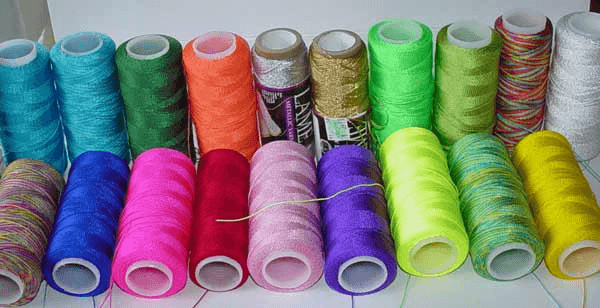
Introduction
The world has many of the most popular and functional synthetic fabrics – nylon. The tough, supple and abrasion resistant nylon finds application in everything from clothes and bedding to industrial and military products. The nylon technology, invented in the 1930s by DuPont, changed textiles by providing a durable substitute for silk, cotton and wool.
Consumers and business people need to know how nylon is produced. It explains the process by which inert things become a material found all around us. Second, with sustainability getting a lot of attention these days, knowing how nylon gets made is useful to know how it impacts the environment and what needs to be done to create better alternatives.
The entire process of nylon manufacturing, from raw materials to finished fabric, is covered in this how-to manual, which includes information on chemistry, manufacturing, and waste.
1. Raw Materials for Nylon Production
- Petrochemical Origins
Nylon is an artificial polymer made from petrochemicals, one of the polyamides. Nylon is made by scavenging crude oil, which is the main raw material from which it’s made.
These are the main monomers of nylon:
- Adipic Acid: One of the main ingredient in making Nylon 6,6.
- Hexamethylenediamine: Also found in Nylon 6,6 this diamine reacts with adipic acid to create the polyamide.
- Caprolactam: The primary monomer in Nylon 6 manufacturing. Caprolactam goes through a different polymerization process than Nylon 6,6.
Importance of Crude Oil
Petroleum oil is the precursor to these monomers and they are then chemistryd to create the molecules that are needed. This dependence on fossil fuels makes it evident how unsustainable the traditional nylon process is and how it afflicts the planet.
1.2. Environmental Concerns
The extraction and refinement of petrochemicals for nylon manufacture is a big environmental problem:
- Carbon Outgasses: Production of adipic acid and caprolactam generates a lot of carbon dioxide and nitrous oxide, the main greenhouse gases.
- Resource Depletion: As we depend on the crude oil which is a finite resource, we deplete resources.
- Air and Water Pollution: Chemical products and byproducts of nylon production pollute air and water.
Sustainable Alternatives
In the face of these pressures, there is a drive to find more sustainable raw materials for the manufacture of nylon:
- Bio-based Nylon: Scientists are testing renewable fuels like plant oils and sugars to make bio-based adipic acid and caprolactam.
- Nylon made of Recycled Material: Waste from the consumer such as fishing nets and fabric is converted into premium recycled nylon, which reduces the use of virgin petrochemicals.
2. Polymerization: The Formation of Nylon
Polymerization — the chemical reaction that transforms monomers into long chain polymer molecules (the origin of nylon fibers). There are two main kinds of nylon-Nylon 6,6 and Nylon 6, each made by using different polymerization processes.
- Condensation Polymerization (Nylon 6,6)
The material Nylon 6,6 is made through condensation polymerization, where two monomers (adipic acid and hexamethylenediamine) react to form a long-chain polyamide.
Steps in Condensation Polymerization
- Monomers to Mix: Adipic acid and hexamethylenediamine mixed under controlled conditions.
- Polymerization Reaction: Monomers get condensed resulting in the escape of water.
- Conversion into Nylon Salt: The reaction produces first a crystallised intermediate that can be called nylon salt.
- Heating and Polymerization: The nylon salt is hot (about 280°C) in order to start polymerization process that produces long chains of Nylon 6,6.
Properties of Nylon 6,6
- High tensile strength.
- Great heat and scratch resistance.
Used in automotive components, textiles, industrial fabrics and athletic fabrics.
- Ring-Opening Polymerization (Nylon 6)
Nylon 6 is made by ring-opening polymerisation, another process that starts with caprolactam.
Steps in Ring-Opening Polymerization
- Thermal Processing Caprolactam: Caprolactam is heated to about 260°C in the presence of a catalyst.
