Introduction
Industrial fabrics form a critical part of every industry as they lend resilience, hardness and performance to all applications. These textiles are specialised for high-wear environments and the raw materials in their production are selected on the basis of their capability to fulfill certain functional demands. Of all the fibres that are produced for industrial textiles, one of the most versatile, hardy and widely employed synthetic fibres is nylon. In this post, we cover the impact of nylon in industrial textiles, its main features, applications and application in various industries.
Synthetic polymer Nylon, created in the 1930s by the chemist Wallace Carothers and his colleagues at DuPont, was invented to replace this substance. Nylon has been popular in consumer and industrial goods ever since it was developed, because of its strength, malleability, abrasion resistance and other characteristics. Due to its multifaceted nature, it’s used in numerous applications from automobiles and construction to filtration and manufacturing.
The article below will take you step by step through nylon’s most important features that make it the ideal material for industrial textiles and show how it can be used in many different fields. The article will also highlight nylon advantages, disadvantages, and what is the future outlook and innovation in industrial textiles made with nylon.
1. Important Functions of Nylon in Industrial Fabrics.
There are several properties of nylon that are very beneficial to industrial textiles. These include resistance, hardness, elasticity, corrosion resistance, moisture resistance and chemicals. Let’s dive into each of these features and see why nylon is the industrial choice.
Durability and Strength
That is the first thing that keeps nylon on the industrial market: it is durable and robust. Polyester fibres are strong – they can resist a lot of force before they break. The strength also makes nylon the perfect material for fabrics under extreme loads — like rope, conveyor belts and high-density fabrics. Wear resistance of nylon without compromising its structural strength is extremely important in manufacturing areas where durable and dependable products are needed.
The tensile strength of nylon, too, means it will not rip and crack in the face of heavy use. Nylon helps keep goods running when it’s needed and is used in manufacturing and industries, where equipment and products frequently encounter a lot of impact forces.
Because nylon stays tough in a variety of conditions such as temperature, moisture, and chemical attack, it’s great for the outdoors and extreme conditions. Nylon ropes for construction or shipping, for instance, won’t break under pressure and will allow you to handle objects safely.
Resistance to Abrasion
Nylon also has the anti-abrasion ability. These fibers of nylon are highly resistant to friction and this is necessary in some applications that are repeatedly rubbing or being worn. In factories, objects often get touched or moving a lot and that leads to friction and wear. The abrasion-resistant properties of nylon prolong the life of industrial fabrics so that they still function, even in the worst conditions.
For instance, in conveyor belts, nylon’s abrasion resistance means that the belts will keep moving without failing. Further, nylon textiles are durable in their surface, which can tolerate repeated movement — perfect for use in manufacturing processes such as packaging, sorting, and shipping materials. Nor does nylon’s abrasion resistance provide any protection in protective clothing such as gloves that are subjected to all-day friction when workers operate heavy machinery or materials.
The abrasion resistance of nylon also makes it a great material for geotextiles and other construction materials that are exposed to hard environments like soil and gravel. Because nylon is more durable, these fabrics can endure longer and thus bring benefits for the long-term in infrastructure work.
Flexibility and Elasticity
The stiffness and elasticity of nylon is another strength in industrial fabrics. Flexible nylon can stretch and flex, but doesn’t unravel or warp, which is vital for textiles that need to move with you or the way the weather changes. Stretch and bounce make nylon the perfect material for ropes, safety gear and performance fabrics where both durability and flexibility are needed.
For example, nylon ropes and cords are commonly used in shipping, building and climbing because they can be pulled or stretched without breaking their strength. This stretch is a big advantage of nylon fabrics when applied to moving and challenging environments where textiles are frequently bending, stretching and twisting.
The stretch of nylon is also used for comfort and performance in safety clothing like work uniforms and work vests. : Stretch without sacrificing strength allows the fabric to move with the wearer for optimal comfort and flexibility while working out.
Moisture and Chemical Resistance
A second great quality of nylon is that it’s waterproof and chemical resistant. Nylon doesn’t soak up moisture as well as natural fibres such as cotton, making it great for use where moisture resistance is important. Polyester fibres are hydrophobic, that is, they repel water, a necessity when moisture can erode fabrics.
For auto production, marine and chemical production, nylon’s water resistance means fabrics do not become brittle from water or oil. For instance, nylon materials are found in automotive seat covers and upholstery where moisture is a concern. These fabrics are protected from water bleed by the strength of the fabric.
