Silk, a fabric synonymous with luxury, elegance, and unmatched comfort, has captivated people for millennia. Its shimmering beauty and smooth drape have adorned royalty, graced high fashion runways, and added a touch of opulence to everyday lives. But what lies behind the allure of silk? This article delves into the fascinating journey of silk fabric production, from the humble silkworm to the final exquisite textile.
The Silkworm: Nature’s Wonder Worker

The story of silk begins with a remarkable creature – the mulberry silkworm (Bombyx mori). Unlike its wild counterparts, this domesticated moth has played a pivotal role in human history, providing the raw material for this coveted fabric. Silkworms are meticulously raised in controlled environments, ensuring optimal conditions for cocoon production wearing silk fabric. Their life cycle is a marvel of nature’s efficiency, perfectly adapted for silk creation.
Newly hatched silkworm larvae are incredibly voracious, feeding almost constantly on a diet of mulberry leaves. This specialized diet is crucial, as the mulberry leaves provide the essential nutrients needed for the silkworm to produce the protein that forms silk fibers. During their larval stage, silkworms undergo several moltings, shedding their outer skin to accommodate their rapid growth.
From Caterpillar to Cocoon: The Miracle of Spinning
As the silkworm reaches maturity, a remarkable transformation takes place. It stops feeding and enters a preparatory stage, constructing a small platform of silk threads before embarking on the creation of its cocoon. This is where the magic happens. The silkworm possesses a specialized gland that secretes a protein-based liquid called fibroin. As this liquid emerges and comes into contact with the air, it hardens into a remarkably strong and fine silk fiber.
The silkworm then embarks on a mesmerizing dance, meticulously weaving the silk fiber in a complex figure-eight pattern around itself. This intricate process can take several days, with a single silkworm estimated to produce a staggering 1,000 meters of continuous silk filament! The resulting cocoon is a marvel of natural engineering, a tightly woven shell that protects the developing pupa within.
Harvesting the Threads: Delicate Reeling Techniques
Once the cocoon formation is complete, the silk needs to be extracted – a process traditionally known as reeling. Here, the ethical considerations surrounding silk production come into play. Conventional methods involve stifling the pupae within the cocoon to prevent them from maturing and emerging as moths. This ensures the continuity of the silk filament and maintains its high quality. However, advancements in peace silk production offer a more humane alternative, allowing the pupae to develop before harvesting the cocoons.
The traditional reeling process begins by carefully sorting the cocoons based on quality and size. The cocoons are then placed in basins of hot water. This treatment loosens the sericin, a gummy substance that binds the silk fibers together. Skilled workers, often referred to as reelers, then gently unwind the long strands of silk from multiple cocoons, combining them to form a single thread. This delicate process requires a keen eye and steady hand, as any damage to the silk filament can significantly reduce its quality.
Transformation: From Raw Silk to Exquisite Fabric
The reeled silk, still in its raw form, is a thick and uneven thread. To transform it into the smooth and lustrous fabric we know, further processing is required. The raw silk undergoes a process known as throwing, where multiple strands are twisted together to create a stronger and more uniform yarn. Depending on the desired properties of the final fabric, the silk yarn may then be dyed in a vibrant array of colors or bleached to achieve a pure white hue.
The Art of Weaving: Bringing Silk to Life
The final stage in the silk production process is weaving. Weaving involves interlacing threads at right angles to create a fabric. The type of weave used significantly impacts the final look and feel of the types of silk fabric. For example, a plain weave results in a smooth and even fabric like satin, while a twill weave creates a textured surface with a diagonal pattern, as seen in twill and gabardine. Skilled weavers operate looms, intricate machines that precisely interlace the silk threads according to the desired weave pattern.