- Polymerization Reaction: Caprolactam’s cyclic structure opens, the molecules fuse into long chain polyamide molecules.
- Formation of Nylon 6 Polymer: The polymer chains result in Nylon 6.
Properties of Nylon 6
- Lower melting point than Nylon 6,6.
- Good elasticity and flexibility.
- Fabric, Packaging, Consumer goods: Used most commonly.
3. Spinning: Creating Nylon Fibers
After polymerisation, the nylon polymer is ready for spindling to turn into fibers.
- Melt Spinning Process
The most widely used production technique is melting spindle to spin nylon fibres.
Steps in Melt Spinning
- Heat Melting of Polymer: The nylon polymer is heated to melt the polymer and form a thick liquid.
- Extrusion Through a Spinneret: The liquid polymer is pressed through a spinneret, a machine with tiny holes to deform the polymer into fine filaments.
- Cooling and Consolidation: Extruded filaments are cooled fast, then harden into uniform fibers.
- Spindling the Filaments: The filaments are spun into spools to be processed.
Importantly Controlling Temperature And Pressure is a must.
Control of temperature and pressure at extrusion is key to keeping the fibers of nylon uniform, strong and quality.
- Drawing and Orientation
When the fibres are ready, they are drewn in order to give them more mechanical strength.
Steps in Drawing
- The Stretching of the Fibres: The nylon filaments are drawn to several times their original length.
- Polymer Chains Aligning: This stretching moves polymer chains within the fibers, making them tensile and elastic.
- Heat Setting: the pulled fibres are re-assembled to fix their new molecular orientation and even out their size.
Benefits of Drawing and Orientation
- More Tensile Strength: Polymer chains are aligned so that the fibers can withstand greater tensile force.
- Superior elasticity: Drawing makes the fibers extra supple and strong so they are ideal for uses where flexibility is needed.
- Better Resistance to Wear and Tear: Properly directional fibers resist tearing and tear, ensuring that nylon products can last longer.
4. Fiber Modification and Texturing
Once the nylon fibers have been drawn and aligned, they are available for modification so that they have improved properties and can be matched to particular applications. Fiber modification and texturing are the process by which nylon final properties, including colour, strength, surface texture, and function, are determined.
- Adding Properties to Nylon Fibers
Nylon is a multi-functional material, but the nature can also be treated chemically and physically. Such treatments enhance performance and expand nylon fibre applications.
Dyeing: Addition of Color
The dyeing process is one of the most important fiber processing operations because it makes nylon clothes beautiful. Dyeing may be done during or after spinning fibers.
Solution Dyeing (Dope Dyeing):
- The dye is blended with the melted nylon polymer, and then it is spit out into fibres.
- Makes for stable and permanent colour with anti-fading.
- Mostly for outdoor and industrial applications, where colorfastness is a must.
Post-Spinning Dyeing:
- These fibres or fabrics are coloured once they have been spun.
- Flexible in color options and customization.
- The most used for clothing and bedding.
Benefits of Dyeing:
- Adds color to nylon products.
- Offers color-resistance and fade resistance.
- Brands and Customises it in various fields.
UV Stabilizers: Protection Against Sunlight
Nylon deteriorates under long-term ultraviolet (UV) light by discolouration and mechanical degradation. This is corrected by UV stabilizers in nylon fibers.
Function of UV Stabilizers:
- Absorb or filter harmful UV rays from reducing the polymer chains of nylon.
- Prevent water from leaking through nylon outdoor fabrics (tents, outdoor chairs, fishing nets).
Applications:
- Outdoor gear and equipment.
- Automotive components exposed to sunlight.
- Architectural fabrics and outdoor upholstery.
Moisture-Wicking Treatments
Nylon is hydrophobic (wicks away water), but a moisture-wicking treatment can make it more hydrophobic so that it is better suited to applications where moisture control is essential.
Hydrophobic Coatings:
Chemical treatment of nylon fibre surface to make it more water repellent.
Towick moisture away from the skin and keep the wearer dry.
Applications:
- Activewear and sportswear.
- Outdoor and performance gear.
- Footwear and accessories.
Benefits of Moisture-Wicking Treatments:
Gear Crimping: Fibres go through gears that impart a specific crimp or finish.
Applications:
- Hosiery and stockings.
- Activewear and athleisure garments.