Because nylon is chemically resistant, it can also be employed where you may be exposed to strong chemicals. The polymer structure of nylon means it doesn’t dissolve under the pressure of oils, solvents and industrial chemicals. This is crucial in fields such as chemical process and manufacturing, where textiles need to withstand the harsh conditions without compromising performance.
2. Uses of Nylon in Industrial Fabrics.
Because nylon is so adaptable, it can be used for a multitude of uses in industrial fabrics. Here are some of the main sectors where nylon finds its use.
Conveyor Belts
We can find nylon conveyor belts used in mining, manufacturing, and distribution industries. Nylon is tough and resiliency that will help to support hefty weights and thus the material to be travelled at long distances. Conveyor belts made of nylon are very pliable and they can handle huge amounts of goods without rusting quickly.
Not only do they resist abrasion and chemicals, nylon conveyor belts are also rust-proof. Belts that move material very aggressively – in cement plants, or steel mills – benefit from nylon’s heat resistance, friction and resistance to toxic chemicals. All of this means the belts are strong enough even when used under very demanding working conditions.
It’s also very flexible in nylon, meaning that conveyor belts can pass through curves and corners without breaking or cracking. Strong, abrasive and flexible, nylon is a great material for this industrial application.
Protective Clothing and Safety Gear
The manufacturing of safety gear and protective clothing for a variety of construction, manufacturing, and mining uses is the primary use of nylon. Workwear such as gloves, jackets, pants, uniforms, etc are manufactured from nylon fabric, which is durable, flexible and impervious to abrasion.
Polyester textiles for safety clothing are built to endure the harsh physical conditions and shield workers from harm. Nylon gloves, for instance, can be durable enough to withstand cuts and abrasions, and nylon jackets can resist heat and chemicals. Because of the stretch of nylon, these outfits are able to offer both the support and fit you need.
Beyond conventional work wear, nylon is used in special protective apparel like fireproof clothing because of its resistance to heat and flames. It is common to find fabric made of nylon treated with fire retardant coatings for additional fire resistance in extreme conditions.
Ropes and Cords
The industry of nylon ropes and cords are used in all sorts of industries such as shipping, construction, and outdoors. All of this combined with nylon’s strength, elasticity and abrasion resistance makes it perfect for ropes that have to resist large loads, tension and friction.
The stretchability of nylon also comes in handy when designing ropes for situations with movement and stress. For instance, when you’re climbing, nylon ropes stretch in response to the shock of a fall so as to minimise its effect on the climber. As in seafaring, nylon ropes anchor ships and load cargoes due to its indestructibility in saltwater conditions.
Nylon ropes are used for lifting and fastening materials in the construction industry where durability is a must. The ropes are so tough they aren’t ruined even when the surface is hard, and they are perfect for extreme conditions.
Filtration Fabrics
Nylon is also used for industrial filtration fabrics. Because it resists chemicals and moisture, it can be installed in air, water and liquid filtration systems. The thin mesh of nylon filters dirt and helps it hold up in the long run.
Nylon filters are used in wastewater treatment, air filtration, and chemical filtering applications in industry. The nylon’s chemical resistance means the filters are durable under the most aggressive chemicals such as acids and oils. Filtration fabrics made of nylon are also used in food and beverage applications to remove contaminants from fluids to maintain the quality and safety of products.
Because of its resistance to pressure and durability, nylon is the best material for industrial filtration.
Automotive Textiles
The automobile industry is also another field where nylon finds a role. The fabric nylon is used in all types of car textiles such as upholstery, seat covers, carpet and airbags. It is highly resistant to wear, toughness and chemical damage which makes nylon ideal for interior surfaces of cars where material is exposed to extended use, sun exposure, moisture, and changes in temperature.
Nylon in seat covers is stain-resistant so the cloth doesn’t fade and looks the same with time. And because the material is stretchy, it can adapt to the seats’ curves, making them comfortable yet durable. Polyester is also employed in automobile airbags, which require a heavy fabric to resist the pressure of a rapid inflation.
3. The Use of Nylon in Textile Industries.
Nylon has always been the standard material used for industrial textiles as a strength, durability and versatility fabric. For all those fields where you want to create durable fabrics, nylon is just the thing. In this chapter, we will be discussing the main pros of nylon including cost effectiveness, light weight but strong, and great versatility for different industrial applications.
Cost-Effectiveness
Cost Relative to Other Fibers
For industrial textile fibres, the main thing that matters is the price of the fibre. Nylon is an inexpensive option for a multitude of industrial uses, and the performance/price ratio is favorable when compared with most natural and synthetic fibres.