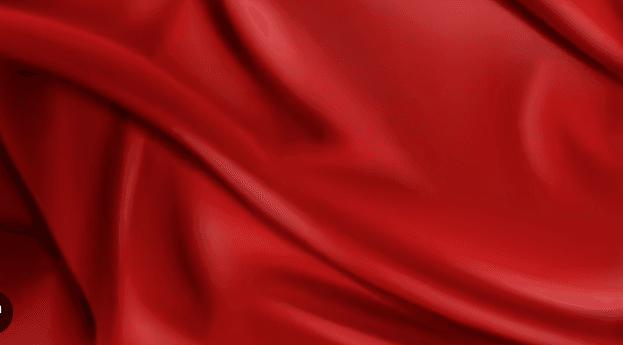
A Look Towards the Future: Sustainable Silk Production
The traditional methods of silk production raise ethical concerns due to the killing of silkworms to harvest the cocoons. However, advancements in peace silk offer a more sustainable alternative. In peace silk production, the pupae are allowed to develop before harvesting the cocoons. This method results in slightly shorter silk filaments, but it aligns with the growing consumer demand for ethical and sustainable fashion practices.
Furthermore, researchers are exploring alternative sources of silk. Some promising developments include the use of spider silk, known for its exceptional strength, and the creation of bioengineered silk using microorganisms. These advancements hold the potential for a more sustainable and ethically sourced future.
Beyond the Fabric: The Diverse Applications of Silk
While silk fabric is undoubtedly the most well-known application of this remarkable material, its uses extend far beyond the realm of fashion. Here are some fascinating examples of how silk is utilized in various industries:
- Medical Textiles: Due to its biocompatibility and hypoallergenic properties, silk finds application in sutures, surgical mesh, and wound dressings. The natural structure of silk fibers allows for controlled drug release and promotes tissue regeneration.
- Acoustics: Silk’s excellent sound absorption properties make it a valuable material for musical instruments and soundproofing applications. The natural fibers help dampen unwanted noise, creating a more controlled and immersive acoustic environment.
- Aerospace and Defense: The exceptional strength-to-weight ratio of silk makes it a potential candidate for use in aircraft components and parachutes. Research is ongoing to explore the use of silk composites in aerospace applications due to their lightweight and high-performance characteristics.
- Optics: Silk can be manipulated to create biocompatible waveguides for transmitting light within medical devices. This opens doors for advancements in minimally invasive surgeries and diagnostic procedures.
The Delicate Balance: Preserving Tradition and Embracing Innovation
Silk production is a fascinating blend of ancient tradition and modern innovation. The meticulous skills honed over centuries by silkworm farmers and weavers remain essential to this day. However, advancements in technology are transforming the industry, from automated reeling machines to sustainable peace silk production methods.
The future of silk looks bright. Research is ongoing to explore various aspects of silk production, including genetic modification of silkworms for increased silk yield and the development of new dyeing techniques that use eco-friendly dyes. Additionally, the growing consumer demand for sustainable fashion practices is pushing the industry towards more ethical and environmentally responsible methods.
A Detailed Look at Different Silk Fabrics:
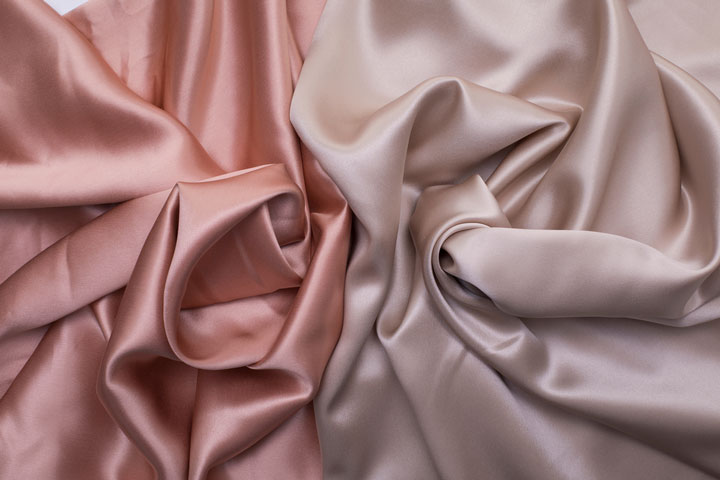
Silk fabrics come in a remarkable variety, each boasting unique characteristics and applications. Here’s a closer look at some of the most popular types:
- Satin: Satin is renowned for its luxurious sheen and smooth drape. The characteristic satin weave creates a fabric where the warp threads (lengthwise threads) dominate the surface, resulting in a lustrous appearance. Satin can be lightweight and delicate for evening wear or heavier and more structured for jackets.