- Upholstery and automotive interiors.
Chemical Texturing
Chemical texturing is when you paint nylon fibres with chemicals to create textures or characteristics.
- Acid Treatments: Enhance roughness or absorption of dye.
- Enzyme Treatments: Alter fiber surface to soften or less pill.
Benefits of Texturing:
- Enhances the touch of the fabric.
- Increases elasticity and stretch.
- – Makes nylon products look better.
5. Weaving and Knitting: Fabric Formation
After nylon fibres are treated and smoothed, they are woven or knitted into cloth. They shape, harden and bend the final nylon cloth.
- Weaving Nylon Yarns
Weaving: weaving is a way of overlapping yarns along a parallel line to weave a dense, tough fabric.
Process:
– Warp (vertical) yarn is laid out on a loom.
To stitch the fabric, the weft (horizontal) yarns go over and under the warp yarns.
The density and stiffness of the fabric depends on the closeness of the weave.
Common Woven Nylon Products:
- Tents: Fiberglass, lightweight nylon is good for outdoor shelters.
- Backpacks: Strength and abrasion resistance.
- Dresses: Applied to windbreakers and rain jackets for its water-repellency.
Benefits of Weaving:
- High tensile strength.
- Resistance to tearing and abrasion.
- Used for use that need to be tough and rigid.
- Knitting Nylon Yarns
Knitting is all about connecting yarns to make a fabric that can stretch.
Process:
- Yarns are spun in different loops — jersey, rib or interlock.
- It’s softer and more elasticity because the loops make it more like weave.
Common Knitted Nylon Products:
- Active Wear: Fitted for mobility in physical activities.
- Hosiery and underwear: Smooth, snug fit.
- Wear For Watersports: Mixes stretch with moisturewicking.
Benefits of Knitting:
- Enhanced flexibility and stretch.
- Soft, comfortable texture.
- Perfect for applications where you want to be able to move.
6. Finishing Processes
Once the material is weaved or knitted, it is then finished in order to improve its properties, look and functionality.
- Heat Setting
Heat setting is a process of using heat to solidify nylon fabric and permanently set it in shape and size.
Process:
- It is a fabric heated on an agitated surface in an oven or under control.
- Heat slacks the polymer chains and locks the cloth in its final position.
Benefits of Heat Setting:
- Relieves shrinkage in washing and drying.
- Maintains fabric dimensions and structure.
- Adds wrinkle resistance and body contour.
- Coating and Lamination
Coating and lamination consists of putting protective or functional layer on the nylon fabric.
Coating:
: A coating of material (polyurethane or silicone) is put on the surface of the fabric.
Gives you water-repellency, fire retardance or antimicrobial effect.
Lamination:
- Fabric or film is interwoven into composite material with multiple layers.
- Enhances durability, insulation, or waterproofing.
Applications:
- Jackets With Water Resistant: Made of water repellent.
- Industries Fabrics: Laminate for extra durability and durability against the elements.
Benefits of Coating and Lamination:
- Increased durability and functionality.
- Protection against environmental hazards.
- Expanded range of applications.
- Quality Control
The process of quality control is a very important process to produce nylon fabric in order to deliver performance.
Examine: The cloth is checked on sight for flecks of uneven dyeing, loom mis-use, or wrinkles.
Mechanical Test: The fabrics are evaluated for tensile, elasticity and abrasion resistance.
Chemical Tests: Measures colourfastness, chemical resistance, UV resistance.
Importance of Quality Control:
- Consistent and reliable in nylon items.
- Reduces waste and production defects.
- Increases satisfaction of customers and product efficiency.
7. Environmental Impact and Sustainable Innovations
This is nylon, a soft, strong material that has become part of everyday life but is also becoming environmentally hazardous. Being a synthetic polymer, derived from petrochemicals, nylon’s manufacture and disposal are not without environmental problems. But in recent years, the textile sector has become a bit more sustainable, with its creation of new manufacturing processes, recycling systems and alternative raw materials. In this section, we will be looking at the sustainability issues with nylon and the sustainable technologies paving its way into the future.
- Environmental Challenges
High Energy Consumption in Production
Even early nylon manufacturing uses a lot of energy. From the raw materials extraction to the polymerisation, petrochemicals are transformed into nylon fibres with a lot of energy.