Cost of raw materials – nylon is less expensive than natural fibres with higher-performing properties such as silk or wool that can be grown and processed in highly specialised environments. What’s more, nylon is also fairly simple to produce, making it cheaper to produce. Instead of using crops and a longer production process like cotton, nylon can be manufactured much faster and more efficiently by using synthetic fibres. That is why it is ideally suited for mass production.
Nylon’s economic advantage in industry is not just about the price of the material. Because nylon is incredibly durable, you can also save on the cost of ownership by increasing the life of products made from it. It is a tough business with industrial textiles — tearing, twisting, chemicals or UV light. Fabrics such as cotton or polyester will wear out more quickly in the face of these forces, and so will be replaced more often. But nylon lasts, resisting wear and tear, so it’s a long-term investment that can be replaced less frequently.
Time and Performance Saving You Money.
Nylon also has the cost advantage of lasting longer. And while other fibres can easily break down in the harshness of the factory environment, nylon maintains long life because it’s already hardy and durable. This strength is why nylon is popular for industrial ropes, conveyor belts, safety suits and filtration fabric applications where quality matters.
For instance, in auto industries nylon is utilized for various linings inside the car like seat covers, airbags, and upholstery. These wear out under the effects of usage, UV light and general wear and tear. These things are not a problem with nylon and that means that the products last long and that they are worth your money in the long run. It also means fewer breakdowns in industrial facilities, where machinery or infrastructure is required. You save money on maintenance as nylon doesn’t have to be maintained as frequently or replaced as something that’s constructed with cheaper materials.
What’s more, nylon has the shape retention and resilience to fatigue, so it always works well. Not only will it ensure safety in applications such as ropes or geotextiles but it will prevent operation interruptions due to failure of materials.
Lightweight Yet Strong
- Why Nylon Is So Light Weighed?
This is the lightness of nylon that is also an industrial textile benefit. This property is particularly useful in the industry where weight is a significant factor in operating productivity, like materials handling, building, automotive industries, etc.
For instance, the automotive sector is trying to reduce weight of cars to get more fuel economy and performance. These are made possible by the density of nylon. Car seat covers, airbag fabrics and underbody parts fabricated from nylon are much lighter than the same products made from traditional steel or thicker natural fibres. Nylon allows manufacturers to lighten these parts without losing their durability or performance.
Nor is it true in building construction or materials handling, where objects must be pushed, lifted or carried over a great distance, but nylon fibres such as ropes, straps and conveyor belts are much more manageable than their steel or other metal equivalents. Nylon ropes, for example, are thinner and lighter, but still durable and slender. Then there is not only reduced physical pressure on the worker but also efficient processes that can directly affect productivity.
Similarity to Heavy Fabrics, Such as Steel or Cotton.
Compared to steel (which is very strong), nylon has comparable tensile strength for a third of the weight. Nylon is best for industrial use, where strength without weight matters. Steel is a heavy substance and the structure or product itself often becomes heavier using it which could cost more in terms of energy and transportation.
Nylon, meanwhile, is much lighter, but can do the job as well as steel does in some circumstances. It’s also the perfect choice for applications like heavi-duty ropes, cables and conveyor belts where strength-to-weight ratio is essential. The fact that nylon absorbs and disperses stress and is very elastic means that it will withstand high load without loosing flexibility or weight benefits.
What’s more, nylon also fare better than cotton in many industrial applications. While cotton is a soft and durable natural fibre, it’s far less strong, abrasive and durable than nylon is for industrial fabrics. Fabrics made from cotton shrink faster under chemical or UV exposure or extreme friction, leading to higher costs for replacement and lower performance. Rather, nylon is more resistant to wear and degradation, and so more reliable in high-wear industrial use.
Adaptability and Versatility
Engineering Nylon for Diverse Applications
That flexibility is one reason why nylon is a favourite for industrial textiles. But unlike other fibres, which are sometimes used only in certain applications, nylon can be manufactured in several shapes and configurations for a wide variety of industries. It is this flexibility that allows nylon to be used in everything from softer, more stretchy fabrics to high-performance industrial products.
: Nylon is used in manufacturing as both filaments and staple fibers, and it can be spun into yarns or woven into textiles. The nylon that is chosen for a particular application is determined by the performance requirements of the garment — strength, elasticity, water and UV resistance, etc. It’s this capacity to tailor nylon fibers to the end-use application that makes nylon a fundamental material in sectors as wide-ranging as automotive, construction, safety and filtration.
