Introduction
In its modern application of design and engineering to automobiles, nylon has long since moved beyond its textile roots. Although we often think of nylon as used in car seats, belts and the like, its use goes beyond textiles. Due to its versatility, strength and adaptability, nylon is essential for manufacturing lightweight, tough and fuel-efficient cars.
The automobile sector has embraced nylon because of its performance, weight reduction, and environmental efficiencies. From functional components in fuel lines to structural components in hybrids and electric cars, nylon has become a key part of automotive innovation.
This article covers the exciting history of nylon in the automotive industry and the role it played in the creation of cars, as well as their functions and how it changed the face of vehicle production.
1. Nylon in Automotive: The Growth of Nylon in Automobiles.
Historical Context
Nylon became a component of automobiles around the mid-20th century, primarily for textile applications such as seat belts, upholstery and carpets. Nylon was coveted for its strength, durability and resiliency. By the time cars were more sophisticated, nylon’s possibilities for non-textile uses had begun to take hold.
Technological Progress
During the past several decades, advances in material science have revealed nylon’s capability as an advanced engineering plastic. Automobile makers even started looking at its use in under-hood and chassis parts:
- Heat Resistant: Developments in heat-resistant nylon made it possible to substitute it for metals in high temperature engine parts.
- Chemical Resistancy: The resistance to oils, fuels, and other chemicals made nylon the perfect material for fluid handling applications.
- Reinforced Nylon: Fillers such as glass or carbon fibers have increased the strength and stiffness of nylon, which makes it suitable for high mechanical demands.
Current Status
Nylon today abounds in the automotive industry and appears both in the interior and exterior of vehicles. It is used from functional applications like fuel lines and switches, to decorative applications like trims and hoods. New developments such as electric and hybrid vehicles further increased the applications of nylon, with manufacturers looking for lightweight and sustainable solutions to enhance energy efficiency.
2. Nylon in Functional Automotive Components
Engineered Plastics
For engines and mechanical parts that require high performance, nylon has been the preferred material: it’s extremely flexible.
Applications:
- Intake Manifolds: Nylon has taken over metal in most intake manifolds because it’s light weight, simple to produce, and can endure extreme temperatures and pressures.
- Oil Pans: Nylon oil pans are light and durable — they absorb impacts to improve fuel mileage.
- Radiator End Tanks: Because nylon resists heat and corrosion, it is a great choice for radiator assemblies that can maintain their performance throughout a vehicle’s life.
Benefits:
- Lightweight: Nylon parts make a vehicle lighter than conventional metal parts for greater fuel economy.
- High Performance nylon grades have the heat resistance of up to 200°C (392°F) which makes them ideal for use under the hood.
- Chemical Resilience: Nylon’s abrasion resistance to oils, fuels, and coolants ensures long-term durability.
Electrical Systems
Polyester is also used in automobile electrical components where long life and insulation are essential:
Applications:
- Wiring Harnesses: Nylon wraps and seals wiring harnesses, providing flexibility and insulation.
- Plugs & Clips: Nylon plugs are strong, light, and environmental resistant, giving you reliable electrical wiring.
- Cable Ties: Polyester cable ties are commonly used to store wiring in cars.
Advantages:
- Electrical Insulation: Nylon’s excellent dielectric strength prevents electrical failure and offers security.
- Resilience: Nylon elements can resist vibrations, humidity, and changes in temperature, making it ideal for use in automobiles.
- Easy Manufacturing: Nylon can be cut into various shapes, thus making complex electrical components.
Fuel Systems
Automobile manufacturers have used nylon for fuel system parts because it is resistant to fuel and chemical damage:
Applications:
- Fuel Lines: Nylon fuel lines are lightweight, durable, and fuel resistant, delivering fuel in a clean manner.
- Tanks: In some fuel tanks, reinforced nylon is used which replaces the metal with a lighter material without compromising strength.
- Emission Control Systems: Nylon parts control emissions by controlling fuel vapor and exhaust gases.
Benefits:
- Fuel Permeation Resistance: Nylon blocks fuel vapor from escaping, which enables manufacturers to comply with strict emissions regulations.