Energy-Intensive Chemical Processes:
In order to manufacture nylon, it is normally made by highly energetic chemical reactions at high temperatures (condensation and polymerisation). Such reactions are required to make the raw substances such as adipic acid, hexamethylenediamine and caprolactam into the longer polymer chains that make up nylon fibres.
For instance, condensation that makes Nylon 6,6 consists of two monomers reacting at very high temperatures and using up quite a lot of energy.
The same applies to Nylon 6, which is made by ring-opening polymerisation of caprolactam, another process involving high energy.
Impact on Carbon Footprint:
The production process has high carbon emissions – particularly if the energy comes from non-renewable fossil fuels. It’s the source of greenhouse gases and global warming. Nylon production increasingly depends on environmentally friendly energy sources like solar, wind or hydropower when industries look to offset their carbon footprint.
Non-Biodegradability and Microplastic Pollution
The synthetic fiber nylon is composed of petroleum monomers, so it’s non-biodegradable. Because unlike natural fibres like cotton or wool, which can break down over time, nylon can remain on the Earth for centuries.
Persistence in Landfills:
The nylon waste that goes into landfills does not decompose. All this leads to increasing trash and landfill contamination. Even the nylon textile of old clothes, carpets and industrial waste could hang on for decades — eating up space and polluting the environment.
Microplastic Pollution:
The microplastics release that is among the most egregious environmental concerns for nylon. When nylon clothes are washed, and synthetics especially activewear, they release tiny plastic fibres. These microfibers sometimes escape from washing machines and get released into the water supply.
Such microplastics are able to enter the digestive tract of fishes and have detrimental consequences for marine life. In time, the microplastics accumulate in the food chain, possibly into human health as well.
Nylon fibres are one of the most widespread microplastics detected in the oceans and rivers, researchers have found.
Apart from being polluting to the environment, nylon’s petrochemical basis is made from precious fossil fuels that contribute to the issues of resource scarcity and energy use.
- Sustainable Practices in Nylon Manufacturing
The ever-increasing question of the environmental footprint of nylon has led to a lot of innovation in sustainable production of nylon. These sustainable methods are intended to reduce energy, waste and circularity in nylon fabric manufacturing and disposal.
Nylon Waste Recycling: Post-Consumer & Post-Industrial Nylon Recycling, Usage of the Nylon Waste Recycling (Pcw/PI)Nylon.
Recycling is the most efficient way to eliminate the ecological footprint of nylon. By recycling nylon waste, we do not require virgin materials and save energy and water.
Post-Consumer Nylon Recycling:
Post-consumer nylon is any item that has been used once and is disposed of. Fabric waste, clothing and carpets – all of which are often sources of post-consumer nylon residue – are also common sources of these plastics.
Companies are building mechanisms to recover and recycle used nylon into new fibres or goods.
The “Nylon 6 Recycled” is one of them, in which old nylon clothing and textiles are pulverized into raw material for new products. This also saves a lot of garbage from the dumps and gives it a second chance.
Fashions, home textiles and even ropes and fishing nets have been made with recycled nylon.
Post-Industrial Nylon Recycling:
Nylon waste that has been post-industrial is produced in factories that over produce. These can be the scraps of faulty items, bits or scraps of fiber.
There are now techniques that a lot of textile companies are employing to recover and recycle this leftover nylon, which saves material and eliminates waste.
Others are companies that recycle industrial-strength nylon, and use it to make things such as auto parts and industrial fabrics.
Benefits of Recycling:
Cut in virgin nylon use.
- Reduce manufacturing’s ecological footprint.
- Exclusion of waste from landfills & Avoidance of Pollution.
- Nylon made of Bio : Production of Nylon from Renewables.
- Bio-based nylon is one of the most promising futures of sustainable textile manufacturing. Bio-based nylon is made from renewables such as plant oils, such as castor oil, rather than from petrochemicals.
Nylon 6,6 from Bio-Based Resources:
Nylon 6,6 was the old monomers derived from petroleum (adipic acid and hexamethylenediamine). But bio-alternatives are being created using renewable raw materials. Castor oil, for example, takes the place of one of the raw materials that makes nylon, saving fuel.
The chemistry of bio-based nylon is the same as standard nylon and can give the same strength, resilience and versatility with less carbon footprint.
