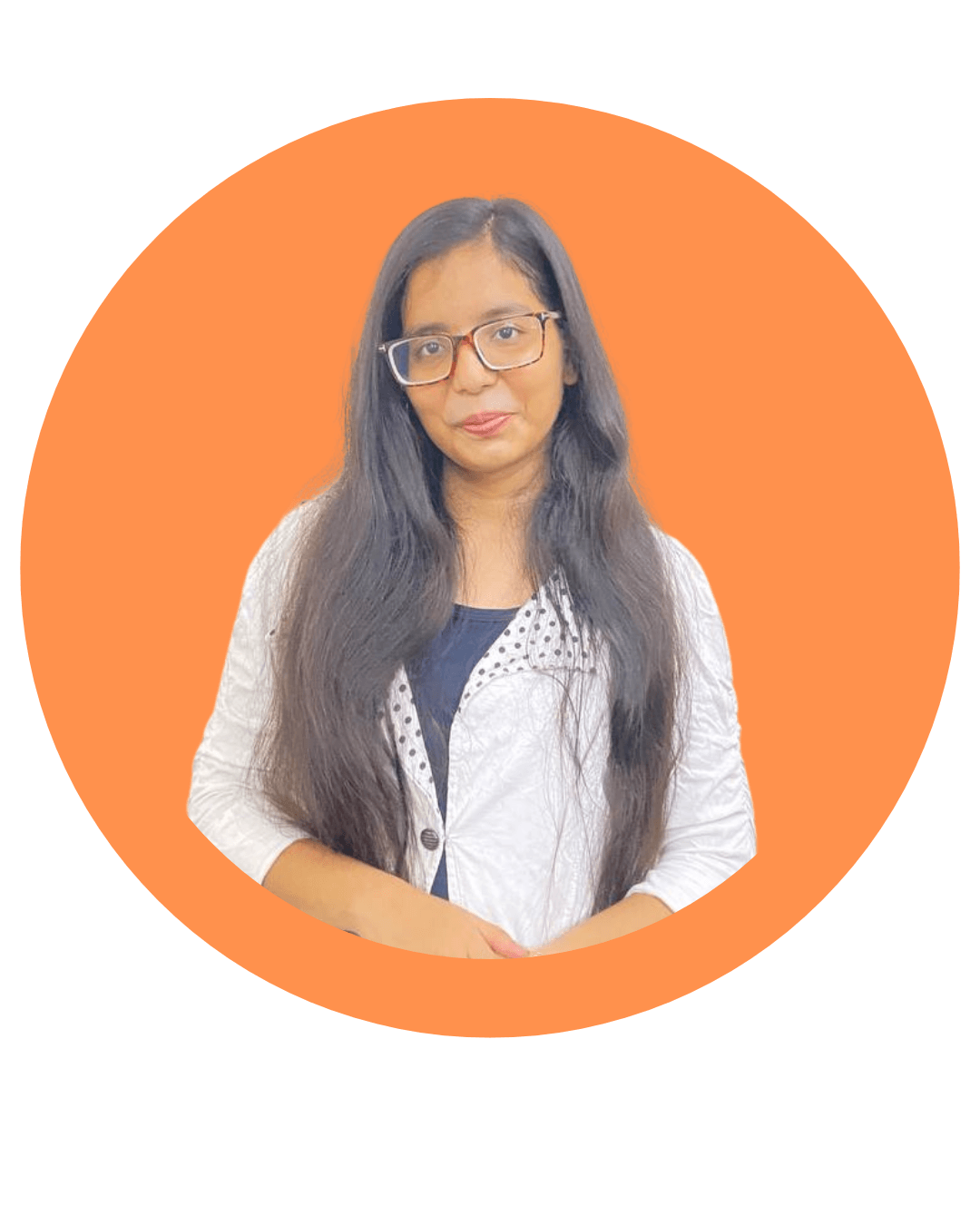
Yashvi Jain, a writer by day and reader by night, is an accomplished content writer and published author of ‘Mind Under Construction. Yashvi possesses extensive knowledge of fabrics, sustainability, and literature. On occasions, you would catch her scripting for her YouTube channel, engrossed in fiction, or ardently dedicating her time to research and storytelling.