- Corrosion resistance: Nylon doesn’t corrode from fuels or chemicals, making it a very durable fabric.
- Flexible: Nylon’s flexible nature makes it easy to install and reduces the likelihood of stress-related fuel lines and systems failures.
3. Nylon in Structures and Machines.
Nylon has proven itself as an essential material for both structural and mechanical parts in contemporary automobile manufacturing. It’s strength, durability, and lightness make it a perfect replacement for conventional materials such as metals. In the next two parts, we’ll talk about what it does for certain tasks and what its benefits are.
Lightweight Substitutes for Metals
Incorporating engineered nylon into structural and mechanical components is a revolutionary approach for car makers who want to lighten their vehicles without sacrificing performance.
Applications:
- Gears: Nylon is increasingly used for timing gears and other drivetrain components. Its self-lubricating nature eliminates friction and wear, making it cost effective and convenient.
- Bearings: The nylon bearings are light, corrosion resistant and quieter than the metal ones. They’re particularly helpful in situations where noise is an issue.
- Brackets: Nylon brackets hold on to most automotive systems such as electrical and fluid lines to ensure they work reliably under load.
Advantages:
- Weight Saving: Compared to metal components, Nylon parts are much lighter than metal, which directly improves gas mileage and lower emissions.
- Price: The Nylon parts are affordable to manufacture since they require less raw materials and are easier to produce by injection molding.
- Noise Reduction: Nylon’s inherent vibration- and noise-reduction properties make it a perfect choice for gears and bearing frames, enhancing ride quality.
- Durability: Unlike metal, nylon will not rust or corrode when wet or subjected to chemicals, which will prolong the service life of equipment.
Case Study:
Glass-reinforced nylon gears for power steering applications showed considerable weight savings and durability improvements over traditional steel gears. They’re also less noisy and efficient, which makes driving more enjoyable.
Hybrid and Electric Vehicles
The move to hybrid and electric vehicles (EV) has driven nylon’s entry into high-use markets. It’s imperative to choose light, robust materials that deliver the best battery performance and are optimized for energy efficiency.
Applications:
- Battery Housings: Battery housings are made from nylon that offer structural integrity while reducing weight. High-tech compounds provide resistance to heat and flames, which is safe in high-temperature applications.
- Machine Cooling Systems: Polyester is used for coolant lines and hoses due to its heat and chemical resistance. They are essential to balancing the thermal requirements of electric drivetrains.
- Lightweight Frame Components: Nylon composites are applied to vehicle frames and body parts, allowing companies to reduce weight without sacrificing strength.
Advantages:
- Enhanced Energy Efficiency: Lightweight nylon materials lighten the overall weight of EVs to increase the range of drives and reduce energy usage.
- Safety: Nylon’s high temperature performance and flame retardancy makes it perfect for batteries and other applications where safety is a concern.
- Design Flexibility: Nylon’s mouldability lets you design elaborate fully assembled parts that make assembly much easier, eliminating the need for additional fasteners or reinforcements.
Future Outlook:
With the rapid increase in EV usage, the use of high-performance nylon in battery materials and lightweight constructions is expected to grow. New materials like carbon-fiber reinforced nylon composites are likely to be major drivers for improving future car design and performance.
4. Environmental and Economic Advantages of Nylon in Automotive Industry
The automotive sector reaps significant environmental and financial benefits by using nylon in vehicles, as part of the industry’s sustainability and cost savings strategies.
Fuel Efficiency
Perhaps nylon’s biggest contribution to auto production is its ability to reduce emissions:
- Weight reduction: by substituting nylon for heavier metals such as steel and aluminum, manufacturers can produce lighter vehicles. Vehicle weight reduction directly contributes to improved fuel economy, as less energy is required to accelerate the vehicle.
- Energy Efficiency: Because nylon lubricates moving parts, including gears and bearings, its efficiency also reduces the loss of energy.
- Low emission: Nylon-based vehicles also create fewer greenhouse gases thanks to their fuel efficiency, making it easier for automakers to meet strict emission standards.