- Chiffon: Chiffon is a lightweight, sheer fabric known for its ethereal quality. The plain weave construction with loosely twisted yarns creates a soft, flowing material that drapes beautifully. Chiffon is often used for scarves, blouses, and evening gowns, adding a touch of elegance and airiness.
- Organza: Organza is a crisp and translucent fabric with a slightly stiff texture. The plain weave with tightly twisted yarns gives organza its signature structure and ability to hold its shape. This makes it ideal for creating voluminous sleeves, structured bodices, and overlays on garments.
- Dupioni: Dupioni is a textured silk fabric with a unique slubbed appearance. This unevenness arises from the use of short silk fibers in the weaving process. Dupioni offers a rich and sophisticated look, often used for bridal gowns, jackets, and upholstery.
- Habotai: Habotai is a plain-weave silk known for its smooth and lustrous surface. The fabric is lightweight and versatile, making it a popular choice for linings, lingerie, and blouses. Habotai can also be dyed in a wide range of colors, adding to its adaptability.
- Velvet: Silk velvet is a luxurious fabric with a short, dense pile that creates a soft and plush feel. The pile is typically made from cut silk fibers, giving the fabric its characteristic depth and richness. Silk velvet is used for high-end garments like evening dresses, jackets, and accessories.
- Brocade: Brocade is a richly woven silk fabric featuring raised patterns or designs. These patterns are created by incorporating extra weft threads during the weaving process. Brocade offers a sense of grandeur and opulence, often used for formal wear, upholstery, and decorative items.
The Global Silk Industry:
Silk production has a long and rich history, with several countries and regions playing a significant role. Here are some of the major players in the global silk industry:
- China: China is the undisputed leader in silk production, accounting for over 70% of the world’s raw silk output. Silk production has been a cornerstone of Chinese culture for millennia, with regions like Jiangsu and Zhejiang renowned for their silk heritage.
- India: India boasts a long tradition of silk production, particularly in the southern regions like Karnataka and Andhra Pradesh. Indian silk, known for its vibrant colors and intricate designs, holds significant economic and cultural importance.
- Japan: Japanese silk is known for its exceptional quality and craftsmanship. Regions like Kanto and Kansai specialize in producing high-grade silk fabrics like satin and kimono silks. The meticulous attention to detail and focus on traditional techniques are hallmarks of Japanese silk production.
- Italy: Italy is a major center for silk processing and manufacturing. The country imports raw silk from other regions and transforms it into luxurious finished fabrics, often adorned with intricate designs and patterns. The fashion houses of Milan are prime examples of how Italian expertise elevates silk into couture masterpieces.
- Vietnam: Vietnam’s silk industry has seen significant growth in recent years. The country focuses on producing high-quality mulberry silk and is known for its beautiful ao dai garments, a traditional Vietnamese dress made from silk.
The global silk industry plays a vital role in the economies of these regions, providing employment opportunities and generating significant export revenue. Silk production also holds cultural significance, with traditions and techniques passed down through generations, weaving a rich tapestry of history and heritage.
The Environmental Impact of Silk Production:
While silk is a natural fiber, conventional production methods do have an environmental footprint. Here are some key considerations:
- Mulberry Leaf Production: The cultivation of mulberry leaves, the primary food source for silkworms, requires significant land use and water resources. Additionally, pesticides used to control pests on mulberry trees can contribute to environmental pollution.