Potential Benefits of Bio-Based Nylon:
- Low Carbon Emissions: Bio-based raw materials are also made from renewable sources so bio-based nylon is carbon-free when compared to normal nylon.
- We can Reduce Reliance on Fossil Fuels: Plant oils reduce reliance on non-renewable fossil fuels that are becoming more and more difficult to access sustainably.
- Agriculture Sustainability: Bio-based nylon fuels the agriculture sector, creating new markets for renewable crops like castor beans, which go into making castor oil.
Examples of Bio-Based Nylon:
- Nylon 6,10: Bio-based nylon that is produced with sebacic acid from castor oil. This product is being used in industries such as textile and automobile industry.
- Nylon 11: Then there’s also Nylon 11, which is made of renewable vegetable oils and is used for automotive components, medical devices, and textiles.
Circular Economy: Ensuring Closed-Loop Processes for the Production and Recycling of Nylon.
The circular economy is all about recycling and reducing waste in closed loop fashion. It is the practice that seeks to reduce the footprint of manufacturing by reusing and recycling materials instead of throwing them away.
Design for Disassembly:
With circular economy, things are engineered for their last use. That’s by making nylon fabrics that can be readily recycled or reused after use.
Manufacturers now concentrate on building goods that can be easily broken down into their constituent parts (for example, separating nylon fibres from other synthetic or natural fibres) and recycled.
Closed-Loop Systems:
Closed-loop makes sure the waste from manufacturing nylon products doesn’t end up in the landfill.
- In this space, we see some “Take Back” programs where consumers can take their reusable nylon products or clothing back for recycling.
- We could also build nylon recycling plants where the after-consumer waste gets transformed into new goods and hence there is no longer any virgin content.
Global Collaborations:
Many large manufacturers are working with environmental groups and communities to find clean ways to dispose of nylon.
There are some examples: Patagonia and H&M are leading the charge in including recycled nylon in their collections and making it easier for consumers to recycle their old products.
Benefits of Circular Economy:
- Least amount of waste being dumped into the landfills.
- Extended lifecycle of materials.
- Waste Management and Save Energy.
8. Applications of Nylon Fabric
Nylon has a huge number of applications across many industries because of its versatility. Fashion, clothing, textiles for factories, carpeting and furniture all rely on nylon for making the things we touch and feel.
- Fashion and Apparel
Polyester has made fashion changing with a lightweight, durable, and flexible replacement for fibers from nature.
Activewear:
Elastane, sturdiness, and wicking ability make nylon great for activewear. Lycra and Spandex (mixed with nylon) fabric used to make gym clothing, yoga pants and running apparel.
Swimwear:
The water-resistance and quick drying nature of nylon make it a favorite material for swimming costumes. It’s easy to lace up, comfortable and resistant to chlorine and saltwater.
Lingerie and Hosiery:
The silky texture and softness of nylon is great for lingerie and socks. It’s stretchable and molds to body shapes for comfort and fitting.
Outerwear:
We usually use nylon in jackets, coats and windbreakers as it’s windproof and lightweight. A good number of outerwear wears also have water repellent coatings for optimal wet-weather performance.
- Industrial Uses
Nylon is also widely used for industrial purposes beyond the runway because of its durability, strength and wear resistance.
Ropes and Cords:
We use nylon in the manufacture of ropes and cords for climbing, sailing and ship-carrying. It is very strong so nylon ropes will not buckle under pressure.
Parachutes:
Nylon is the preferred material for parachutes because it’s tough and light. It’s heavy enough to carry a human body and robust enough to withstand launch and take off.
Fishing Nets:
The water resistance of nylon and the fact that it can be woven into fine but sturdy threads make it great for fishing nets. Commercial and recreational fishing applications use nylon nets as they are durable.
Automotive Components:
Nylon is a strong, heat and chemical resistant material used for parts in vehicles like fuel tanks, air conditioners, and engine parts.
- Home Textiles
The textiles industry for household purposes also employs nylon, whose strength and care-effectiveness are highly sought-after.
Carpets:
We often find nylon in carpets and rugs as it resists staining, abrasion and fade. It is one of the most hardwearing carpet fibers and comes in many colors and textures.
Upholstery:
— The nylon upholstery used for furniture and automobile interiors. It’s durable and wear-resistant, which is perfect for a lot of foot traffic.