Case Example:
For internal combustion engines, use of nylon composite intake manifolds has reduced component weight up to 60% over aluminum models and resulted in tangible improvements in fuel economy.
Cost Savings
Nylon is a cost effective substitute for the common materials used in car manufacturing.
- Cost of Raw Materials: Nylon is generally less expensive than metals like steel or aluminum, particularly considering the energy-intensive processes needed to extract and form metals.
- Efficiency in Manufacturing: Nylon’s compatibility with injection molding makes it possible to produce complex components on a large scale quickly and reduces labor and tooling costs.
- Maintenance savings: Due to its strength and resistance to damage, nylon elements last longer, thus reducing repair and replacement costs for manufacturers and end users.
Example:
Nylon automotive wiring harnesses are easier to manufacture and maintain over time than the traditional types, saving you a significant amount of money.
Sustainability Initiatives
This environmental imperative has pushed the automotive industry towards recycled and sustainable nylons:
- Recycled Nylon: Materials such as Econyl (sourced from discarded fishing nets and industrial scraps) are found in automobile interiors and components. Nylon recycled not only saves landfill space but helps to diminish the need for virgin resources.
- Lifecycle Impact: Nylon’s recycling capabilities help manufactures to build closed-loop processes where retired parts are reused in new products, creating as low an impact as possible on the environment.
- Low Power Production: New manufacturing techniques reduce the amount of energy needed to manufacture nylon making it a sustainable material.
Case Study:
Many car manufacturers, including luxury brands, incorporate recycled nylon into carpets, trims and engine components to showcase the material’s adaptability and sustainability.
A Holistic Approach to Sustainability
- Partnerships: Partnerships between automakers and material developers are driving advances in recycled and biodegradable nylons.
- Awareness: In order to keep up with the demand of sustainable automobiles, the sustainable nylon is a major selling point for eco-conscious consumers.
- Future Prospects: Automotive companies are seeking opportunities to include bio-based nylon (from renewable sources such as castor oil) in its products for greater sustainability.
5. Issues with using Nylon in Automobiles
While nylon has largely become the foundation of vehicle engineering, it’s not without its challenges. It is crucial to address these shortcomings in order to maximise its potential and make sure it is put to good use in the demanding driving environments of today’s automobiles.
Heat and UV Sensitivity
The heat and UV damage of nylon makes it a tough material, particularly on the exterior and underneath the car.
Heat Sensitivity:
Nylon breaks down with prolonged exposure to high temperatures. This constraint holds especially true for parts such as engine parts that need to go through high-temperature cycles.
- Impact: Heat can cause nylon to stretch, weaken or break and undermine parts.
Solutions:
- High Temperature Grades: Higher temperature grade nylon materials, like nylon 6T and nylon 46, offer high performance.
- Additives: Additives can be added to make the material heat resistant and keep the performance stable when exposed to high temperatures.
- Application Design: Engineering designs that eliminate the direct heat source or utilize heat shielding can increase the resiliency of nylon components.
UV Sensitivity:
Exposure to UV rays can make nylon fade, become brittle or mechanically degraded over time, and this is an issue for trims and brackets on the exterior.
Consequences: UV damage damages parts both cosmetically and functionally.
Solutions:
- UV Stabilizers: When manufactured, UV-blocking additives can stave off the damage.
- Coatings & Treatments: Protective coatings (such as paints or laminates) provide an additional barrier against UV rays.
- Blends and Composites: Using nylon with materials that resist UV rays can make it more durable for outdoor use.
Structural Limitations
Nylon is robust and versatile, but it might be structurally unsuited to certain high-stress applications without reinforcement.
Challenges:
- Nylon in its pure state isn’t as stiff or durable as steel or advanced composites.
- It can creep in response to long-term mechanical forces (creep), which is not a desirable property in structures.
Solutions:
Reinforcement Techniques:
- Glass Filled Nylon: Filling nylon with glass fibres boosts its tensile strength, stiffness, and resistance to deformation. Which makes it suitable for load-bearing items such as brackets and engine mounts.
- Carbon-Fiber-Reinforced Nylon: The use of carbon fibers helps to provide ultra-lightweight parts with a superior mechanical response, ideal for high-performance use cases.