Nylon, for instance, can be found in many products in the automobile world — seat covers, airbags, underbody panels. In this market, nylon is developed for light weight, impact resistance and environmental protection (high temperature, oils, UV radiation etc). This is the same general versatility of nylon in filtering systems, where nylons of various types are employed for water filtration, air filtration and liquid filtration because of their chemical resistance and fine meshability.
It is also used to produce geotextiles in geotechnical engineering — for stabilisation, drainage and road building. These geotextiles are designed to withstand the abuses of moisture, chemicals and UV rays so nylon is a great candidate for such uses.
Nylon in All Shapes and Flexibility – What Does It Do?
You can get nylon in monofilament, multifilament and staple fiber, and so many applications. That it can make nylon in various configurations means that it can fulfill the mechanical, thermal and chemical demands of industrial applications.
Monofilament nylon is generally applied in the areas where strength and toughness are important: in ropes, fishing lines and industrial textiles. Multifilament nylon, however, is used for textile fabrics such as those used in automotive upholstery, filtration products and clothing. Staple fibres are spun to yarns that are used in textiles, including those that need to be soft, flexible and comfortable.
Nylon is versatile also across the different industries. From nonwovens for filtration applications to high-density woven fabrics for conveyor belts and safety equipment, nylon can be designed to fit various industries.
4. Challenges and Options in Using Nylon in Industrial Textiles.
Nylon has a lot going for it, but it also has its limitations, which must be overcome if it is to be exploited to its full potential in industrial fabrics. These problems are its ecological footprint, degradation and production cost.
Environmental Impact
But nylon is the main negative point. Nylon is a synthetic fiber, extracted from petroleum-based resources, and the manufacturing process is energy-hungry. Also, nylon is not biodegradable, so it can remain in the environment for decades, and this is plastic pollution.
But there’s been some big strides in reducing nylon’s impact on the environment. Demand for eco-friendly materials resulted in the creation of recycled nylon, made from post-consumer scrap materials like old nylon fabrics or plastic bottles. Recycled nylon is much more eco-friendly than virgin nylon as it uses a lower energy amount and doesn’t demand as much raw material. Most top brands and suppliers are now using recycled nylon in their designs for sustainable industrial textiles.
Wear and Tear Over Time
Nylon, too, can wear out when subjected to UV rays, chemical agents or extreme temperatures for long periods of time. Nylon can be wear-resistant in the short term but when it is subjected to environmental stresses over time it becomes weaker, more elastic and less resilient. That’s especially true in outdoor and industrial uses where nylon products are exposed to the elements on a daily basis.
For this reason, nylon is constantly being optimized for UV degradation and abrasion resistance. This is by UV coatings, additives and advanced nylon composites to strengthen the materials against environmental stresses. These technologies are making nylon-based products last longer in industrial textiles.
Cost of Production
Production of nylon fibres consumes huge amounts of energy using petroleum feedstocks. Thus, the price to manufacture nylon can be higher than that of other fibers, especially virgin nylon. But with new technology and the use of more recycled nylon, production is dropping. Then there’s the research on more efficient manufacturing technologies and new feedstocks, which could further cut the carbon footprint and expense of nylon production in the future.
5. Nylon Trends for Industrial Textiles to 2025?
Nylon’s future in industrial fabrics depends on the success of sustainability, technology and performance. The future of nylon textiles in many sectors is defined by a number of trends.
Recycled Nylon
Demand for sustainable alternatives is driving the use of recycled nylon in industrial textiles. When used in recycled products, the manufacturers save on virgin nylon, while saving on the carbon footprint. In textiles such as automotive textiles, safety wear and filtration systems, recycled nylon is used in more products that use it for sustainability instead of nylon.
And circular economies in textiles are driving adoption of recycled nylon, too. With more businesses committing to recycling and switching to closed-loop production lines, nylon is becoming a leading candidate for more sustainable textile production.
Innovations in Nylon Manufacturing
A lot of new technologies are being invented to help make nylon more useful in the workplace. New methods of production are making nylon production more efficient, consuming less energy and leaving less waste. There’s also smart fabrics using nylon — which is another exciting research topic. Such textiles might include things such as temperature control, performance control and improved durability that would make them ideally suited for industrial applications.
Sustainability in Industrial Textiles
The future of nylon in industrial fabrics will be shaped by the sustainability movement. Because industries will be looking for ways to make things environmentally friendly, eco-friendly materials will only grow in importance. Nylon – with its recycling capacity and manufacturing innovation – could be a major contributor to the move towards more sustainable textiles.