Curtains and Blinds:
Curtains and blinds are also made of nylon that is not only durable but also washable. It doesn’t get mildewed or fade, so it’s ideal for use in the home.
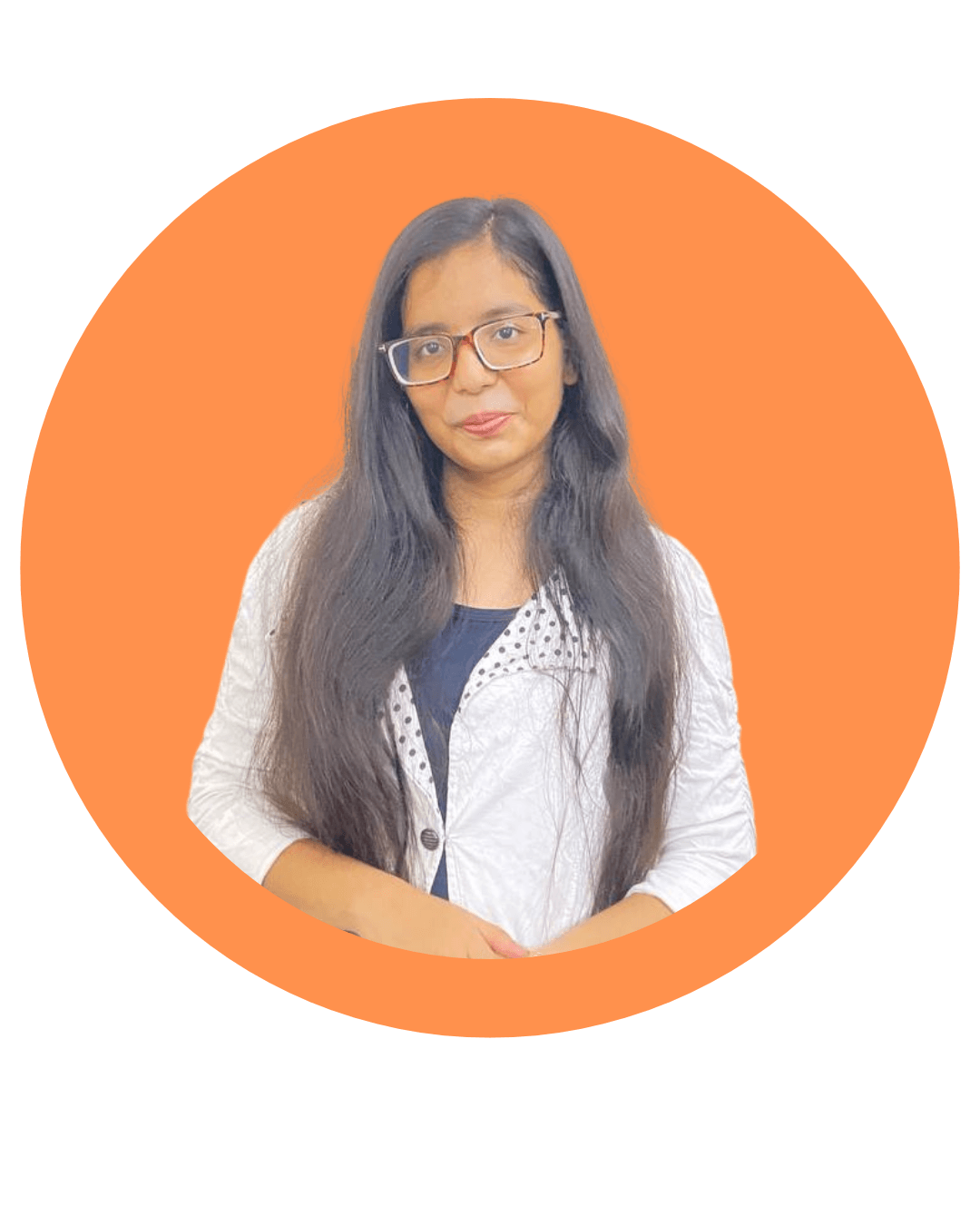
Yashvi Jain, a writer by day and reader by night, is an accomplished content writer and published author of ‘Mind Under Construction. Yashvi possesses extensive knowledge of fabrics, sustainability, and literature. On occasions, you would catch her scripting for her YouTube channel, engrossed in fiction, or ardently dedicating her time to research and storytelling.