- Polymer Composites: Nylon mixed with metals or other polymers yield composites that combine the best attributes of all components.
- Optimized Design: Building components can be designed with ribbing, gussets, or other characteristics to distribute stress more efficiently and reduce the risk of failure.
Cost vs. Performance
Keeping costs down while still meeting the performance needs of engineering-class applications remains a pressing concern for manufacturers.
Challenges:
Specialty grades of nylon and reinforced formulations cost more than regular grades.
Additives, processing, and quality assurance may raise production costs.
Strategies for Balance:
- Material Optimization: Use higher grades only when required, use ordinary nylon for less severe applications.
- Scale Economies: Massive volume could cut the per-unit price of high end nylon components.
- New Production Methods: High-end manufacturing techniques, like 3D Printing and Injection Molding, facilitates the manufacturing of nylon parts accurately and at a reasonable cost.
- Recycled Materials: Recycling nylon adds to raw material savings and helps in achieving sustainability.
6. New Nylon Designs for Automobile Engineering
The automobile sector is using new nylon technologies to overcome these challenges and increase its uses.
High-Performance Nylon Composites
Applications:
Lightweight, high-strength components, including body panels, frame supports, and battery cases, are manufactured from carbon-fiber reinforced nylon (CFRN).
Advantages:
- Ultra-Lightweight: CFRN reduces weight by up to 20 times that of metal and even conventional glass-filled nylon.
- Superior Hardness: It’s as mechanically strong as aluminum, and is easy to shape into intricate structures.
- Thermal Stability: CFRN is ideally suited for applications where heat and pressure are present.
Future Potential:
The advances in composite technology may continue to replace metal in the chassis and suspension of vehicles on a large scale.
Smart Materials
Combining sensors and electronics with nylon is driving future intelligent materials in auto design.
Applications:
- Predictive Maintenance: Nylon components fitted with sensors detect stress, temperature, and wear continuously, which is useful for predictive maintenance.
- Adaptive Materials: Nylon smart materials can adapt to the environment and modulate rigidity or reduce vibrations to enhance vehicle performance and ease of use.
Example:
A smart nylon spring in the suspension might change depending on the driving environment, making the ride smoother and safer.
3D Printing
Additive production in nylon is changing the way automotives are prototyping and manufactured.
Applications:
- Prototypes: Since nylon is very easy to print and process, it’s a great material for prototyping both functional and structural pieces.
- Modifications: 3D Printing can be used to create custom components for exclusive cars or accessories.
- Minimal Weight Structures: Highly intricate, light weight structures that cannot be crafted by hand can be manufactured using 3D printing.
Advantages:
- Short Lead Times: Prototypes and parts can be created in a short amount of time, which helps in minimizing the development times.
- Material Efficiency: Additive manufacturing eliminates as much waste as subtractive manufacturing.
- Design Freedom: Nylon 3D Printing allows for complex geometries and layered features.
7. Trends in Automobile Nylon Uses Future Report 2017/18
- Electric Vehicle Revolution
Expanded Use:
Nylon’s lightness and thermal conductivity are essential for battery enclosing, cooling, and EV high voltage wiring.
Innovations:
New nylon composites and thermal stabilizers make safer, more efficient batteries possible, and they are helping to accelerate the global electric revolution.
- Circular Economy
Recyclable Nylon:
In the automotive industry, nylon is also becoming more recyclable, aiding in the circular economy.
For instance, nylon from fishing nets or post-consumer waste is recycled into car interiors and parts.
Biodegradable Options:
Advances in bio-based and biodegradable nylons will further reduce the carbon footprint of automotive production.
- Integration with Advanced Manufacturing
Automation and Robotics:
Nylon is becoming increasingly prevalent in robotic assembly lines, providing a high degree of accuracy.
Future Possibilities:
Integration with Industry 4.0 technologies like AI and IoT will enable nylon parts to be produced and tracked with unmatched accuracy and productivity.