Circular Economies in Textile Production
It will have a direct effect on the future of nylon as well as the circular economies in the textile industry. Circular economies prioritise waste reduction and material re-use. Nylon is recyclable, so closing the loop makes it an essential material and recycled nylon is becoming more of a fixture in the textile industry. Through recycling, waste minimisation and production efficiency, nylon can lead to a greener future for industrial textiles.
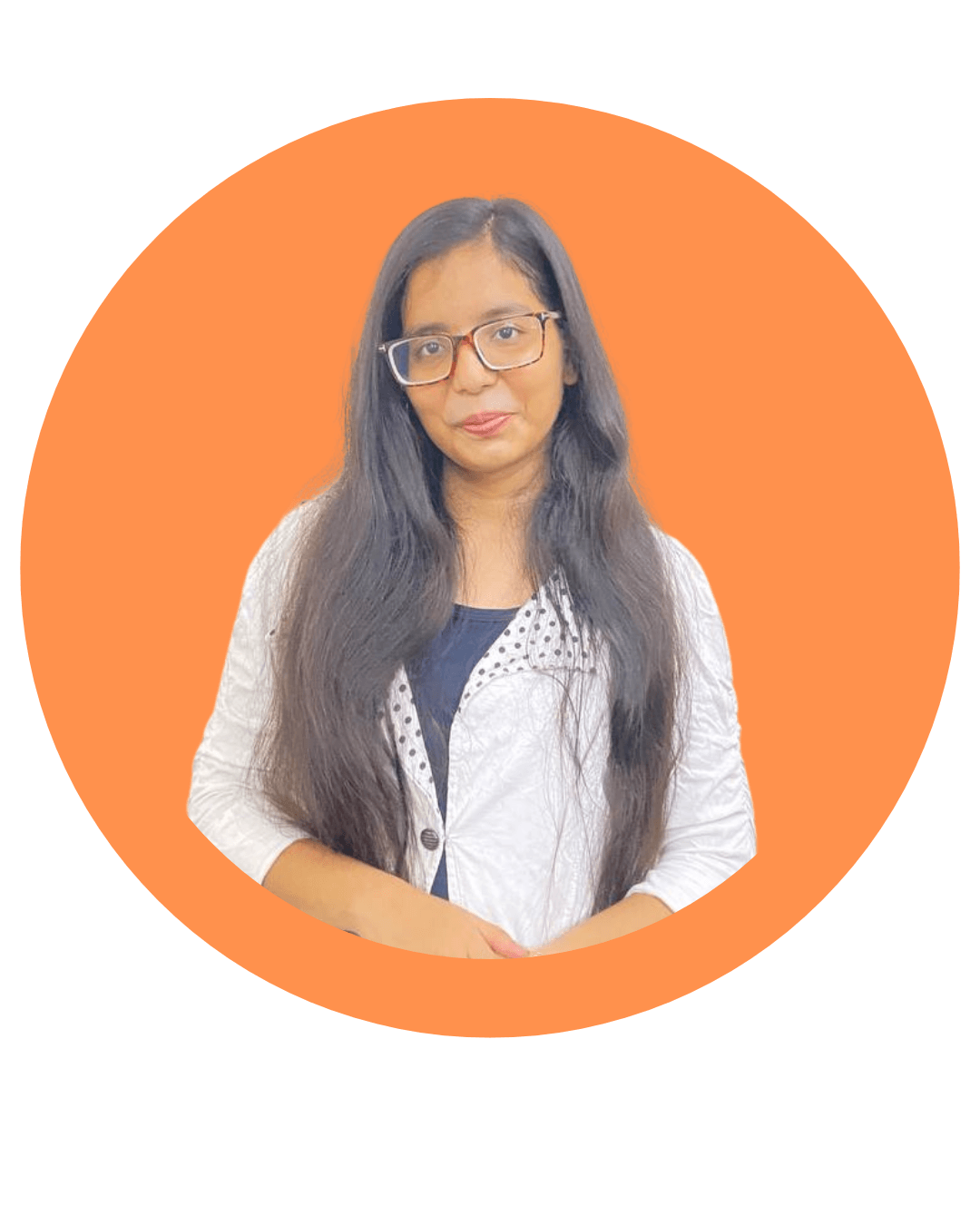
Yashvi Jain, a writer by day and reader by night, is an accomplished content writer and published author of ‘Mind Under Construction. Yashvi possesses extensive knowledge of fabrics, sustainability, and literature. On occasions, you would catch her scripting for her YouTube channel, engrossed in fiction, or ardently dedicating her time to research and storytelling.