- Water Usage: The silk reeling process utilizes large quantities of water, particularly in the hot water treatment used to loosen sericin. This can place a strain on water resources in regions where water scarcity is a concern.
- Chemical Dyes: Conventional silk dyeing processes often involve harsh chemicals that can pollute waterways. These chemicals can harm aquatic life and contribute to overall environmental degradation.
Initiatives for Sustainable Practices:
Thankfully, the silk industry is recognizing the need for more sustainable practices. Here are some encouraging initiatives:
Peace Silk Production: As mentioned earlier, peace silk allows silkworms to complete their metamorphosis before harvesting the cocoons. This eliminates the need to kill pupae.
- rganic Mulberry Farming: The adoption of organic farming practices for mulberry trees reduces reliance on chemical pesticides and fertilizers. This protects soil health, promotes biodiversity, and minimizes water pollution from agricultural runoff.
- Water-Efficient Reeling Techniques: Innovations in reeling technology are aiming to reduce water consumption during the sericin removal process. These techniques include using closed-loop systems and exploring alternative methods for loosening the sericin.
- Eco-Friendly Dyes: The development of natural dyes derived from plants or recycled materials is gaining traction. These dyes offer a more sustainable alternative to harsh chemical dyes, reducing environmental impact during the dyeing process.
- Life Cycle Assessment: Implementing Life Cycle Assessment practices allows silk producers to identify and address environmental hotspots throughout the production chain. This holistic approach helps minimize the overall environmental footprint of silk production.
The Future of Silk Technology:
Silk, with its remarkable properties, continues to inspire researchers to explore innovative production methods. Here’s a glimpse into the future of silk technology:
- Bioengineered Silk: Scientists are developing methods to produce silk using genetically modified microorganisms. These microbes can be programmed to create silk fibers with specific properties, potentially offering a more sustainable and scalable production method.
- Spider Silk Production: Spider silk is known for its exceptional strength and elasticity, surpassing even the best quality silkworm silk. Researchers are exploring ways to “farm” spider silk by either extracting the silk directly from spiders or utilizing recombinant DNA technology to produce spider silk proteins in other organisms. While challenges remain, spider silk production holds immense potential for high-performance applications.
- Advanced Fabrications: Innovations in 3D printing and biofabrication could revolutionize silk production. These techniques could allow for the creation of complex silk structures with tailored properties, opening doors for new applications in various fields, including medical textiles and bioengineering.
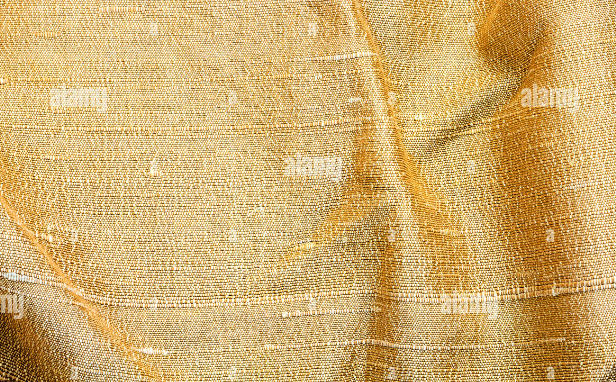
The future of silk production is brimming with possibilities. By embracing sustainable practices and harnessing the power of new technologies, silk can continue to be a source of beauty, luxury, and innovation for generations to come.
A Timeless Legacy Woven in Silk
The journey of silk, from a tiny silkworm to a luxurious fabric, is a testament to nature’s wonders and humankind’s ingenuity. From its historical significance as a symbol of wealth and royalty to its contemporary applications in cutting-edge technology, silk continues to captivate and inspire. As research and innovation continue to shape the future of silk production, one thing remains certain – the allure of silk, a timeless legacy woven in thread, endures.
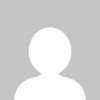