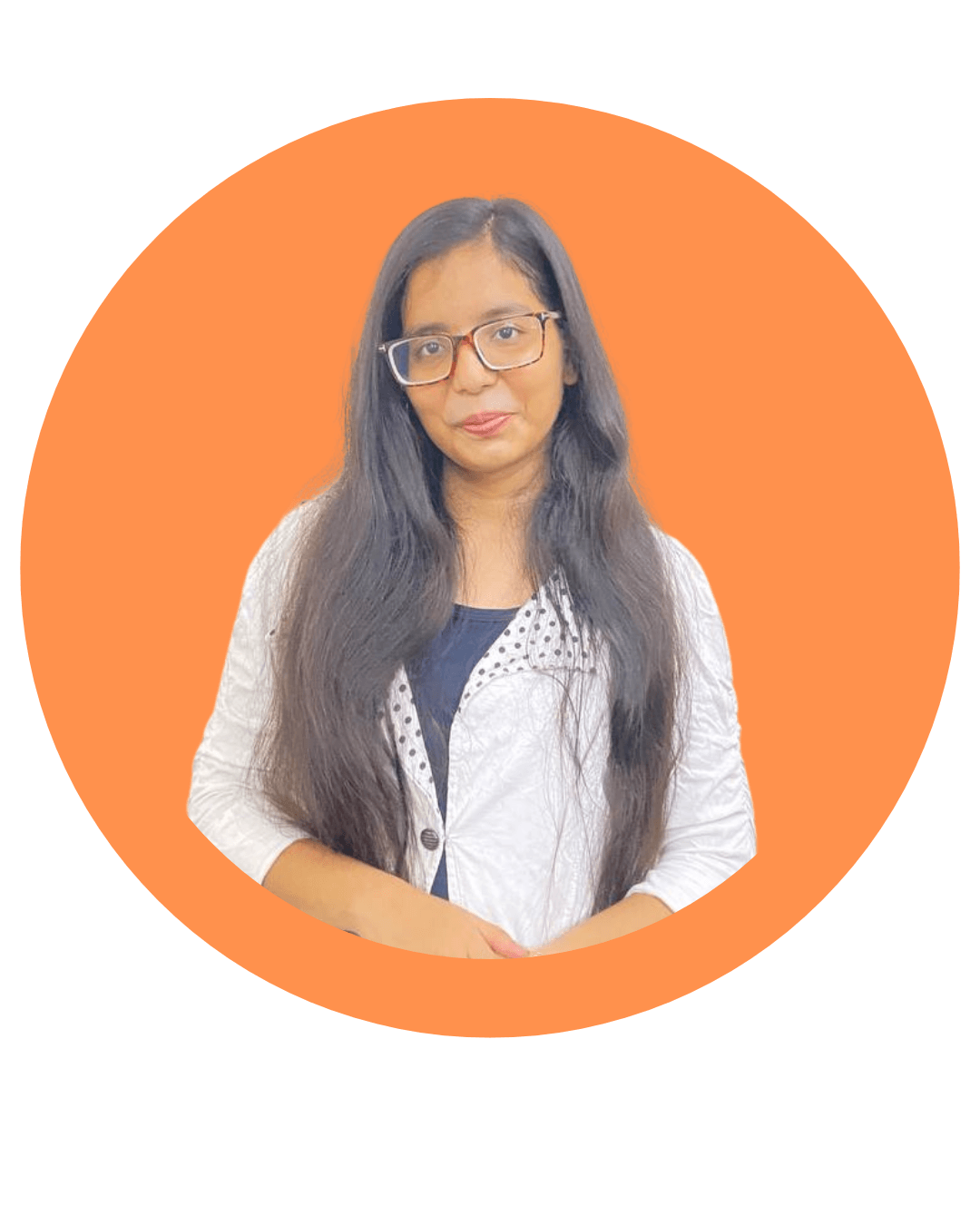
Yashvi Jain, a writer by day and reader by night, is an accomplished content writer and published author of ‘Mind Under Construction. Yashvi possesses extensive knowledge of fabrics, sustainability, and literature. On occasions, you would catch her scripting for her YouTube channel, engrossed in fiction, or ardently dedicating her time to research and storytelling.